Технологична така конструкція литому деталі, при якій можна виготовити виливок, що відповідає вимогам, пропонованим до точності, шорсткості поверхні, фізико-механічним властивостям і структурі металу при найменших витратах на виробництво. При цьому враховують витрати виробництва при виготовленні виливка й наступної її механічній обробці
Часто на лиття по виплавлюваних моделях переводять деталі, що виготовлялися раніше з кувань, штампованих заготовок або прокату. Ці деталі можуть мати більші безперервні площини, місцеві стовщення, не викликувані умовами їх служби, тверді допуски на розміри, без особливої праці одержувані механічною обробкою, але важко виконувані у виливках. Тому при перекладі на виготовлення деталі литтям по виплавлюваних моделях необхідно змінювати конструкцію її з урахуванням специфіки цього способу, особливо коли в одному виливку поєднують ряд деталей, що з`єднувалися раніше у вузол зварюванням, пайкою або механічним кріпленням
При переході від штампованих або кутих заготовок на виливки по виплавлюваних моделях слід ураховувати також особливості литого металу, механічні властивості якого, як правило, нижче, чим металу обробленого тиском. Для одержання литих деталей, равнопрочних з деталями, обробленими тиском, рекомендують заміняти марку сплаву, наприклад застосовувати для литому деталі низьколеговану сталь замість звичайної углеродистой, з якої виготовляли кування
Нижче розглянуті основні якісні характеристики виливків і викладені рекомендації з них конструюванню
Точність розмірів. Точність розмірів оцінюють по відхиленню дійсного розміру виливка від номінального. Найбільше часто розмірну точність виливків оцінюють класами точності, прийнятими в машинобудуванні, тому що система допусків повинна забезпечувати сполучення й взаємозамінність деталей машин і приладів. Для характеристики системи допусків необхідні посадки, передбачені в ній. Тому питання про точність розмірів виливків повинен зводитися до визначення повних полів розсіювання розмірів і встановленню класів точності застосовуваних систем і допусків, у поля яких вкладаються поля розсіювання дійсних розмірів деталейг. Повне поле розсіювання залежить від допусків на розміри порожнини прес-форми, мінливості (коливання) усадки сплаву, модельної сполуки, властивостей оболонки при різних температурах
Допуски на розміри робочої порожнини прес-форми звичайно не перевищують 3-го класу точності або квалітету 10 (СТ СЄВ 144-75). Погрішність, викликана неточністю виготовлення прес-форми, спостерігається в кожної отриманій по ній моделі й тому є систематичною. Погрішності, пов`язані з коливанням усадки модельної сполуки й металу, а також з об`ємними змінами оболонки при сушінні, нагріванні й охолодженні, є випадковими. Знаючи величину й характер погрішностей, викликуваних кожним фактором, можна встановити методику підсумовування приватних погрішностей і обчислити повні поля розсіювання [8, 28, 29, 90].
Розподіл полів допусків щодо номінальних розмірів деталей, виготовлених немеханічною обробкою, ухвалюють відповідно до системи допусків, використовуваної в машинобудуванні, за ДСТ 7713-62 і СТ СЄВ 145-75, де поля допусків повинні бути спрямовані «у тіло» деталі, тобто для внутрішніх ( розмірів, що охоплюють) А (мал. 1.1, б) зі знаком плюс, а для зовнішніх (охоплюваних) розмірів В (мал. 1.1, а й б) — зі знаком мінус. Для розмірів З, що не ставляться до зовнішніх і внутрішніх, тобто розмірів між осями й від осей, радіусів, виступів і поглиблень, допуски повинні бути двосторонніми, розташованими симетрично щодо номінальних розмірів. Така система дає можливість конструкторам уникнути складних розрахунків розмірних ланцюгів і в ряді випадків виключити механічну обробку й припасування готових деталей при складанні машин і приладів
ДЕРЖСТАНДАРТ 2.307-68 ЕСКД (єдина система конструкторської документації) «Нанесення розмірів і граничних відхилень», у розділі III містить п. 3.1, у якому сказано, що «граничні відхилення розмірів указують безпосередньо після номінальних розмірів, але розміри відносно низкою точності, що багаторазово повторюються на кресленні, є винятком» (мал. 1.2). Граничні відхилення таких розмірів на зображення не наносять, а в технічних вимогах роблять запис, наприклад: «Не зазначені граничні відхилення розмірів внутрішніх — по А
, наруж-
Рис. 1.1. Схеми визначення допуску на товщину стінки деталі: а — простій; б — складної
них — по В
, інших — по CJ2» ( тобто ±1/2 допусків 8-го класу). При такій системі позначення допусків у значній мірі скорочується час на розробку й оформлення робочих креслень готових литих деталей [56].
Відповідно до прийнятої системи допусків у машинобудуванні повне поле допуску на товщину стінки б у простої деталі при певних розмірах А и Б (див. мал. 1.1, а) розташовується «у тілі» стінки (мал. 1.3, а) і позначається D. Допуск на ту ж товщину стінки б у складній деталі (див. мал. 1.1,6) може бути однобічним мінусовим — D, коли товщина стінки б обумовлена конструктором розмірами А и В (мал. 1.1,6), або двостороннім симетричним (мал. 1.3, б), коли стінки обумовлені конструктором розмірами З.
(див. мал. 1.1, б) або двома радіусами З.
Рис. 1.2. Креслення виливка
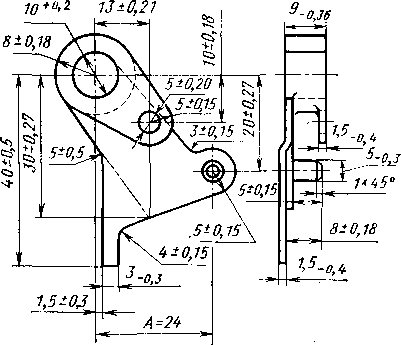
Дослідженнями великої кількості деталей, виготовлених литтям по виплавлюваних моделях, установлене, що розсіювання розмірів товщини стінок виливків у більшості випадків підкоряється закону нормального розподілу. Криві фактичного розсіювання толщин стінок близькі за формою до кривих нормального рас-
Рис.1.3. Розташування повного поля допуску:.
а — однобічне мінусове (у тіло); б — двостороннє симетричне прн F — G; в — двостороннє несиметрично мінусове, при F > G на величину -Х
прерозподілу. Це підтверджує зіставлення кривих розподілу й обчислені критерії згоди Колмогорова. Розмах коливань розмірів окремих елементів толщин стінок ( За/8) 100 у відсотках від середнього арифметичного розміру т
(див. мал. 1.3, в) для застосовуваних толщин стінок становить 21,0-6,3 %.
На підставі встановлених залежностей розроблені нормативи среднеєкономической розмірної точності толщин стінок виливків, виготовлених по виплавлюваних моделях (табл. 1.1).
При дослідженнях установлене, що відбувається відхилення середньоарифметичного розміру тб (див. мал. 1.3, в) «у тіло» стінки на величину -Х
внаслідок деформації (прогину) стінок оболонки форми. Для різних толщин стінок і габаритних розмірів виливків -Х
= 0,12-5-0,72 мм, що становить приблизно 1/4 частину повного поля допуску, зазначеного в табл. 1.1.
відхилення, Що Допускаються, мм, при номінальних толщинах стінок, мм.
Таблиця 1.1.
Нормативи розмірної точності толщин стінок виливків
Найбільші габаритні розміри виливка | від 1 | до 3 | Св. | до 6 | Св. 6 | до 10 | Св. 10 до 18 | Св. 18 до 30 | ||
Клас | До. пуск | Клас | До. пуск | Клас | До-. пуск | Клас | До. пуск | Клас | До. пуск | |
До 30 | 8 | 0,4 | 9 | 0,75 | 10 | 1,5 | * ‘ | |||
30-80 | 8 | 0,4 | 9 | 0,75 | 10 | 1,5 | 10 | 1.8 | - | • — |
80-120 | 9 | 0,6 | 10 | 1,2 | 10 | 1,5 | 10 | 1,8 | 10 | 2,1 |
120-250 | 9 | 0,6 | 10 | 1,2 | 10 | 1,5 | 10 | 1,8 | 10 | 2,1 |
250-400 | 10 | 1,00 | 11 | 1,6 | 11 | 2,0 | 11 | 2,2 | 11 | 2,5 |
400-500 | - | - | 11 | 1,6 | 11 | 2,0 | 11 | 2,2 | 11 | 2,5 |
Припустимі відхиленні розмірів виливків, мм
Найбільші габаритні розміри виливка, мм | Група точності | |||||
підвищена | середня | знижена | ||||
Клас | Допуск | Клас | Допуск | Клас | Допуск | |
До 30 | 4 | 0,13 | 5 | 0,20 | 6 | 0,33 |
30-80 | 5 | 0,30 | 6 | 0,46 | 7 | 0,74 |
80-120 | 6 | 0,54 | 7 | 0,87 | 8 | 1,40 |
120-250 | 6 | 0,72 | 7 | 1,15 | 8 | 1,80 |
250-400 | 7 | 1,35 | 8 | 2,20 | 9 | 3,30 |
400-500 | 7 | 1,55 | 8 | 2,50 | 9 | 3,80 |
Зменшення толщин стінок виливка при литті по виплавлюваних моделях приводить до зниження її маси. Це зниження проти теоретичного (розрахункового) значення може досягати для застосовуваних толщин стінок 3,5-10,5 % і визначається по формулі G = = ( -Х/8) 100. У зв`язку із цим відхилення по масі завжди буде тільки убік зменшення від теоретичного розрахункового. Тому відпадає потреба в нормативах на припустимі верхні відхилення по масі
Внесення нормативів на розмірну точність толщин стінок виливків (див. табл. 1.1) обумовило коректування припустимих відхилень на інші розміри виливків, виготовлених по виплавлюваних моделях (табл. 1.2).
З табл. 1.2 випливає, що в найпоширенішому діапазоні зміни розмірів виливків, виготовлених по виплавлюваних моделях, до 500 мм фактично досяжна точність перебуває в межах 4- 9-го класів стандартів машинобудування СРСР, що відповідає 11- 16-му квалітетам СТ СЄВ 144-75. На окремих контрольованих розмірах, переважно дрібних, може бути отримана й більш висока точність ( до 3-го класу), однак для її забезпечення необхідне дотримання ряду умов, удорожающих і ускладнюючих виробництво (наприклад, використання оснащення високої точності, дорогих формувальних і модельних матеріалів). Крім того, підвищенням вимог до розмірної точності неминуче буде збільшуватися відсівання виливків у шлюб по розмірах. Тому при конструюванні виливків призначення твердих допусків на окремі розміри повинне бути технологічно й економічно виправдане. Точність в основному залежить від контрольованого размфау складності конфігурації й конструктивних особенностей відливки,, .властивостей ливарного сплаву, якості й властивостей модельний,і формрвочнкх Матеріалів, точності застосовуваного оснащення, .якості використовуваного встаткування, точності дотримання оптимальнийтехнологических режимів на всіх операціях — від одержання моделі до л5чищення й термообробки виливків [1].
Як приклад досліджень точності, що фактично досягається, отл ийбк; розглянемо данкце математичної обробки ре-.
.
зультатов виміру розміру А сталевого виливка, зображеної на мал. 1.2. Вимірювали 400 виливків. З порівняння гистограмми із кривої, що вирівнює частоту допусків, мабуть, що закон розподілу допусків близький до нормального закону. Допустимість розбіжностей кривих, що вирівнюють частот і гистограмм визначали за допомогою критерію Колмогорова. Дослідження показали що залежність допусків від розмірів виходить лінійної (мал. 1.4), тоді як у деталей, одержуваних механічною обробкою, вона виражається кубічною параболою. Тому допуски, прийняті в зазначені вище стандартах машинобудування, не узгодяться з допусками при литті по виплавлюваних моделях. Однак систему допусків, застосовувану в машинобудуванні, все-таки використовують. Економічна ефективність цього визначається можливістю застосування парку калібрів, зниженням вартості виливків, а також внаслідок збільшення допусків на розміри деталей, до точності яких пред`являються невисокі вимоги, усуненням шлюбу в механічних цехах, що виникає у зв`язку із застосуванням неправильних схем нанесення розмірів і допусків
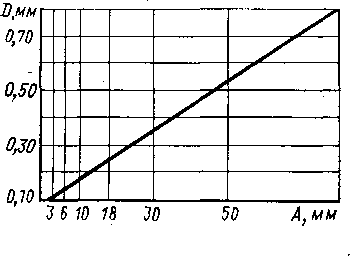
Рнс. 1.4. Залежність допусків D від розмірів виливків
.
Шорсткість поверхні виливків. Для оцінки шорсткості поверхні машинобудівних деталей використовують ДЕРЖСТАНДАРТ 2789-73. Цим стандартом установлені вимоги до шорсткості поверхні виробів, у тому числі з будь-яких металів і сплавів незалежно від способу їх одержання або обробки
Вимоги до шорсткості поверхні встановлюють вказівкою числових значень параметра (або параметрів) і базової довжини, на якій визначають параметр. Стандартом передбачено шість параметрів: три висотні й три крокові. Висотні параметри: Ra — середнє арифметичне відхилення профілю, мкм; Rz — висота нерівностей профілю по 10 крапках, мкм, і Rmax — найбільша висота профілю, мкм. Крокові параметри: Sm — середній крок нерівностей, мм; S — середній крок нерівностей по вершинах, мм, і tp — відносна опорна довжина профілю, %.
Параметр Ra, Що Є кращими иредставляющий собою середнє арифметичне з абсолютних значень, відхилень профілю в межах базової длинидобивают по формулі
де в — відхилення профілю (відстань між будь-якою крапкою профілю й середньою лінією); I — базова довжина (довжина базової лінії, використовувана для виділення нерівностей, що характеризують шорсткість поверхні); п — число обраних для вимірів крапок профілю. Наближений метод, застосовуваний у статистику, дає усереднене значення мікронерівностей. Чим більше вимірів проведене на тому самому ділянці, тем точніше можна визначити Ra.
Позначення шорсткості поверхонь наведені в ДЕРЖСТАНДАРТ 2.309-73. Для виливків по виплавлюваних моделях найбільш характерна шорсткість поверхні від Rz = 20 мкм до Ra — = 1,25 мкм. Шорсткість поверхні виливків, виготовлених по виплавлюваних моделях, в основному тим більше, чим вище шорсткість поверхні робочої порожнини прес-форм і одержуваних у ній моделей, крупней зерна пилоподібного й обсипочного матеріалів, які застосовують для виготовлення першого шару оболонки, вище смачиваемость розплавом матеріалу форми й нижче стійкість останнього проти впливу розплаву і його окислів. Шорсткість поверхні виливків завжди нижче шорсткості поверхні робочих частин прес-форми й моделей і залежить в основному від розмірів зерен пилоподібного - матеріалу. Після хімічної, гідропіскоструминної й дробеметной очищення виливків шорсткість поверхні їх звичайно тим більше, чим крупніше зерна застосовуваних при очищенні матеріалів і нижче твердість поверхні виливка
Поверхневі дефекти, що виявляються після очищення (сліди окислів і полон, засміття, неметалічні включення), погіршують якість поверхні виливків
Шорсткість поверхні визначають, використовуючи прилади, що як безпосередньо стикаються з контрольованою поверхнею («обмацування» її), що так і не стикаються сней.
«, Що Обмацують» прилади високої точності, наприклад профи-лометр — профілограф мод. 201 заводу «Калібр», постачені алмазною голкою з малим радіусом скругления. Коливання голки перетворяться в зміни напруги індуктивним методом. Профилограмма, на якій визначають величину й профіль мікронерівностей, записується приладом у прямокутних координатах. Межі вимірів приладів цього типу Rz = 20--0,025 мкм. Найпоширенішим приладом, що дозволяють контролювати шорсткість поверхні без прикосновенияс їй є подвійний мікроскоп МИС 1$ конструкцій Линника. У цьому мікроскопі використаний принцип *світлового перетину*, так само як і в іншому, що випускається вітчизняною промисловістю приладі ПСС-2.
Шорсткість поверхні виливків іноді оцінюють візуально, шляхом порівняння сєталонами.
Механічні властивості металу виливків. Результати механічних випробувань зразків, вирізаних зі спеціально відлитої
Рнс. 1.5. Граничні значення механічних властивостей сталн 50Л, отримані на 200 стандартні зразках
.
проби, характеризують якість металу або сплаву, що йде на виливки. Однак у більшості випадків ці проби не дають вистави про властивості металу й сплаву в самих виливках. Неоднорідність металу й внутрішні пороки в ньому залежать від товщини стінки, яка по даним аналізу виливків 150 найменувань коливається в межах 1,5-30 мм; частіше зустрічаються стінки товщиною 2, 3, 5, 10 мм. Довжина виливків, як правило, 100-500 мм.
Результати механічних випробувань досвідчених плавок і дані, отримані на заводах, були статистично оброблені по кожній товщині виливка. Як приклад на мал. 1.5 представлені результати статистичної обробки даних про механічні властивості стали 50JI, отриманих на 200 литих зразках круглого перетину (діаметром 5 мм) для випробувань на розтягання й квадратного перетину 10X10 мм із надрізом для випробувань на ударну в`язкість. На малюнку видне, що в 0,2 % зразків з литими поверхнями, підданих випробуванню, тимчасовий опір менш установленого Дст на литу сталь (а
= 580 Мпа), а в 1,7 % зразків межа пропорційності нижче необхідного. Ударна в`язкість менш 0,25 Мдж/м
вийшла в 4,8 % зразків. Найбільше
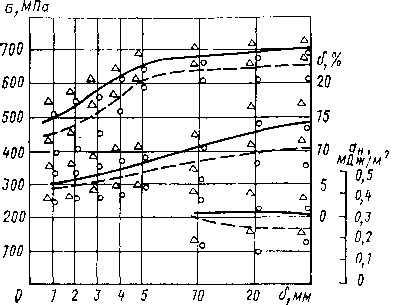
Рис. 1.6. Механічні властивості стали 50J1 у стейках різної товщини:.
Л — заливання знизу; ПРО — заливання зверху; мінімальні значення за Дст В > 580 Мпа; а
= = 0,25 Мдж/м
; 6 > 11 %.
.
число зразків з показниками, меншими встановлених стандартом, має відносне подовження 7,9 % і звуження 16 %.
Оброблені дані по всіх підданих випробуванню виливкам зі стінками різної товщини б представлені на мал. 1.6. Як видне, зі зменшенням товщини стінки механічні властивості стали знижуються; причому при заповненні порожнини форми зверху вони трохи нижче, чим при заповненні знизу. Зниження механічних властивостей литий стали зі зменшенням товщини стінок можна пояснити тим, що порівняно тонкі стінки затвердевают дуже швидко, причому окисли й гази, замішані в рідку сталь при заливанні, не встигають виходити з неї. Крім того, при швидкому затвердінні в тонких стінках може утворюватися пористість усадочного походження, тому що утруднені умови фільтрації рідкої фази
При випробуванні зразка на розтягання розрив відбувається в тому місці, де перебуває найбільший дефект. Прочностние й пластичні властивості стали в цих місцях знижуються, внаслідок підвищення змісту окислів і ємульгированних газів, які утворюються у великій кількості при заливанні форми зверху.
Дослідження показали, що прийнята трефовидная й клиноподібна конструкції проби й узяті зі стандарту значення механічних властивостей литий углеродистой стали не можуть характеризувати дійсні механічні властивості виливків, виготовлених по виплавлюваних моделях. Їх не можна також ухвалювати й для розрахунків при конструюванні виливків, тому що товщина стінок у виливках найчастіше становить 2-5 мм, у той час як товщина проби за Дст прийнято 13-18 мм.
Тільки для елементів виливків, де забезпечене спрямоване затвердіння й достатнє харчування затвердевающей частини, можна прийняти дані Дст. Властивості слід визначати по круглих і прямокутних заготовках-пробам, а не по клиноподібній і трефо-видної пробам. Для більш тонких частин виливка при відсутності спрямованого затвердіння в напрямку З (мал. 1.7, а) значення механічних властивостей у порівнянні зі значеннями, рекомендованими Дст, зменшуються: tf
на 10-20 %; б на 15-25 •%; на 20- 30 %.
Рис. 1.7. Схеми цаправления затвердіння металу у виливках: а — равностенная виливок; б — виливок з напуском; А, У и С — напрямку просування фронту затвердіння
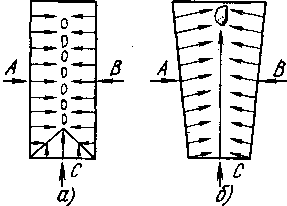
Рис. 1.8. Залежність щільності стали 50JI від напуску на стінці виливка
.
.
У т випадок, коли потрібно забезпечи найбільш висок механічн властивіст метал у певн стінк виливок й висок їхн герметичніст, необхідно створюва спрямован затвердінн метал виливок у форм й достатн харчуванн вони з системи.,
Спрямоване затвердіння може бути забезпечене наступними методами
1.
Конструюванням стінок виливків із застосуванням напусків, как. показане на мал. 1.9, б. Доцільний напуск у межах 5— 10 % висоти стінки (мал. 1.8).
2.
Призначенням відповідних радіусів г у внутрішніх кутах а сполучення стінок виливків або на зовнішніх кутах 1 форми (мал. 1.9).
3.
Призначенням відповідних відстаней а між виливками або їх конструктивними елементами. При порівняно близькому (4—5 мм) розташуванні стінок виливка між собою затвердіння
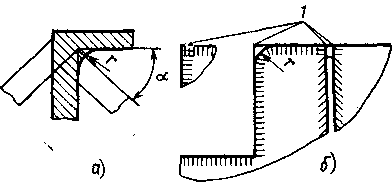
Рис. 1.9. Схема утвору «гарячого» вузла внаслідок перехрещування теплових потоків:.
а — сполучення стінок у виливку з утвором внутрішнього кута; б — «гарячий» гострий кут / на формі й перехресні теплові потоки
відбувається за схемою, показаної на мал. 1.10, а. При цьому осьова} пористість переміщається на поверхні, що взаємно обігріваються, виливків. При розташуванні виливків або їх стінок під кутом 3—5° (мал. 1.10, б) пористість переміщається у верхні виливки, при а > 6 мм пористість переміщається ближче до центру стінки
4.
Застосуванням конічних прибутків-обігрівачів З, розташовуваних між виливками (мал. 1.11). Щоб забезпечити найбільш високі механічні властивості металу у виливках і високу їхню герметичність, необхідно заповнювати форми металом знизу, у положенні, показаному на мал. 1.11, б. Потім форм потрібно поверну на 180°, щоб забезпечи необхідн спрямован харчуванн з системи.,
5.
Управлінням просування фронту затвердіння за схемою (мал. 1.12, а), коли воно відбувається тільки по стрілці при відсутності зародження кристалів на бічних поверхнях у напрямках Л и В. Якщо сплав направленно затвердевает у ливарній формі з відкритою нижньою торцевою частиною ( без ізоляції), яка перебуває в контакті з водоохлаждаемим холодильником (мал. 1.12, б), то у виливку утворюється тонкостолбчатая структура. Якщо спрямоване затвердіння сплаву відбувається в ливарній формі із закритою нижньою торцевою частиною форми (з товщиною ізоляції в 5-6 шарів оболонки форми), то у виливку утворюється крупностолбчатая структура (мал. 1.12, в). При зменшенні числа шарів оболонки форми в.
виливку будуть утворюватися структури проміжні. Для жароміцного сплаву ЖС 6- До була опреде-.
.
Рис. 1.10. Затвердіння двох виливків
а — близько розташованих одна до іншої; пористість вийшла на поверхню при відстані між виливками а = 4 мм; б — розташованих під кутом:
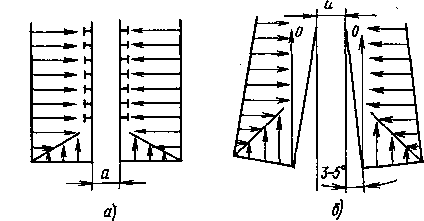
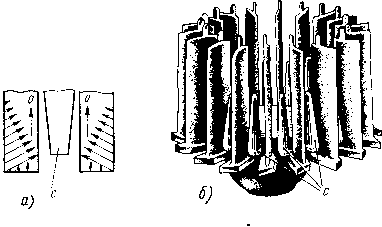
Рис. 1.11. Затвердіння виливків при впливі конічного обігрівача:.
a — схема затвердіння; б — блок лопаток з обігрівачами З
Рнс. 1.12. Спрямоване затвердіння отлнвок: а — схема затвердіння; 6 — з відкритою порожниною; в — із закритою порожниною
.
льону оптимальна стовпчаста структура, завдяки якій ресурс турбінних лопаток збільшений більш ніж в 2 разу