В умовах діючого виробництва у зв`язку з можливими змінами властивостей вихідних матеріалів або повернення звичайно періодично контролюють міцність, вільну лінійну усадку, теплотривкість і плинність сполук, а у випадку застосування їх у пастообразном стані — і зміст замішаного до складу повітря 141, 48].
Визначення лінійної усадки модельного, сполуки. Методика визначення вільної й утрудненої лінійної усадки модельної сполуки полягає у вимірі зміни довжини зразка в певному інтервалі температур. Усадку модельної сполуки виражають впроцентах.
Величину вільної лінійної усадки можна з достатньою точністю визначити на зразках квадратного перетину 10X10 мм і довжиною 200 мм, виготовлених у прес-формах конструкції, представленої на мал. 5.5. Прес-форма має міліметрову шкалу, нанесену уздовж робочої порожнини. Величину усадки замірять приладом за допомогою ноніуса на вставці 5, що вільно переміщається в робочій порожнині прес-форми. Вставка при запресовуванні модельного
Рис. 5.5. Прилад конструкції Вниинмаш для вимірів вільної лінійної усадки модель-них сполук:.
/ — корпус; 2 — кришка; 3 — робоча порожнина; 4 — запресувальний отвір; 5 — вставка з ноніусом для вимірів усадки; 6 — штовхальник для вилучення зразка; 7 — запірне обладнання кришки; 8 — опори
.
сполуки перебуває усередині прес-форми, яку заповнюють сполукою у вертикальному положенні через запресувальний отвір 4. Вільну лінійну усадку обчислюють по формулі
де l
- довжина робочої порожнини прес-форми, рівна довжині зразка відразу після запресовування модельної сполуки; 1
- довжина зразка після завершення усадки (у момент виміру), певна за допомогою вставки 5.
За методикою Ниитавтопрома вільну лінійну усадку визначають на зразку у вигляді усіченого конуса приладом, показаним на мал. 5.6. Робоча довжина зразка 100 мм. Корпус 1 приладу являє собою водоохлаждаемую сталеву прес-форму. У верхній частині її перебуває,-датчик 2, установлюваний перед уведенням мо* ділової сполуки в крайнє верхнє положення, фиксируемое засувкою 3. Одночасно стрілка індикатору 4 установлюється на нуль.’ Модельна сполука запресовується при горизонтальному положенні прес-форми, потім її ставлять вертикально й замірять усадку, коли стрільця індикатору протягом 30 хв показує ту саму величину
Випробовується не менш двох зразків, причому усадка їх не повинна мати коливань більш 0,08 %. Для визначення коливань вільної й утрудненої усадок І. І. Горюновим застосований спеціальний зразок (мал. 5.7). З кожної випробуваної модельної сполуки необхідно виготовити при однакових умовах (температура прес-форми, тиск пресування й ін.) по 10 зразків і обмірити їх:.
Рис. 5.6. Прилад конструкції Ниитавтопрома для вимірів чи-иейиой усадки модельних сполук:.
/ — корпус; 2 — датчик; 3 — засувка; 4 — індикатор; 5 — водяна сорочка; 6 — робоча порожнина;
Відвід
Води
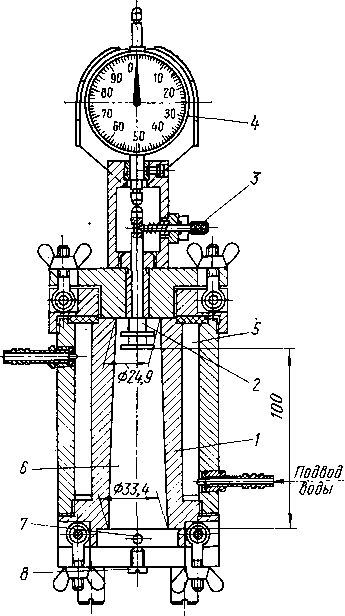
7 — запресувальний отвір; 8 — місце установки термометра (гвинт віддаляється).
На основі результатів вимірів зразків визначають коливання усадки по формулі
ДО
[(-шах
-Х
)!Х
] 100 о/о,.
де X
, Х
- максимальний і мінімальний розміри моделі, мм;
- контрольований розмір порожнини прес-форми
Визначення міцності. Найбільше поширення у вітчизняній і закордонній практиці одержали прочностние випробування модельних сполук на статичний вигин. При цьому одночасно може бути визначена стріла прогину зразка, що побічно характеризує пластичність сполуки. Для досліджень можуть бути застосовані спеціальні прилади для випробувань на статичний вигин і розривні машини невеликої потужності з фиксируемими навантаженнями до 200-500 Н и ціною розподілу шкали не більш 0,5 Н, постачені реверсорами. Один з варіантів конструкції реверсора показаний на мал. 5.8.
За методикою Ниитавтопрома випробування проводять на машині РМ-3 з використанням реверсора спеціальної конструкції. Для випробувань кожної модельної сполуки відбирають до 10 зразків, що не мають зовнішніх дефектів (тріщин, вм`ятин, утяжин, спаїв, раковин, кривизни, незаповнення контуру, вкраплень сторонніх домішок і ін.). Результати випробувань зразків, у зламі яких виявлені внутрішні дефекти, не враховують. Звичайно випробовують зразки квадратного перетину 6X6 мм і довжиною 60 мм, а відстань між опорами реверсора становить 50 мм. Для виготовлення зразків застосовують прес-форми, один з варіантів конструкції яких представлений на мал. 5.9. Після випробувань замірять фактичні розміри поперечного переріза зразка в місці
-. V | |||||
1 1 | |||||
fs | 50 | ||||
- *- | і | 1 -«- | 1 | ||
V.. | 1 | ||||
1 | |||||
& | |||||
700 | f |
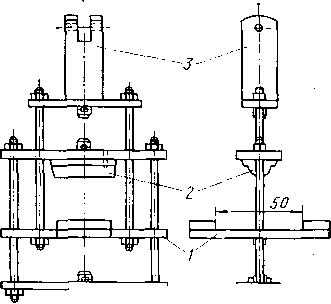
Рис. 5.7. Зразок для визначення сво- Рис. 5.8. Реверсор для випробувань проч. бодиой і утрудненої усадок модельного ности модельних сполук на вигин:.
сполуки / _
р
майданчик; * 2 — ніж; 3 —-.
верхня тяга; 4 — иижняя тяга
зламу з точністю до 0,05 мм. Межа міцності (МПа) підраховують по формулі
M
/W = 3Pl/(2bh
),.
де M
— згинальний момент, викликаний руйнівним навантаженням; W — модуль (момент) опору вигину; Р — навантаження, що викликає руйнування зразка при вигині; I — довжина розрахунки-
Kj
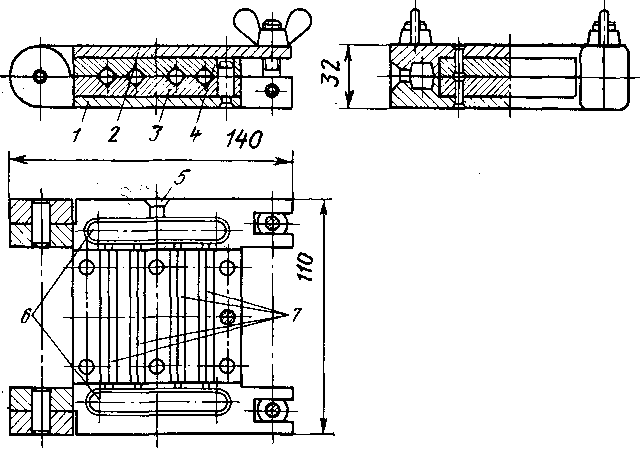
Рис. 5.9. Чотиримісна прес-форма для виготовлення зразків з модельних сполук для випробувань иа вигин:
1 — ннжняя половина; 2 — верхня половина; 3 — нижннй вкладиш; 4 — верхній вкладиш; 5 — запрессовочиое отвір; 6 — колектори; 7 — робочі порожнини прес-форм

Рис. 5.10. Зразок прямокутного сечеиия для испита* иия міцності модельних сполук при розтяганні
.
.
ного ділянки зразка (відстань між опорами); b — товщина зразка в місці зламу; h — висота зразка в місці зламу
Зразки випробовують при постійній температурі (звичайно 20 °С) і термостати-руют при цій температурі протягом 2 ч. За результатами випробувань не менш трьох зразків установлюють середнє значення межі міцності при вигині. Випробування на вигин — не єдиний метод оцінки міцності модельних сполук. За методикою, розробленої у МВТУ ім. Н. Є. Баумана, міцність при розтяганні перевіряли на зразках круглого перетину (типу гагарінських), виготовлених у багатомісній прес-формі, і випробовували на розривній машині з використанням спеціальних захоплень. У НИИТАвтопроме для випробувань на розтягання був застосований зразок прямокутного перетину (5x5 мм у робочій частині), зображений на мал. 5.10. Конструкція зразка забезпечує зручність і надійність кріплення його взахватах.
Визначення твердості. Показник твердості при випробуваннях на пенетрометрі — глибина занурення в досліджуваний зразок сталевої голки під дією постійного вантажу за певний час. Глибину занурення умовно позначають Н
і виражають у міліметрах. Пенетрометр має столик для установки зразка в горизонтальному положенні в стійку, по якій кронштейн вільно пересувається нагору й униз. На консолі кронштейна перебуває бойок з голкою. У пальцеву канавку бойка для втримання його у зведеному (верхньому) положенні входить спеціальний фіксатор. Зразок для випробувань має форму шайби товщиною не менш 10 мм зі строго паралельними підставами, поверхня яких повинна бути гладкої. Шток з вантажем опускають поворотом фіксатора, при цьому голка поринає у випробуваний зразок. Після закінчення 10 з по індикатору з точністю до 0,01 мм фіксують величину занурення голки в зразок. Випробовують не менш трьох зразків з кожного. досліджуваного модельного -сполуки й визначають середнє значення Я
Визначення термічного розширення. Для визначення використовують прилад конструкції НИИТАвтопрома (мал. 5.11). Показником термічного розширення є відношення збільшення довжини зразка при нагріванні до його первісної довжини, виражене у відсотках
де М — приріст довжини зразка, мм; 1
— початкова довжина зразка ( при температурі 20 °С), мм,.
Рис. 5.11. Прилад для визначення термічного розширення модельної сполуки
.
Прилад складається з корпуса 1 з бічними стінками 2, між якими розташований роликовий конвеєр 3, задньої стінки 4, компенсатора 5 і важеля 6, з укріпленим на ньому індикатором 7. Зразок 9 довжиною 150 мм із поперечним перерізом 10X10 мм установлюють на роликовий конвеєр 3 впритул до задньої стінки 4; другий кінець зразка впирається в подушку 8, надягнуту на індикатор. За допомогою компенсатора стрілку індикатору встановлюють на нуль при початковій температурі випробувань (20 °С). Потім прилад зі зразком переносять у термостат, де температуру поступово підвищують. Після підвищення температури на кожні 5 °С дають витримку для прогріву зразка протягом 30 хв, після чого фіксують показання індикатору, що дозволяє графічно зобразити хід процесу розширення
Від кожного різновиду модельною сполуки випробовують не менш трьох зразків і результати випробувань усредняют. До недоліків цього методу ставиться те, що нагрівання приладу й індикатору в процесі випробувань несприятливо позначається на точності їх, а температурний інтервал випробувань обмежений через те, що вірогідність даних залежить від стану зразка. Найменше розм`якшення його буде приводити до деформацій, що спотворюють результати випробувань. Більш достовірні дані про розширення модельних сполук можна одержати при дилатометричних випробуваннях, або за методикою, розробленої в МАТИ, з використанням тензометрії
Визначення стійкості модельних сполук до деформації при температурі 20 °С и нагріванні (теплотривкості). Стійкість сполук До деформацій під дією власної маси при кімнатної
Рис. 5.12. Схеми випробувань модельних сполук на теплотривкість
.
і підвищених температурах оцінюють або стрілою прогину б
зразка, кінці якого лежать на двох опорах (мал. 5.12, а), або відстанню 6
, на яке опускається кінець консольно розташованого зразка (мал. 5.12, б). Випробування при підвищених температурах ведуть у термостаті. Розміри зразків, відстань між опорами 1
або довжина консольної частини 1
, а також тривалість витримки при заданій температурі для одержання порівнянних результатів при всіх випробуваннях повинні бути постійними
Для контролю теплотривкості модельних сполук у Ниита-Втопроме розроблений прилад (мал. 5.13). Випробування полягають у визначенні температури, при якій прогин зразка квадратного перетину 6x6 мм, довжиною 120 мм при відстані між опорами 100 мм досягає 2 мм під дією власної маси. Прилад,.
у гнізда якого встановлюють для випробувань одночасно три зразки, ставлять у термостат з терморегулятором, що підтримують температуру повітря в місці установки зразків з точністю ±1 °С. Для контролю температури в державку приладу поміщають термометр 6, ртутна голівка якого розташована між двома сусідніми зразками. Випробування легкооплавких воскообразних модельних сполук на парафіновій основі починають, звичайно з температури (28 ± 1) °С. Прогин про-
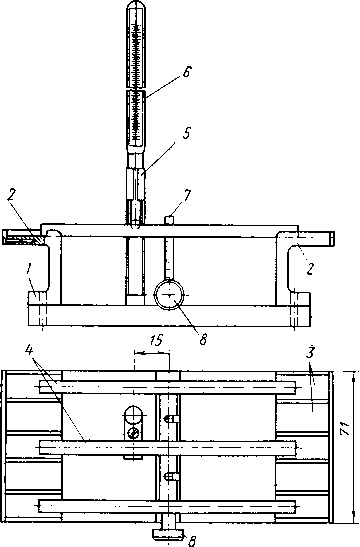
Рйс. 5.13. Прилад для визначення temio-стійкості модельних сполук за методикою НИИТАвтопромй:.
1 — підстава; 2 — опори для зразків;.
3 — гнізда для установки зразків; 4 — зразки; 5 — державка для термометра; 6 — термометр; 7 — міліметрова лінійка для вимірів деформації зразків;.
8 — поворотна шпилька для підведення лінійки до зразка
Рис. 5.14. Прес-форма для визначення плинності модельних сполук (а) і розміри зразка (б).
.
раздов контролюють після двогодинної витримки при заданій температурі за допомогою міліметрової лінійки 7, подводимой до зразка поворотною шпилькою 8. Якщо прогин зразка при початковій температурі випробувань не досягає 2 мм після двогодинної витримки, то температуру повітряного середовища в термостаті підвищують на 2 °С и повторюють виміри після витримки протягом 2 годин. Випробування продовжують, підвищуючи щораз температуру прогріву зразка на 2 °С, поки не буде досягнута температура, при якій прогин середньої частини зразка досягнеться 2 мм. За температуру теплотривкості ухвалюють таку, яка на 1 °С нижче температури, що викликала деформацію зразка на 2 мм.
Визначення плинності. Її визначають для оцінки здатності модельної сполуки при заданих параметрах процесу виготовлення моделей (температури й стану модельної сполуки, тиску запресовування) заповнювати порожнину прес-форми
За методикою НИИТАвтопрома оцінюють плинність по довжині спирали, що виходить при запресовуванні модельної сполуки в спіральну порожнину прес-форми
За методикою МАТИ плинність модельної сполуки в пастообразном стані оцінюють довжиною циліндричного східчастого зразка змінного перетину, виготовленого в прес-формі (мал. 5.14), загальна довжина робочої порожнини якої 400 мм. Порожнина складається із чотирьох сполучених, концентрично розташованих циліндричних частин рівної довжини (100 мм), діаметр яких послідовно зменшується від 10 до 2 мм. Сполуку запресовують
Рис. 5.15. Прилад МАТИ для визначення плинності модельних сполук
у порожнину більшого діаметра при горизонтальному положенні прес форми. Максимальні розміри зразка, які можуть бути отримані при високій плинності модельної сполуки, показані на мал. 5.14, б. З метою одержання більш точних характеристик і порівнянних результатів плинність модельної сполуки визначають на установці (мал. 5.15), що полягає з ультратермостата I, запрес-совочного обладнання з постійним тиском пресування II і описаної вище прес-форми III (мал. 5.14).
Ультратермостат обслуговує запресувальне обладнання; циліндр його має сорочку, порожнину якої гнучкими шлангами з`єднана з термостатом. У процесі роботи його рідина-теплоносій безупинно циркулює в порожнині, утвореною сорочкою циліндра. У такий спосіб підтримується постійна температура циліндра, що й завантажується в нього модельної сполуки. Цю температуру можна регулювати в широких межах (20—180 °С). Для створення постійного тиску на Поршень обладнання, що пресує, використаний видозмінений лабораторний копер (типу 031). Вантажна платформа копра опускається на шток-поршень, створюючи постійне навантаження протягом усього періоду пресування. тиск, що пресує, можна регулювати зміною вантажу, установлюваного на платформу копра
Тривалість затвердіння й швидкості охолодження модельної сполуки в прес-формі можуть бути визначені за методикою НИИТАвтопрома за допомогою приладу, показаного на мал. 5.16. Прилад складається із прес-форми 1 для виготовлення зразка східчастої форми, що полягає з п`яти кубічних частин, розташованих, що симетрично й мають послідовно зменшувані поперечні переріза 30x30; 20 х20; 15x15; 10хЮ й 5x5 мм. У прес-формі
Рис. 5.16. Прилад для визначення часу затвердіння й швидкості охолодження модельної сполуки впресс-форме.
є п`ять різьбових отворів 2 для вгвинчування температурних датчиків 4, підключених до електронного потенціометра 3. Модельна сполуку запресовують збоку, у порожнину кубика більшого об`єму. Перед запресовуванням установлюють датчик так, щоб кінець його перебував у середній частині, утворюючи перетин контрольованої товщини. Відраховують тривалість охолодження за допомогою секундоміра, що включається в момент закінчення запресовування. Відлік часу продовжують доти, поки стрілка потенціометра не покаже температуру на 3 °С нижче температури теплотривкості досліджуваної модельної сполуки. Можливе нагрівання або охолодження прес-форми водою до оптимальної температури
Дослідження реологических властивостей модельних сполук дозволяють об`єктивно оцінити поведений їх при виготовленні моделей. Перші систематичні дослідження реологических властивостей модемних сполук були проведені в ИПЛ АН УРСР А. С. Лакеевим і Г. П. Борисовим. Мди й результати цих досліджень описані в роботі [38]. Для визначення найбільш важливих структурномеханических характеристик модельних сполук використовували модернізований капілярний віскозиметр АКВ-2М, удосконалений прилад К.-2, звичайно застосовуваний для визначення міцності консистентних мастильних матеріалів, а також пластометр конструкції П. А. Ребиндера. Визначали або розраховували за результатами експериментальних досліджень статичне й динамічне граничні напруги зрушення, найменшу пластичну в`язкість зруйнованої структури, жидкоподвижность, пластичність потоку маси, пластичну міцність структури. Експериментально підтверджене, що модельні сполуки можна розглядати як дисперсні системи з коагуляционним утвором структури. Результати досліджень використані як для оцінки реологических властивостей різних модельних сполук, так і для оптимизаций рецептур ебставов ЙПЛ, а також для встановлення onffi-мальних умов роботи з ними, наприклад, при визначенні необхідної температури шароподібної сполуки при запресовуванні
При дослідженнях реологических властивостей модельних сполук для визначення дійсної в`язкості й граничної напруги зрушення може бути використаний ротаційний віскозиметр РВ-8 конструкції М. П. Воларовича, застосовуваний при дослідженнях суспензій
Визначення змісту повітря в пастообразних сполуках
Найпростішим методом є відбір проби готової модельної сполуки, наприклад, за допомогою циліндричного пробника, розплавлювання проби й визначення різниці об`ємів зразка з пастообразного сполуки з повітрям і монолітного зразка тієї ж маси. Опис методики визначення змісту повітря в модельній сполуці, запропонованої в НИИТАвтопроме, наведене в роботі [48 J.
Визначення стійкості модельної сполуки до взаємодії його_зі сполучним розчином. За методикою МАТИ зразки, що мають форму пластин, витримують у розчині сполучного. Тривалість витримки вибирають відповідно до максимально можливої у виробничих умовах тривалості контакту непросохлої суспензії з поверхнею моделі, але не болег.
24 ч. Стан поверхні зразків оцінюють візуально. Потім оглядають злам зразків для визначення можливих змін у поверхневому шарі модельної сполуки. Далі перевіряють зольність модельної сполуки й порівнюють із зольністю зразків, що не мали контакту зі сполучним. Визначають також (зважуванням на аналітичних вагах) зміна маси зразків до й після випробувань
За методикою НИИТАвтопрома зважений зразок модельної сполуки (~15 г) занурюють у розчин сполучного й витримують протягом 2 год при контактній температурі, а потім поміщають у киплячу воду на 2,5 ч. Воду прохолоджують, модельна сполуку знімають із її поверхні, досліджують кислотне число, температуру краплі-падіння й зольність модельної сполуки. За результатами досліджень судять про стійкість модельної сполуки при взаємодії зі сполучним. Плавкість, зольність, коксівність, кислотне число, число омилення визначають стандартними Методами. Наприклад, плавкість оцінюють температурами плавлення або каплепадения, обумовленими відповідно за ДСТ 4255—75 і ДЕРЖСТАНДАРТ 6793—74, зольність- за ДСТ 1461—75, кількість води, що втримується, — за ДСТ 2477-65, кислотне число —■ за ДСТ 5985-79, коксівність (на приладі ЛК.Н-70) за ДСТ 8852-74, число омилення — за ДСТ 21749-76. Дотепер актуальна проблема створення найбільш обґрунтованих і об`єктивних уніфікованих методів досліджень і контролю модельних матеріалів і централізованого виробництва приладів для них проведення
Процес виготовлення моделей у прес-формах включає підготовку прес-форми, уведення в її порожнину модельної сполуки, витримку моделі до затвердіння, розбирання прес-форми й витяг моделей, а також охолодження моделей до температури виробничого приміщення
Використовують звичайно один з наступних способів заповнення прес-форм модельною сполукою: вільним заливанням розплаву; заливанням під тиском розплаву або суміші розплаву з порошком твердого наповнювача; запресовуванням у пастообразном стані; заливанням під тиском пластифицированних (, що розм`якшуються нагріванням) гранул компактного або, що спінюється термопласта; вдмухуванням або засипанням гранул матеріалу, що спінюється при наступному прогріві (водою, парою і т.д.).
В окремих виняткових випадках моделі для одержання штучних виливків можна виготовити обробкою різанням із блоків спіненого полістиролу
Підготовка прес-форм. Прес-форми очищають (протирають, обдувають), змазують їхню робочу поверхню, збирають, у ряді випадків підігрівають або прохолоджують. Очищення, тобто видалення часток модельної сполуки, що залишилися в поглибленнях і отворах порожнини прес-форми, роблять звичайно обдуванням стисненим повітрям. Сполука, прилиплий до прес-форми, видаляють дерев`яними счищалками. Протирають прес-форми марлевим або ватяним тампоном. Великі й складні прес-форми змазують перед кожною операцією. При виготовленні з пастообразних сполук на парафіновій основі дрібних, нескладних за формою моделей, можливо періодичне змазування прес-форм через 10—12 запресовувань. У якості мастильного матеріалу використовують чисте трансформаторне масло, або касторове масло, змішане з етиловим спиртом у співвідношенні 1:1 для зменшення в`язкості. В умовах масового виробництва моделей на напівавтоматичних і автоматичних агрегатах змазування прес-форм здійснюється обдуванням їх робочих поверхонь масляною емульсією
{.
При ручному виготовленні моделей мастильний матеріал наносять тонким рівним шаром за допомогою ватяного або матер`яного тампона. Густий і нерівномірний мастильний матеріал викликає утвір на поверхні моделей раковин, складок, шорсткості і є причиною неточного виконання контурів моделі, особливо гострих крайок
Температура прес-форми виявляє важлив якість, що часто вирішує вплив на, моделей, особливо при виготовленні моделей вільним заливанням. Прес-форми перед початком роботи звичайно підігрівають уведенням у них модельної сполуки. При цьому перші (одна-дві) моделі направляються впереплав.
Оптимальна температура прес-форми залежить від властивостей сполуки й форми моделей. Наприклад, для парафіново-стеаринових сполук вона перебуває в межах 22—28 °С, Коливання температури прес-форми викликають зниження розмірної точності моделей, а низька температура її збільшує внутрішні напруження в моделях і приводить до жолоблення й утвору тріщин вних.
За час розбирання для вилучення моделі й складання прес-форми звичайно не встигають остудитися до оптимальної температури. Тому застосовують примусове охолодження їх за допомогою натурального або штучного льоду, обдуванням, поливанием водою, зануренням у воду, пропущенням холодної води через спеціальні порожнини в прес-формах. Останній спосіб є найкращим в умовах масового виробництва
Виготовлення моделей запресовуванням з пастообразних сполук,
утримуючих повітря. Цей метод був уперше застосований і знайшов найбільше поширення у вітчизняній практиці. Пастообразний модельна сполука запресовується за допомогою різноманітних обладнань — від найпростішого ручного шприца до складних багатопозиційних машин-автоматів
Ручні шприци застосовують у лабораторіях, а також у досвідченому виробництві. Переважніше застосовувати шприци, місткість Kq-Горих достатня для заповнення модельною сполукою декількох прес-форм. Однак слід ураховувати, що чим більше діаметр шприца, тем сутужніше вручну створити необхідний тиск. На практиці прийняті наступні оптимальні граничні розміри, ручних шприців: діаметр поршня 25—50 мм, довжина робочої частини циліндра 100—250 мм, діаметр випускного отвору шприца 2—6 мм.
Випускний отвір повинний бути можливо більшого діаметра. При малому діаметрі заповнення форми відбувається повільно, що приводить до переохолодження модельної сполуки, утвору спаїв і інших нерівностей на поверхні моделі, нечіткому виконанню контурів, особливо в тонких частинах і гострих кутах. Крім того, при малому діаметрі випускного отвору шприца збільшується швидкість струменя модельної сполуки, що сприяє захопленню повітря й утвору раковин у моделях. Відомі випадки, коли тільки збільшенням діаметра цього отвору вдавалося повністю усунути шлюб моделей. Тиск на модельну сполуку при запресовуванні вручну становить звичайно 0,1—0,4 МПа.
Шприци виготовляють із углеродистой конструкційної сталі. Робочі поверхні циліндра-і поршня притирають. Перед початком роботи корпус і поршень шприца підігрівають до 40—50 °С и надалі підтримують цю же температуру. Заповнення шприца усмоктуванням модельної сполуки можливо тільки за умови застосування рідкої пасти й у випадку, якщо поршень і циліндр ретельно притерті друг до друга. Частіше застосовують спосіб наповнення шприца спеціальною лопаткою (ложкою).
У цехах серійного виробництва для виготовлення моделей з пастообразних сполук одержали поширення малогабаритні установки, що полягають із пастоприготовительного й запресувального обладнань. Останнє складається із циліндра, що пресує, або шестеренного насоса, що й обігрівається гнучкого щлацга зі шприцом на його
Рис. 5.17. Шприци пістолетного типу для запресовування модельної сполуки
.
кінці. Звичайно застосовують шприци пістолетного типу різних конструкцій (мал. 5.17 і 5.18). Такі обладнання використовують для заповнення прес-форм різної місткості
Прес-форми встановлюють на стаціонарних або обертових столах. Для заповнення прес-форми штуцер 6 (мал. 17, а й б) притискають до її ливникового отвору, після чого натисканням на рукоятку 7 відкривають доступ модельної сполуки зі шланга в прес-форму. Шланг 1 і корпус шприца (мал. 5.17, а) обігрівають дротовим нагрівальним елементом потужністю 25 Вт при напрузі не більш 36 В. Гнучкий шланг складається з рукава 3 з маслоустойчивой гуми й двох тканевих прокладок 4 я 5, між якими поміщений нагрівальний елемент 2. Зверху шланг обмотується кіперною стрічкою
.
На мал.. 5.18 показаний шприц конструкції РПЗ. Перевагою його є наявність удосконаленого обладнання для включення й можливість регулювання тиску. .
Установка із шестеренним насосом сконструйована й застосована на Іжевськом машинобудівному заводі, а потім модернізована у Вниилитмаше (мал. 5.19). Вона придатна не тільки для сполук на основі парафіну, але й для сумішей з більш високою температурою пастообразного стану, наприклад типу МАИ, що є позитивною відмінністю цієї установки від інших
У верхній частині станини 1 установлений шестеренний насос 3, що приводиться в рух від електродвигуна 2 через систему клиноремінних передач. На цій же станині змонтовані стіл 9 для установки прес-форми, бачок 5 для модельної сполуки з водяною сорочкою 6, шприц (вузол А) і система трубок, що обігріваються, з`єднують між собою бачок 5, шестеренний насос і шприц
Для готування пастообразного сполуки в бачок наливають рідку сполуку. Вода в сорочці бачка підігрівається за допомогою єлек-
Рис. 5.18. Шприц конструкції РПЗ із регульованим тиском:.
1 — носок; 2 — корпус шприца; 3 — рукоятка шприца; 4 — обмежник; 5 — фіксатор кута повороту рукоятки крана; 6 — рукоятка краиа; 7 — шкала перемикання крана; 8 — корпус краиа; 9 — микровиклю-чатель; 10 — сполучна гайка; 11 — пастопровод.
.
троспирали, що дозволяє точно регулювати температуру й під-держивать її постійної. Модельна сполука з бачка по трубці 4 засмоктується шестеренним насосом, шестірні якого обертаються із частотою 60 про/хв і переганяють сполука по трубці 8 у корпус шприца ( через зазор 13 у порожнину 14) і з неї через трубку 7 знову в бачок 5. У процесі такої перегонки модельна сполука нагріває робочі порожнини установки (насос, шприц, трубки), прохолоджується й протягом 8-15 хв стає пастообразним.
Прес-форму 10 ставлять на стіл 9, який завдяки гвинтовому обладнанню може переміщатися у вертикальному напрямку. Лійку літника прес-форми підводять до наконечника шприца. При цьому за допомогою золотникового обладнання в шприці отвір трубки 8, що підводить модельну сполуку від шестеренного насоса, сполучається ( як показано на малюнку) з отвором 15 у трубці шприца, через яке модельна сполука нагнітається в порожнину пресс-формв Наконечник шприца оснащений електропідігріванням
У процесі запресовування тиск модельної сполуки регулюють зміною зазору 13 між трубкою 8 і золотником 11. Надлишок сполуки, безупинно подаваного насосом, приділяється через зазор 13 у поворотну трубку 7. Після заповнення прес-форми тиск модельної сполуки починає підвищуватися, у результаті чого піднімається клапан 16. При опусканні прес-форми пружина 12
Рис. $.19. Установка із шестеренним насосом для готування модельної сполуки й И4* готовления моделей
опускає Золотник, отвір у шприці перекривається й сполука знову починає надходити тільки в бачок#. Для заповнення витрати модельної сполуки в бачок Періодично додають розплав у суміші зі здрібненою твердою сполукою. В описаній установці внаслідок постійної, циркуля&ин модальної сполуки й безперервного переме* шивания його шестеренним насосом досягається висока якість модельної паед.
У зв`язку з розвитком масового виробництва лиття по виплавлюваних моделях з`явилася істотна необхідність у високопродуктивних автоматичних машинах для виготовлення виплавлюваних моделей
Автоматичні установки для виготовлення моделей з пастообразних сполук (див. мал. 5.2) одержали найбільше поширення у великих цехах масового виробництва дрібних, переважно сталевих виливків. Вони включають агрегати для плавлення компонентів модельної сполуки, готування модельної пасти й запресувальне обладнання, об`єднане з карусельним столом в один автоматичний агрегат. Усі установки агрегату випускає Тираспольський завод ливарних машин ім. С. М. Кірова. Обладнання для готування пастообразного модельної сполуки розглянуті
Рис. 5.20. Карусельний автомат мод. 653
Рис. 5.21. Головний вид автомата мод. 653.
вище. Карусельний автомат мод. 653 для виготовлення модельних ланок показаний на мал. 5.20. Технічні характеристики його наступні: продуктивність 190-360 ланок у годину, розміри поверхонь для кріплення прес-форм 250 х 250 мм, найменша відстань між плитами для кріплення прес-форм 250 мм, темп роботи сгола 10-14-29 з, число встановлюваних прес-форм 10, хід рухливої плити не менш 160 мм, витрата повітря не більш 50 м
/год, витрата води 3—4 м
/год, тиск стисненого повітря не менш 0,5 МПа, зусилля змикання 10 кН, габаритні розміри 3700 х2900 х Х1400 мм. Головний вид автомата показаний на мал. 5.21.
Карусельні столи в комплекті установок для виготовлення моделей можуть бути успішно нспользовани в умовах серійного й масового виробництва виливків різної форми й розмірів. Конструкції застосовуваних карусельних столів можуть бути класифіковані по ступеню механізації привода стола й операції по складанню й розбиранню встановлених на ньому прес-форм, по циклу роботи столів, їх розмірам, числу розташовуваних на них прес-форм і т.д. В умовах серійного виробництва застосовують столи з ручним приводом
Для точного збігу наконечника запреееовочного обладнання й отвору в прес-формі столи постачені фіксаторами, що періодично зупиняють стіл у певному положенні. Вода для охолодження прес-форми подається через обладнання в порожньої осі стола. За останні роки ВКВ точного лиття в Тирасполі спроектоване, а заводом ливарних машин ім. С. М. Кірова освоєне у виробництві універсальне встаткування для готування модельних сполук і виготовлення моделей в умовах дрібносерійного й серійного виробництва. Так, створена напівавтоматична лінія мод. 6A5Q для автоматизованого готування воскоподобних модельних сполук у пастообразном стані, заповнення ними прес-форм, призначених для ручного розбирання й складання, а також регульованого виборчого охолодження заповнених прес-форм. Лінія може працювати по трьом режимам з найбільшою продуктивністю відповідно до 32, 125 і 250 запресовувань у годину й витратою модельної сполуки до 32 л/ч. Найбільші розміри прес-форм у площині рознімання 350 х250 мм. Тиск пресування 0,1—0,3 МПа, температуру модельної сполуки на виході із шестеренного змішувача можна регулювати в межах 40—60 °С. Довжина лінії 4300 мм, ширина 3500 мм, висота 2300 мм.
Установка мод. 6А54 призначена для виготовлення моделей в умовах дрібносерійного й серійного виробництва. Експлуатація установки можлива в складі напівавтоматичної лінії мод. 6А50, а також при роботі в комплекті з будь-який шприцмашиной, аналогічної застосовуваної в цієї лгинии й навіть при використанні ручних шприців
Моделі з розплавлених і напіврідких сполук без замешива-ния в них повітря широко застосовують у закордонній практиці. У порівнянні з моделями,-виготовленими з воскообразних сполук, що містять замешенний повітря, суцільнолиті моделі мають проч-ность в 1,3-1, 5 рази вище, ббльшую твердість і поверхня кращої якості. Однак одержання стабільних по властивостях паст без повітряних включень становить труднощі, запресовування таких сполук ускладнюється, а при використанні розплавів у мо-делях з`являються усадочні дефекти, для попередження утвору яких використовують Підпресування затвердевающего модельної сполуки під тиском 10 Мпа, а іноді й більш.
Для складних моделей змінного перетину зі стовщеними вузлами, вилученими від місця підведення модельної сполуки, більш ефективна подача стисненого повітря у модель, що формується. Повітря при правильному виборі моменту поддува створює усередині моделі порожнини, підпресування через які ще не затверділого повністю пластичної модельної сполуки, запобігає утворенню зовнішніх усадочних дефектів, підвищує точність і стабільність розмірів моделей. Однак, що утворюються усередині порожнечі небажані для деяких моделей з тонкими частинами, тому що внаслідок зниження міцності можлива їхня поломка, наприклад, при видаленні моделей із прес-форм і нанесенні на блоки шарів суспензії. До недоліків монолітних щільних моделей ставиться те,.
.
Рис. 5.22. Пристосування для запресовування рідкої модельної сполуки
.
що вони більш теплопроводни, чому виготовлені з воздухоеодержащих пастообразних сполук, досить чутливі до коливання температури повітря у виробничих приміщеннях, яке викликає в них об`ємні зміни. Це особливо небезпечно в період формування оболонок, тому що може викликати розтріскування ще неміцних її шарів
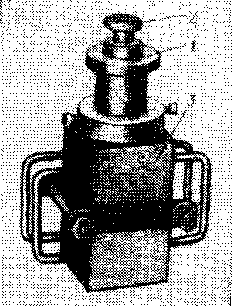
Щільні монолітні моделі виявляють також значний тиск на оболонку форми при нагріванні в процесі виплавления (перед розплавлюванням моделі).
Пристосування для запресовування рідкої модельної сполуки під поршневим тиском (мал. 5.22) складається із циліндра 1 і точно підігнаного до нього поршня 2, виготовлених зі среднеуглеродистой конструкційної сталі. Зібрану прес-форму 3 установлюють на стіл преса. Циліндр 1 підігрівають до температури,близької до температури розплавленої модельної сполуки, і встановлює на прес-форму; потім у неї через циліндр заливають модельна сполука так, щоб він заповнив усю порожнину прес-форми й
/
об`єму циліндра. Після цього в циліндр вставляють попередньо підігрітий поршеиь 2, на який давить шток преса
Тривалість витримки модельної сполуки під тиском становить від декількох секунд до 4-5 хв; її вибирають із урахуванням температури й властивостей модельної сполуки, форми й розмірів моделі, розмірів ливникового ходу в прес-формі. Вона повинна бути не більш того часу, протягом якого модельна сполука повністю затвердевает у ливниковому каналі прес-форми
При виготовленні моделей зі сполук з підвищеною в`язкістю, що й швидко твердіють, наприклад типу Кпсц, під тиском уводять усю шрцию модельної сполуки, необхідну для заповнення прес-форми. Для цього використовують циліндр 1 запресувального обладнання такої місткості, щоб сполуки, що перебуває в ньому, з надлишком вистачило на заповнення прес-форми й компенсацію усадки. Прц підготовці до запресовування між прес-формою 3 і циліндром 1 прокладають тонкий папір, який перекриває отвір циліндра. При запресовуванні папір проривається й модельна сполука заповнює порожнину прес-форми
Для запресовування застосовують важільні, гвинтові, пневматичні й гідравлічні преси. Найбільше поширення одержав пневматичний настільний прес (мал. 5.23). До підстави 1 болтами прикріплений кронштейн 4, на якому встановлені робочий циліндр 7 і золотниковий механізм 3. У порожнину циліндра через золотникове обладнання підводять стиснене повітря, тиск якого 0,4-
Рис. 5.23. Пневматичний прес для виготовлення моделей
.
0,6 Мпа. При повороті рукоятки 2 униз відкривається доступ через кран 8 стисненого повітря у верхню камеру циліндра. При цьому повітря з нижньої камери циліндра виходить в атмосферу через спеціальний отвір. Поршень 6 через шток 5 натискає на поршень запресувального обладнання. Модель витримують під запресувальним тиском до 10 кн, після чого поворотом рукоятки 2 відкривають доступ стисненого повітря в нижню камеру циліндра й одночасно вихід дл повітря в атмосферу з верхньої камери. Поршень преса зі штоком піднімається при цьому нагору у вихідне положення
Становить інтерес спосіб виготовлення моделей із застосуванням вакууму й тиску. Схема машини, призначеної для виготовлення складних тонкостінних моделей із застосуванням вакууму й тиску, наведена на мал. 5.24. Тут же показана модель ротора 9, виготовлена на цій машині. Прес-форму 4 установлюють на стіл 3, який за допомогою пневмопривода піднімають нагору. При цьому прес-форму притискають до верхньої плити 5 машини так, щоб сполучилися ливниковий хід у прес-формі й отвір у плиті для підведення модельної сполуки. Знизу на прес-форму насувають кожух 2, що переміщається за допомогою повітряних циліндрів 8, що й щільно притискається до плити 5. Гумова прокладка в місці стику забезпечує герметичність сполуки
З кожуха 2 через трубку 1 откачивается повітря, а після створення вакууму через запресувальне обладнання 7 з ковзним клапаном 6 запресовують модельна сполука в порожнину прес-форми. Завдяки розрідженню в порожнині форми й тиску на модельну сполуку вдається одержати складні моделі без дефектів і з високою точністю розмірів ( як модель 9, показана на малюнку).
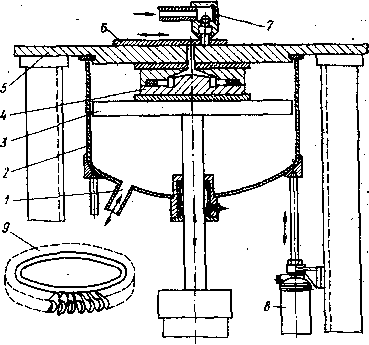
Рис. 5.24. Схема машини для виготовлення складної тонкостінної моделі із застосуванням вакууму й тиску