Жаростійкі (окалиностойкие)"стали й сплави характеризуються високою хімічною стійкістю до окиснення при високій температурі [17]. Опір окисненню при високих температурах залежить від хімічного складу сталей і сплавів, стійкості окісних плівок, що утворюються на їхній поверхні, і сполуки газового середовища, у якому відбувається окиснення. Жаростійкі сталі й сплави близькі по основних складових до коррозионно-стійким сталям, але містять більша кількість легуючих елементів і мають більш складну фазову сполуку. Зі збільшенням змісту хрому підвищується окалиностойкость сталей
Стали, що містять 10—13 % Сг, мають гарну жаростійкість до температури 750 °С; утримуючі 15—18 % Сг — до 900 С°; утримуючі 22—25 % Сг — до 1100 °С. Присадка до хромистих і хромонікелевих сталей і сплавам алюмінію, кремнію й невеликої кількості титану, ніобію, бериллия, ще більше підвищує жаростійкість
Підвищенню жаростійкості сприяє утвір на поверхні металів і сплавів тугоплавких, щільних окісних плівок у результаті сполуки хрому, нікелю, алюмінію, кремнію з киснем. Ці плівки щільно прикривають поверхня сплаву й перешкоджають двосторонній дифузії атомів кисню й металу (див. табл. 2.4).
Жароміцні сталі й сплави (див. табл. 2.5) відрізняються властивістю протистояти пластичній деформації під впливом напруг при високій температурі [99].
На жароміцність великий вплив виявляє природа твердого розчину основи сплаву, її температура плавлення й тип кристалічної решітки. Чим вище температура плавлення основи, тем вище жароміцність сплаву. Сплави аустенітного типу на основі заліза
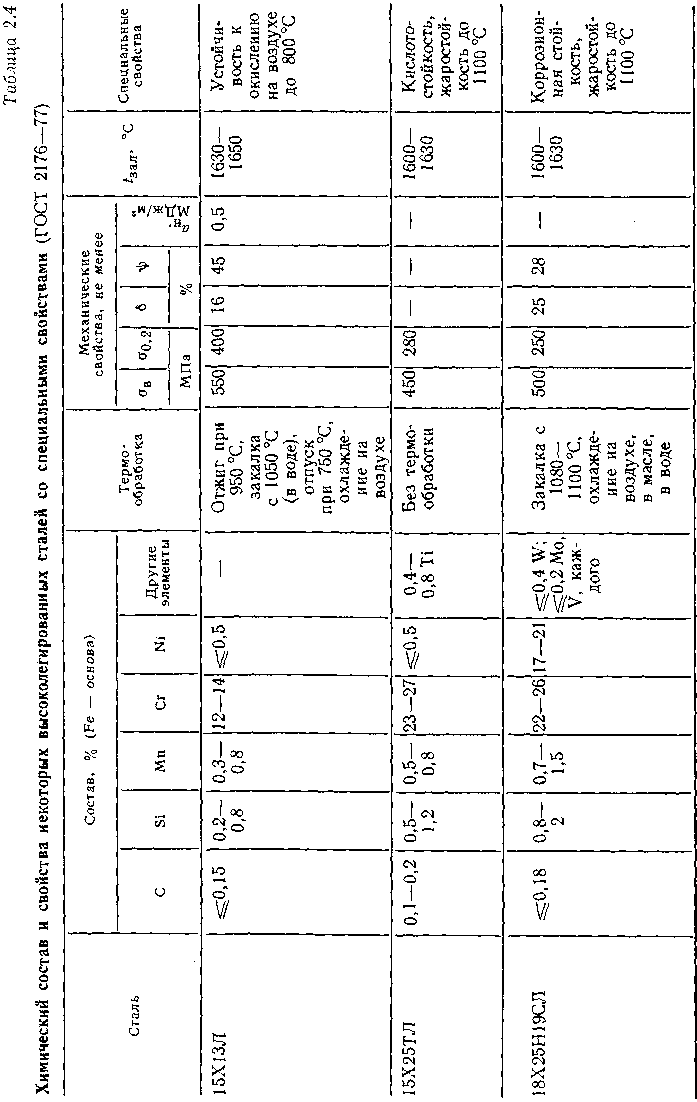
Примітки. 1. У всіх зазначених сталях допускається зміст до 0,3 % Си.
2.
У сталі 15Х13Л повинне бути % Р; у сталях 08Х14Н7МЛ н 16Х18Н12С4ТЮЛ повинне бути .
у всіх інших сталях —
< 0,3S і 0,35Р.
3.
У сталей зазначених марок вільна лінійна усадка 1,7—2,5 %, задовільні жндкотекучесть, зварюваність, гарна».
оброблюваність різанням
Сполука, % | Термо. обра. ботка | ||||||||
Сплав | Fe | Ni | З | Сг | Si | Мп | Інші елементи | ||
20Х26Н19С2Л | Основа | 18 — 20 | 23 — 27 | 2-3 | 0,5-. 1,5 | Загартування з 1100 °С, охолодження у воді | |||
40Х9С2Л | Основа | 0,35 — 0,5 | 8—10 | 2 — 3 | 0,3 — 0,7 | Без термообробки | |||
20X21 Н46В8Л | Осталь. ное | 43 — 48 | 0,1—0,25 | 19 — 22 | 0,2-. 0,8 | 0,3-. 0,8 | 7 — 9 W; | Старіння при 900 °С, витримка 5 год, охолодження на повітрі | |
жсз-дк | Осталь. ное | 0,07 — 0,12 | 11 — 14 | 2,8 Ti;. 4.5 А1;. 4.5 Мо;. 4.5 W; 8 З;. 0,02 В, 0,02 Рє ( з розрахунку) | Загартування з 1215 °С, витримка 4 год, охолодження на повітрі | ||||
ЖС 6- ДО | Осталь. ное | 0,13 — 0,2 | 9,5-. 12 | 0,4 | 0,4 | 3 Ti;. 5 А1;. 4 Мо;. 5 W;. 5 З. 0,02В; 0,015 Рє ( з розрахунку) | Загартування з 1220 °С, витримка 4 год, охолодження на повітрі | ||
АНВ300 | Осталь. ное | 14 — 17 | 1,4—2 Ti, 7,0-10 W, 4,5 — 5,5 А1 | Загартування з 1120 °С, витримка 10 год, охолодження иа повітрі |
Примітки. 1.У сплавах АНВ300В, ЖС 6- ДО.ЖСЗ-ДК утримується: 8. Для сплавів щільність
Механічні властивості, ие менш | **зал* | Лннейная вільна усадка, % | Спеціальні властивості,. призначення | |||||||
t випробувань, °З | а в | а 0,2 | а 100 | 6 | S. l4 | |||||
МПа | % | |||||||||
20 | 500 | 250 | - | 25 | 28 | - | 1600—1620 | 2,5 | Жаростійкість до 1100°С. Соплові лопатки ГТД | |
Не нормуються | 1560 — 1600 | 2,3 | Жаростійкість до 800 °С. Жароміцність до 700 °С. Соплові вінці турбокомпресорів | |||||||
20 | 450 | 6 | 8 | 1600 — 1620 | 2,4 | Жаростійкість до 1000 °С. Жароміцність до 800 °С. Деталі двигунів і газових турбін (робітники й соплові лопатки й ін.) | ||||
20. 900 | 900. 700 | 800. 500 | 290 | 5. 6 | 8. 8 | 0,3 | 1560 — 1620 (у вакуумі) | 2,3 | Жаростійкість до 1100 °З, жароміцність до 1000 °С. Робочі турбінні колеса ГТД | |
20. 900 | 900. 800 | 830. 500 | 320 | 1,7. 5 | 6. 8 | 0,1 | 1580 — 1650 (у вакуумі) | 2,3 | Жаростійкість до 1100 °С. Жароміцність до 1000 °С. Робочі соплові лопатки й колеса ГТД | |
20 850 | 950. 700 | - | 240 | 1. 1,8 | 3. 1,5 | — | 1540-1600 (у вакуумі) | 2,3 | Жаростійкість до 1000 °С. Жароміцність до 950 °С. Робітники й соплові лопатки ГТД невеликої потужності |
із гранедентрированной решіткою мають більшу жароміцність, чому сплави ферритного типу з об`ємноцентрованою решіткою
Підвищенню жароміцних і інших властивостей сталей і сплавів сприяє також легування. Найбільший ефект досягається при одночасному легуванні багатьма елементами. Уведення таких елементів, як алюміній, титан, вольфрам, молібден, ніобій, бор, сильно збільшує опір сплавів пластичної деформації при високих температурах внаслідок утвору високодисперсних интерметаллидних фаз і блокування площин ковзання при виділенні цих фаз із твердого розчину. Крім того, присутність цих елементів у твердому розчині затримує дифузійні процеси, і сплав при високих температурах не разупрочняется.
При введенні великої кількості легуючих елементів у сплави поряд з підвищенням їх жароміцності знижується пластичність і погіршується їхня ковкість. Тому найбільш жароміцні литі сложнолегированние сплави з гетерогенною структурою. Тому що такі сплави мають високу твердість, в`язкість і важко обробляються, застосування лиття по виплавлюваних моделях є більш доцільним методом для виготовлення деталей складної форми, наприклад лопаток турбін і соплового вінця, крильчаток, робочих коліс і лопаток турбокомпресорів
Властивості жароміцних сплавів залежать від чистоти шихтових матеріалів, застосовуваних при плавці, і методів рафінування. Сірка із шихти, при підвищеному її змісті, вступаючи в сполуку з нікелем, утворює легкоплавку євтектику (температура плавлення 645 °С), яка розташовується по границях зерен, у результаті чого знижується жароміцність сплаву. Ще більшою мірою знижуються жароміцні властивості сплавів при забрудненні їх легкоплавкими домішками (вісмут, свинець, сурма й ін.), що попадають із шихти. Тому шихту ретельно перевіряють, а розплав у процесі плавки рафінують [36, 87].
Жароміцність грубозернистих сталей і сплавів більш висока, чому дрібнозернистих. Для литих деталей з жароміцних сплавів характерна крупнозернистость.
Сплави прийнято вважати жаростійкими, якщо при даній температурі за 100 год випробувань у повітряному середовищі збільшення маси зразків внаслідок утвору окалини не перевищує 1 г/см
в 1 ч.-Сплави вважають жароміцними, якщо при даній температурі за заданий строк випробувань вони зберігають необхідний рівень міцності. Жароміцні й жаростійкі сталі й сплави здебільшого мають також термостійкість, тобто стійкістю до впливу навантаження в умовах частої зміни температур (нагрівання — охолодження).
Магнітними називають сплави, що володіють магнітними властивостями: магнітною проникністю й сприйнятливістю, залишковою індукцією й коерцитивною силою. Магнітна проникність характеризує властивість сплаву пропускати магнітний потік. Магнітна сприйнятливість характеризує здатність сплаву до намагничи-.
Химическиб сполука деяких ливарних магнітних сплавів ( ДЕРЖСТАНДАРТ 17809-72)
Сплав | Сполука (основні компоненти), % (Fe — решта) | ||||
А1 | N1 | Си | З | Інші елементи | |
ЮНД4 | 13-14 | 24-25 | 3-4 | 0,2-0,3 Ti | |
ЮНТС | 13-16 | 32-35 | - | - | 1-1,5 Si, 0,4-0,5 Ti |
ЮНДК15 | 8,5-9,5 | 19-20 | 3-4 | 14-15 | 0,2-0,3 Ti |
ЮНДК18 | 9-10 | 18-19 | 3-4 | 18-19 | - |
ЮНИЙ14ДК24 | 7,5-8,5 | 13,5-14,5 | 2,5-3,5 | 23,5-24,5 | - |
ЮНДКЄ1ТЗБА | 6,8-7,2 | 13-13,5 | 3-3,5 | 30,5-31,5 | 3-3,5 Ti 0,9-1,5 Nb |
ЮНДК40Т8АА | 7,2-7,7 | 14-14,5 | 3-4 | 39-40 | 7-8 Ti |
Примітка. У позначенні марок сплавів букви наприкінці марки означають: А — стовпчаста кристалічна структура; АА — монокристалічна структура
ванию. Залишкова індукція характеризує ступінь залишкової намагніченості сплаву після зняття магнітного поля. Коерцитивна сила являє собою значення напруженості магнітного поля, необхідного для того, щоб звести до нуля залишкову намагніченість у магнітних сплавах. Хімічний склад магнітних сплавів, застосовуваних при литті по виплавлюваних моделях, наведений у табл. 2.6.