Плавка металів і сплавів характеризується складними физикохимическими процесами,що протікають при високих температурах. Процес плавки складається з фізичних перетворень вихідних матеріалів і хімічних реакцій, у яких беруть участь складові сплаву й флюси, а також грубні гази й футеровка печей. Сутність цих процесів докладно викладена в роботах, присвячених теорії металургійних процесів і виробництву сплавів. Тут наведені тільки найважливіші відомості про особливості технології плавки сплавів, широко застосовуваних при литті по виплавлюваних моделях
Залежно від роду футеровки сталеплавильних печей плавку стали ведуть основним або кислим процесом. Основна футеровка печей дозволяє виплавляти сталь зі зниженим змістом фос-.
фора й Сірки, що досягають застосуванням активних шлаків з високим змістом перевести
Фосфор — шкідливий елемент у сталі. Він утворює фосфіди заліза, витісняє вуглець із карбідів заліза, надає сталі властивості холодноламкості. Реакції окиснення фосфору й дефосфорації йдуть у розплавленому металі (гомогенна реакція) і на поверхні роздягнула метал-шлаки (гетерогенна реакція).
У печі з основний футеровкой окис кальцію зв`язує пятиокись фосфору в хімічно стійку сполуку — тетрафосфат кальцію (СаО)
-я Р]> перехідне вшлак.
Сірка — також шкідливий елемент у сталі. Сульфіди заліза, не розчиняючись у твердому розчині, утворюють тендітну євтектику по границях зерен і викликають червоноламкість сталі в інтервалі температур 800—1200 °С. Процес видалення сірки (десульфурация стали) відбувається в присутності високоосновного активного вапняного шлаків при високій температурі
Кисла футеровка печей руйнується основним вапняним шлаками, тому вапно при кислої футеровке застосовують в обмеженій кількості. Кислі шлаки тугоплавки, малорухомі. Вилучити фосфор і сірку в печах з кислої футеровкой практично неможливо. Однак сталеплавильні печі з кислої футеровкой мають переваги перед печами з основний футеровкой у довговічності й меншої вартості
Підбираючи шихту з малим змістом сірки й фосфору, можна успішно вести плавку в печах з кислої футеровкой. При плавці спеціальних сталей з високим змістом марганцю, нікелю, титану, алюмінію й зі строго обмеженим змістом кремнію відбувається насичення сплаву кремнієм, що відновлюються з кислої футеровки, що неприпустимо.
".
Пр-І виплавці марганцовистих сплавів кисла футеровка швидко руйнується, тому що закис марганцю, реагуючи із кремнеземом футеровки, утворює легкоплавкий силікат марганцю. Алюміній і титан відновлюють кремній з футеровки. Никелевохромовие сплави, виплавлювані в кислій печі, забруднюються мелкодисперсними включеннями кремнезему («кремениста каламуть»), які іноді нерозрізнені під мікроскопом, але, розташовуючись між первинними кристалами, сильно знижують ударну в`язкість сплаву й погіршують його пластичні властивості. Тому такі сталі й сплави плавлять у печах з основний футеровкой.
У виробництві лиття по виплавлюваних моделях сталь плавлять без окиснення, найчастіше методом переплаву в електричні індукційні печах
Для плавки без окиснення ретельно розраховують шихту й становлять її зі свіжого сплаву й повернення або при необхідності зниження змісту вуглецю в сталі — з 70-80 % повернення й 20-30 % низьковуглецевої сталі (0,1 —0,15 % З; % Р).
Шихту розплавляють при максимальному нагріванні металу. До розкислення приступають після розплавлювання шихти й доведення стали по хімічному складу. При розкисленні відбувається відновлення
мал. 7.1. Схема індукційної плавильної печі підвищеної частоти з машинним перетворювачем
.
закиси заліза, розчиненої як у металі, так і в шлаках. Крім того, раскислители легуючі елементи, що частково відновлюють, перебувають у шлаках у вигляді окислів. Відновлені легуючі елементи знову переходять вметалл.
Обладнання й робота індукційних печей підвищеної частоти. Індукційні плавильні печі підвищеної частоти (1000-2500 Гц) широко застосовують у цехах лиття по виплавлюваних моделях. З такою частотою й працюють сучасні установки з машинними й тиристорними перетворювачами. На мал. 7.1 наведена схема печі з машинним перетворювачем. До трубчастого індуктора, охолоджуваного водою, що протікає всередині нього, підводять змінний електричний струм, який, проходячи по індуктору, створює змінний магнітний потік, пролизивающий футеровку печі й завантажені в тигель шматки металевої шихти. Виникаючі в металі вихрові струми нагрівають шихту до розплавлювання
Печі з машинним обертовим перетворювачем складаються з наступних основних вузлів: печі 1 з індуктором, конденсаторних батарей 2, збудника 3 до перетворювача підвищеної частоти 4 електродвигуна 8, що обертає перетворювач, електромонтаж* ний, вимірювальної, блокувальної й пускової апаратури (на схемі не показані).
Властиво піч являє собою каркас із ізолюючими про* кладками, усередині якого укріплений індуктор. Ізолюючі прокладки необхідні для того, щоб навколо ийдуктора каркас печі не утворював замкнених контурів, що запобігає витоку енергії в каркас. Тигель, розташований усередині індуктора, набивають футі-ровочной масою по конусному металевому шаблонові. Шаблони роблять із листового желаза (зварені). Невеликі шаблони виймають із печі після набивання. Шаблони в печах великої місткості розплавляються при першій плавці. Каркас печі укріплений на станині й обертається на дапфах, навколо зливального носка печі. Поворот печі здійснюється електротельфером, гідроприводом або черв`ячним поворотним механізмом за допомогою штурвала
Індуктор печі являє собою мідну трубку у вигляді котушки з розрахунковим (по потужності установки) числом витків. По індуктору пропускається змінний електричний струм підвищеної
частоти. Усередині індуктор прохолоджується проточною холодною водою, що охороняє його від перегріву й оплавлення. Електричний струм і воду підводять до індуктора по гнучких кабелях і шлангам, що дозволяють здійснювати поворот печі. З боку футеровки індуктор захищають, додатково використовуючи вогнетривку обмазку й ізоляційні аркуші міканіту й азбесту
Конденсатори монтують у батарею. Вони дозволяють значно скорочувати потребную потужність перетворювача й регулювати роботу печі на економічних режимах (регулювати cos .
На схемі (див. мал. 7.1) наведений обертовий перетворювач із горизонтальною віссю. В останні роки одержали поширення перетворювачі з вертикальною віссю, а також статичні (тиристорні) перетворювачі з високим КПД, відсутністю деталей, що зношуються, і т.п. У табл. 7.2 наведені технічні характеристики плавильних печей, що випускаються промисловістю індукційних, для плавки стали
Футеровка індукційних печей. Углеродистие стали виплавляють, як правило, у печах з кислої футеровкой. Вихідними матеріалами для кислої футеровки служить кварцит або кварцовий пісок і борна кислота
Більшу частину легованих, коррозионно-стійких, спеціальних сталей і сплавів виплавляють у печах з основний футеровкой. Нижче наведена, як приклад, футеровка печі основними матеріалами. Кисла футеровка виконується таким же способом. Вихідними матеріалами для основний футеровки служать хромомагнезитова цегла (бій), магнезитова цегла (бій), що заміняє їхній металургійний магнезит {порошок), вогнетривка глина, рідке скло, борна кислота
Магнезитова й хромомагнезитова цегла або бій цегли дроблять на щековой каменедробарці, подрібнюють у бігунах або в кульовому млині до величини зерен
< 4 мм, потім просівають через сито № 04. Отриманий матеріал зберігають у закритих ларях; у сухому приміщенні й у міру потреби використовують для готування футеровочной маси. Вогнетривку глину просушують при температурі 150—200 °С, подрібнюють у бігунах і просівають також через сито № 04. Мелену глину зберігають у закриті ларях.
Застосовують футеровочную масу наступного сполуки; до 95 % магнезиту або хромомагнезиту; 2-6 % вогнетривкої глини й 1,5-.
2 % борної кислоти або бури. Спочатку ретельно перемішують магнезит, потім додають борну кислоту, знову ретельно перемішують усю суміш у сухому виді й, додаючи води ( до вологості
3-4 %), знову ретельно перемішують усю масу. Мішалки можуть бути лопатевими або шнековими
Перед набиванням тигля обов`язково перевіряють справність механізму підйому печі, системи водяного охолодження, ізоляції й кріплення індуктора. Потім рчцщают і обдувають індуктор стислим
Таблиця 7.2.
Технічні характеристики індукційних плавильних печей для плавки стали
t> * | сх. ж | к. КS. о. з | сть. пері- | Витрата води на охолодження, м 8 /год | а. V | S. ПРО. * | ||||
Тип печі (місткість тигля по сталі, кг) | Тип перетворювача частоти | Вихідна мощн < преобр азовател я, | Частота струму кс иой депи, Гд | Номінальне нап ние живильної де | Продуктивно по переплавові й греву, т/.ч | індуктора | конденсаторної батареї | преобразовате. ля | Маса єлектропе | Число печей у плексе |
ИСТ-0,06 | ВПЧ — 100-2,4 | 100 | 2400 | 380 | 0,13 | 1,2 | 0,6 | 2,5 | i,6 | 2 |
(60) | ТПЧ — 100-2,4 | 100 | 2400 | 380 | 0,13 | 1,2 | 0,6 | 2,0 | i,6 | 2 |
ТПЧ — 100-2,4 | 100 | 2400 | 380 | 0,24 | 1,8 | 1,0 | 2,0 | 1,6 | 2 | |
ИСТ-0,16 | ТПЧ — 160-2,4 | 160 | 2400 | 380 | 0,265 | 1,8 | 2,8 | 4,0 | 2,0 | 2 |
(160) | ОПЧ — 250-2,4 | 250 | 2400 | 380,. 600,. 3000. або. 6000 | 0,41 | 2,5 | 3,8 | 4,0 | 2,0 | 1 |
ТПЧ — 320-1 | 320 | 1000 | 380 | 0,50 | 3,1 | 5,5 | 4,0 | 2,0 | 1 | |
ИСТ-0,25 (250) 4 | ; ОПЧ — 250-2,4 | 250 | 2400 | 380,. 600,. 3000. або. 6000 | 0,38 | 2,25 | 3,3 | 4,0 | 2,4 | 1 |
ТПЧ — 320-1 | 320 | 1000 | 380 | 0,47 | 2,5 | 4,8 | 5,5 | 2,4 | 1 | |
ОПЧ — 500-1 | 500 | 1000 | 3000. або. 6000 | 0,81 | 3,7 | 7,5 | 4,0 | 3,0 | 1 | |
ИСТ-0,4 | ТПЧ — 320-1 | 320 | 1000 | 380 | 0,44 | 2,9 | 6,3 | 4,0 | 3,0 | ) 1 |
(400) | ОПЧ — 500-1 | 500 | 1000 | 3000. або. 6000 | 0,78 | 4,0 | 8,2 | 5,5 | 3,0 | 1 |
Примітки. 1, ОПЧ — однофазний перетворювач частоти. ВПЧ — обертовий перетворювач частоти, ТПЧ — тиристорний (статичний) перетворювач частоти
2. Напруга контурного ланцюга в печах усіх типів 800 — 1000 В.
повітрям. Для ізоляції індуктора можна застосовувати спеціальну обмазку, що полягає з 80 % шамотного порошку, 20 % глиноземистого цементу й води ( понад 100 %) до кашоподібного стану. Шар обмазки продавлюють крізь витки індуктора й загладжують із внутрішньої сторони, потім сушать. По внутрішньому діаметру індуктор ізолюють двома шарами листового азбесту, який закріплюють пружинними рознімними кільцями. На подину печі укладають два-три шари листового азбесту загальною товщиною 6-10 мм .(мал, 7.2),
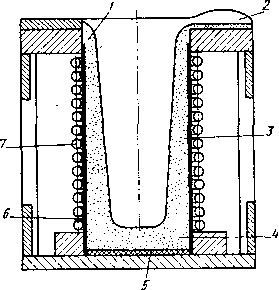
Рис. 7.2. Футеровка індукційної печн підвищеної частоти:.
1 — верхнє кільце (комір); 2 — носок; 3 — стінка тигля; 4 — подииа; 5 — азбест; 6 — азбестова ткаиь; 7 — індуктор
.
На аркушевий азбест, покладений на подину печі, засинають футеровочную масу (шар товщиною 100-130 мм) і ущільнюють її трамбуванням рівномірно й щільно настільки, щоб трамбування відскакувало. На цей шар установлюють металевий шаблон. Поверхня втрамбованого шару навколо підстави шаблону спушують і засинають футеровочную масу в кільцевий простір між індуктором і шаблоном шаром висотою 20-40 мм. Кожний шар щільно втрамбовують і потім для зв`язку з наступним шаром спушують поверхню. Стінки тигля набивають футеровочной масою до верхнього витка індуктора, попередньо виймаючи по черзі розтискні кільця. Після цього виймають шаблон або розплавляють його при першій плавці. Іноді стінки тигля змочують 50 %-ним розчином рідкого скла у воді. Верхнє кільце футеровки й носок тигля виконують із тієї ж футеровочной маси з добавкою 5-10 % рідкого скла
У тигель вставляють графітовий стрижень, близький по розміру тиглю, або металеві болванки, і включають пекти на потужність 10-40 кВт. Таким чином, протягом 1,5-2 год відбуваються сушіння й спікання тигля. По закінченню цього процесу пекти виключають, виймають графітовий стрижень (болванки), продувають тигель стисненим повітрям і перевіряють стан футеровки. При відсутності тріщин у футеровке пекти придатна до плавки. Якщо в процесі роботи печі на футеровке з`являться незначні тріщини або розмиви, то допускається підмазати їх футеровочной масою з рідким склом, застосовуваної для набивання верхнього кільця (коміра).
Перед завантаженням шихти пекти очищають від сторонніх предметів, перевіряють стан футеровки печі (на відсутність тріщин, розмивів і інших дефектів) і стан індуктора (справність ізоляції й водяного охолодження).
Футеровку тиглів вакуумних печей здійснюють набиванням сумішшю плавлених магнезиту й електрокорунду в співвідношенні 2:1.
Футеровочную суміш становлять із порошків трьох фракцій, у тому числі 10 % розміром зерна 4-2 мм, 20 % розміром зерна 2-.
1 мм, інші розміром зерна .
Суміш готовлять у лопатевих мішалках або в бігунах, що змішують. Спочатку змішують тонкозернисту фракцію (розмір зерна
.
Стійкість футеровки вакуумних печей з масою плавки 10- 20 кг, найбільше часто застосовуваних у виробництві виливків з жароміцних сплавів, досягає 500-600 плавок. Однак у процесі експлуатації спостерігаються дрібні розтріскування й руйнування футеровки, частки якої попадають у рідкий метал і приводять до шлюбу виливків по засорам. Для зниження шлюбу по засорам замість набивних тиглів доцільно застосовувати готові спеченние вогнетривкі тиглі із щодобової їх заміною
Плавка стали в індукційних печах. Плавка в індукційній печі йде швидко, тому немає можливості чекати повного експрес-аналізу й за отриманим даними коректувати хімічний склад розплаву. Плавку доводиться вести, ґрунтуючись на розрахунках шихти. Шлаки мають низьку температуру й недостатньо активні. Із цієї причини плавку ведуть без окиснення, методом переплаву, використовуючи чистий металевий скрап, чисте ливарне повернення й феросплави. Процеси дефосфорації, десульфурации й дифузійного розкислення в такому випадку утруднені, тому шихтові матеріали необхідно підбирати з малим змістом сірки й фосфору
Розміри шихтових матеріалів підбирають із умов найбільш повного заповнення тигля. Тугоплавкі феросплави зафужают у більш гарячу частину печі — у нижню частину тигля. Для"більш щільної укл,адки проміжки між великими шматками шкхти засинають дрібними. Щільне укладання шихти сприяє прискоренню її розплавлювання й зниженню витрати електроенергії. У ці ж цілях пекти накривають кришкою-зводом. Шихтові матеріали не слід завантажувати вище витків індуктора, тому що в цьому випадку, не перетинаючись силовими лініями магнітного поля, шихта плавиться тільки за рахунок теплопередачі; крім того, високо завантажена шихта перешкоджає щільному закриттю печі зводом
Шматки шихти в міру оплавлення й опускання вниз можуть зварюватися між собою, утворюючи «міст», під який розплав перегрівається, що може привести до руйнування футеровки.Заклинйв-Шиеся шматки шихти слід звільняти, піднімаючи їх кліщами нагору, осаджуючи в той же час звільнені шматки шихти вниз, у розплав. Не можна завантажувати холодну шихту, а тим більше вологу в розплавлений метал, тому що це супроводжується виплеском останнього з печі. Виплески, потрапляючи на шматки твердої шихти, також сприяють утвору «мостів».
У міру плавЛенйй й осідання Шихти в піч додають подогре тие шматки шихти, що не помістилися при завалці
Дотримуються наступного порядку введення в сплав легуючих елементів. Нікель у процесі плавки не окисниться, тому era уводять безпосередньо в шихту при завантаженні печі. Раняя завантаження* нікелю сприяє виділенню з металу водню, газів, содер- жащихся в електролітичному нікелі, і води — у гранульованому нікелі. Феромолібден також дають взавалку.
Вольфрам — тугоплавкий елемент із температурою плавлення. ~3400 °С. Для його розчинення в розплаві потрібне тривалий час, скоротити яке можна попереднім підігрівом вольфраму або феровольфраму до 900—950 °С. Вольфрам — важкий; метал. Для його розчинення необхідно перемішувати нижні шари ванни
Металевий хром уводять до складу шихти при виплавці сталей з особливими властивостями (жароміцні, жаростійкі) головним чином у випадках, коли потрібне низький зміст вуглецю. При виплавці інших легованих сталей звичайно використовують ферохром різних марок. Ферохром уводять у завалку або після розплавлювання основи сплаву. Після присадки ферохрому шлаки здобуває зелений колір завдяки окислам хрому. Раскислители відновлюють хром з окислів, і шлаки після розкислення здобуває світле фарбування
При виплавці високохромистих сталей ферохром попередньо підігрівають у нагрівальній печі, що скорочує тривалість плавки. Ферохром має меншу об`ємну масу, чому сталь, тому шматки його спливуть на поверхню металу. Їхнім періодично осаджують у глибину ванни
Ванадій легко окисниться, тому його вводять у ванну за 5- 10 хв до випуску стали в добре раскисленний метал
Титан окисниться ще більш інтенсивно, ніж ванадій. Його вводять у ванну перед випуском стали з печі ( за 2-3 хв). Тому що титан значно легше стали, те його для кращого засвоєння слід занурювати в розплав за допомогою спеціального «дзвіночка» або шомпола. Якщо феротитан попередньо підігріти й безупинно занурювати при розплавлюванні в сталеву ванну з малою кількістю Шлаків, то можна розчинити в сталі до 70 % титану, що вводиться. Якщо цих заходів не прийняти, засвоєння титану складе всього 50-40 %, а іноді й менш.
Після розплавлювання всієї шихти наводять шлаки. В індукційних печах завдяки опуклому меніску розплаву, що пронизується магнітними силовими лініями, шлаки стікає до стінок тигля; його час від часу додають, не допускаючи появи незахищеної Шлаками поверхні металу. Жужільний покрив в індукційних печах захищає сплав від насичення газами, знижує вигар елементів і зменшує теплові втрати. При виплавці стали в печах з кислої футеровкой найчастіше в якості жужільної суміші використовують бій скла
При основний футеровке шлаки складається з 60-80 % свежеобож-женной перевести, 15-20 % магнезитового порошку й 5-20 % плавикового шпату. Для високожаропрочних нікелевих сплавів застосовують також шлаки наступного сполуки: 50 % Сао, 25 % А1
0
; 18 % Mgo і 7 % Caf
Під час доведення стали в останній період плавки до складу шлаків додають мелений кокс або електродний бій, феросиліцій або комплексні раскислители-силикокальций, боркальк. Від сполуки шлаків залежить стійкість тигля. Високоосновной шлаки проникає в стінки футеровки й реагує зі сполучним, вимиваючи стінки тигля. Крім того, якщо шлаки має така сполука, що при охолодженні він розсипається на повітрі, ошлакованние стінки тигля при охолодженні печі також можуть обсипатися. Тому часто доведення сплаву ведуть зі шлаками меншої основности, наприклад: 50 % Sio„.
25 % Сао, 25 % А1
0
Загальна кількість шлаків при плавці в індукційних печах становить ~3 % маси металевої шихти. Плавку слід вести на максимальній потужності генератора й набудовувати електричний режим на резонанс (cos .
При виплавці стали в печах місткістю 150-250 кг після повного розплавлювання металу беруть пробу для експрес-аналізу на вуглець і марганець в основній печі й на вуглець і кремній у кислій печі. Чекаючи аналізу знімають шлаки, що утворювався при плавленні, і наводять новий шлаки того ж сполуки
При плавці в печах місткістю 10-50 кг експрес-аналіз звичайно не роблять внаслідок швидкого протікання процесу плавки. У цьому випадку сполука шихти не коректують, а ведуть плавку точно з розрахунку, строго витримуючи час і єлектрическщцєежим плавки. У печах малої ємності через труднощі наведення шлаків при дуже опуклому меніску розплаву покривним шлаками звичайно не користуються. Плавку ведуть без шлаків
Після одержання аналізу, якщо сплав треба науглеродить, знімають шлаки й на дзеркало розплаву засинають дрібно дроблений електродний бій або деревне вугілля, після чого наводять новий шлаки. У цьому випадку коефіцієнт засвоєння вуглецю становить 70-80 %. Науглероживание стали краще вести, застосовуючи углеродистий ферохром або чавун, а не деревне вугілля або електродний бій, тому що в останньому випадку час плавки збільшується
Марганець уводять у розплав, виходячи із середнього змісту його ( по заданому хімічному складу сплаву). При добре налагодженій технології плавки для економічної роботи легуючі елементи вводять у розплав з урахуванням засвоєння на нижній межі хімічного складу
У всіх випадках доведення стали по сполуці слід проводити в печі, а не в ковші, як це іноді намагаються робити
- Перед узяттям проби на хімічний аналіз слід ретельно перемішувати ванну на всю глибину,.
У якості раскислителей застосовують вуглець, кремній, марганець, титан (або їх феросплави), алюміній, карбід кальцію, а також комплексні раскислители: силикокальций, силикомарга-нец, алюмобарийкальций і ін. При дифузійному розкисленні раскислители вводять у шлаки в меленому виді або в порошку (алюміній).
Розкислення вуглецем іде по реакції
Побічною речовиною при розкисленні вуглецем є газ, а єго виходить, що метал не забруднюється неметалічними сполуками. Розкислення вуглецем зв`язане й з деякими недоліками: можливо науглероживание сплаву, дифузійний процес розкислення вуглецем тривалий
Розкислення кремнієм, марганцем і алюмінієм іде по реакціях
Кремній — сильний раскислитель, але з підвищенням температури його раскисляющая здатність знижується
Марганець значно слабкіше раскисляет сталь, чому кремній. Одним марганцем повністю раскислить сталь не можна. Закис марганцю нерозчинний у сталі й переходить у шлаки. Із сіркою марганець утворює більш тугоплавка сполука, чому залізо. Сірчистий марганець повністю переходить у шлаки й метал звільняється від сірчистих сполук
Для остаточного розкислення використовують силикокальций ( до 0,1 %), який змінює характер включень устали (строчечние включення він перетворює в глобулярні).
Розкислення металу для більших плавок (>100 кг) можна проводити дифузійним методом, уводячи в шлаки мелений кокс, феросиліцій або комплексні раскислители (силикокальций, бор-кальк). Шлаки при цьому швидко одержує светную фарбування. Розкисленню сприяє інтенсивний рух металу при індукційній плавці, але використовуючи гарну циркуляцію металу, можна раскислять сталь і кусковими раскислителями, що частіше роблять при роботі на печах малої ємності. Циркулюючі потоки металу виносять продукти розкислення на поверхню, де окисли переходять е шлаки
При дифузійному розкисленні застосовують різні шлаки залежно від хімічного складу стали й обладнання печі. Конструкційні углеродистие стали зі змістом менш 0,3 % З.
раскисляют під білим шлаками, среднеуглеродистие й високоуглеродистие під карбідним шлаками, коррозионно-стійкі — під магнезіально-глиноземистим шлаками
Перед наведенням білого шлаків скачивают окисний шлаки, у ванну присаживают феромарганець із розрахунку на верхню межу змісту в сплаві, потім наводять високоосновной шлаки, що полягає з 80 % вапна й 20 % плавикового шпату. Кількість шлаків залежить від місткості печей і становить 2-3 % маси завалки для печей великої місткості й 3-7 % — малої
Для розкислення в жужільну суміш уводять мелений кокс або деревне вугілля, що володіє меншою масою й менше науглероживающий сталь
Вуглець у шлаках раскисляет закис заліза й марганцю по реакціях
Перед розкисленням шлаки темного кольору ( присутні окисли заліза й марганцю), у процесі розкислення він світлішає. Для остаточного розкислення вводять дроблений 75 %-ний феросиліцій так, щоб його частки залишалися зваженими в шлаках і не переходили в метал. Кількість феросиліцію повинна бути дорівнює кількості вуглецю, що вводиться в шлаки. Після остаточного розкислення шлаки стає білим пінливим. Гарний шлаки при остиганні розсипається на повітрі впорошок.
Розкислення металу в печах малої місткості ( до 50 кг) ведуть твердим раскислителем (переважно силикокальцием з рас* чету 0,2-0,3 % маси шихти). У цьому випадку шлаки не наводять. У процесі розкислення тигель закривають залізним аркушем через великий пироєффекта.
Підвищення якості сталей і сплавів у процесі їх плавки й заливання. Більшу частину сталей длялитья по виплавлюваних моделях у металургійній промисловості виплавляють у печах із кварцової (кислої) футеровкой. Зміст сірки й фосфору в цих сталях більш високе, чому в сталях, виплавлених у печах з основний футеровкой. Ці сталі забруднені також неметалічними включеннями (сульфіди, фосфіди й ін.), що знижують їхні механічні властивості, особливо пластичність. Для забезпечення високої ударної в`язкості високоякісних виливків зміст сірки й фосфору в них повинне бути не більш 0,01 %. Тим часом в, що випускаються металургійною промисловістю сталях, використовуваних у якості шихтових материалор при литті по виплавлюваних моделях, зміст сірки й фосфору допускається до 0,025 і навіть 0,05 %. Для придушення впливу шкідливих домішок, при плавці слід застосовувати модифікатори, які видозмінюють особливо несприятливу гострокутну форму фосфідів, оксидів і сульфідів, очищають границі зерен і упрочняют сталь

Рис. 7.3. Схема плазменно-індукційної плавильної установки:.
I — механізм переміщення плазмотрона; 2 — плазмотрон; 3 — поду« ча аргону; 4 — герметизированний люк; 5 — кришка (звід); 6 — індуктор печі; 7 — водоохлаждаемий анод; 8 — джерело харчування
.
Гарним модифікатором є силикокальций у комбінації із РМЗ, при введенні яких в 2 рази підвищується ударна в`язкість стали [111, 1121.
Значне підвищення якості сталей і сплавів досягають також застосуванням плазменно-індукційної плавки при якій завдяки додатковому нагріванню верхньої частини ванни скорочується час плавкий. Одночасно підвищується чистота металу, продуктивність печей і знижується питома витрата електроенергії [91.
В ИПЛ АН УРСР розроблена й випробувана на ряді заводів плазменно-індукційна установка [9], виготовлена на базі печі ИСТ-0,16, до якої зроблена плазмова приставка, що представляє собою водоохлаждаемую футерованную кришку (звід), установлену у верхній частині печі на ущільнювальному кільці (мал. 7.3). На кришці змонтований плазматрон з механізмом його переміщення. Для завантаження шихти в процесі плавки, уведення легуючих добавок і спостереження за ходом плавки в кришці передбачений герметизированний люк зі склом. У дно тигля вмонтований водоохлаждаемий анод. До плазматрону підведені системи охолодження й газоочищення. Харчування плазматрона здійснюється від керованого джерела постійного струму типу ВПР-602. У якості плазмообразующего газу використовують технічно чистий аргон ( ДЕРЖСТАНДАРТ 10157—79), попередньо очищений від вологи, кисню й азоту
Відомо, що властивості виливків у великому ступені залежать від орієнтації й величини зерей у литому структурі. Якість виливків можна підвищити, здійснюючи регулювання структури металу в процесі заливання форми і її охолодження, так звану, контрольовану кристалізацію [90, 18]. Для цих цілей у плавильнозаливочних вакуумних установках, додатково до плавильних печей поміщають індукційні нагрівальні печі для форм. Прожарені форми встановлюють у піч нагрівання форми й, у процесі плавки металу й заливання його форма не остигає, а нагрівається до заданої температури й навіть до температури розплаву, що заливається. Контрольовану (спрямовану) кристалізацію виливків можна вести по декільком варіантам технологічного процесу, розглянутим нижче.
1.
Застосовують тонкостінну міцну оболонку форму без опорного наповнювача, яку нагрівають до 1000—1050 °С, заливають розплавом при температурі 1480—1500 °С и витримують у нагрівальній печі до 800—850 °С. При досягненні цієї температури виливок переносять у термостат з температурою 600—650 °С, де витримують до 300 °С с наступним охолодженням на повітрі. При такому режимі одержують полікристалічну структуру виливка з мінімальними залишковими напругами, але з порівняно великою макроструктурою
2.
При виготовленні оболонкової форми в поверхневий шар форми вносять мелкодисперсние окисли, що є модифікаторами — центрами кристалізації, і потім цю форму нагрівають, заливають розплавом і прохолоджують по варіанту 1. У цьому випадку одержують більш дрібну макроструктуру в поверхневому шарі виливка. Її можна регулювати кількістю; модифікатора і його дисперсністю
3.
Оболонкову форму нагрівають до температури заливання розплаву. Після заливання нижню частину форми (виливка) штучно охлаждаюр-і поступово із заданою швидкістю форму з виливком виводять униз із зони нагрівальної печі. Відбувається спрямована знизу нагору кристалізація виливка, який здобуває полікристалічну або монокристалічну структуру, орієнтовану вертикально по всій висоті. При цьому різко зростають пластичні властивості металу, надійність і тривалість експлуатації виливків
У табл. 7.3 наведені властивості сплаву ММ 200, відлитого по різних варіантах технології
Таблиця 7.3.
Властивості різних модифікацій сплаву ММ 200 _ _.
Сплав | ММ 200 | |||
Властивості | звичайний | ММ 246 (модифікація) | спрямованої кристал-лиаацин | у виду монокристала |
при г і = 760 °з. сг в . МПа | 949 | 1055 | 1055 | 1055 |
6, % | 3 | 4 | 6 | 12 |
Жароміцність т, год ( при 700 МПа) | . 5 | 30 | . 380 | 250 |
Повзучість проо/юо ( П Р И 00 МПа) | — | 30 | 3 | 5 ■ |
При t B = 982 °С Жароміцність х, год ( при 210 МПа) | 40 | 36 | 105 | 105 |
Повзучість проо/юо ( П Р И 210 Мпа) | 30 | 10 | 45 | 45 : |
Термічна утома | Гарна | Дуже | Отлич | |
Вартість | Звичайна | гарна Висока | їм Дуже | |
висока |
Рис. 7.4. Макроструктура виливків з регульованою кристалізацією;.
.
/ — поликристаллнческая структура; II — спрямована ( про-дольио-ориеитнрованная) структура; III — монокрнсталлическая структура
По пластичності й термічної утоми сплави зі спрямованою кристалізацією в порівнянні з полікристалічними сплавами мають дуже більші переваги, що пояснюється відсутністю поперечних границь зерен. Але повільна кристалізація сприяє утвору рихлот у виливках. Немає переваг у повзучості. Одержання виливків з контрольованою кристалізацією трудомістко й складно, тому виливка поки дуже дороги
4. Оболонкову форму встановлюють у графітову опоку з д ом і засинають графітовою крихтою. Опоку поміщають у піч і нагрівають до температури заливання металу. Після заливання форму витримують у печі до повного заповнення розплавом междендритних порожнеч. Потім форму із заданою швидкістю опускають із нагрівальної печі й вона остигає на повітрі, або в термостаті по заданому режиму. У результаті одержують тонкостінний щільний фасонний виливок з односпрямованим затвердінням металу у всіх стінках. При цьому спостерігається деяке підвищення міцності й різке підвищення пластичності
На мал. 7.4 наведена макроструктура виливків з регульованою кристалізацією
Плавка спеціальних сплавів в иидукциоииих вакуумних печах. Найбільш високими жароміцними властивостями, необхідними для виробництва литих турбінних лопаток, мають литі сплави на нікелевій основі типу ЖС. Основним методом одержання лопаток із цих сплавів є лиття по виплавлюваних моделях. Однак зазначені сплави через великий зміст алюмінію й титану легко окисняться й утворюють у процесі плавки й розливання щільні окісні плівки, які, потрапляючи у виливки, порушують сплошность
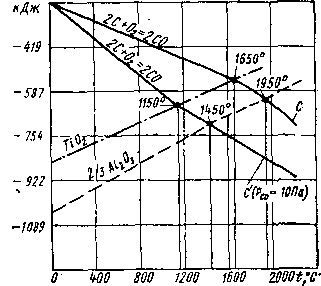
Рис. 7.5. Вільні енергії утвору окислів металів для реакцій, виражених на 1 г• моль кисню
.
матеріалу й знижують міцність лопаток. Величина окісних плівок і їх розташування у виливках найрізноманітніші. Наявність окісних плівок на поверхні пера лопаток, а також на їхніх крайках, як правило, є ознакою шлюбу
Окісні плівки утворюються при температурі до 1700 °С як під час готування вихідного сплаву иразливки його в изложници, так і під час готування робочого сплаву й розливання його у форми при виливку лопаток. Уникнути утвору окісних плівок можна обробкою рідкого розплаву раскислителями, плавкою й розливанням у вакуумі або в нейтральному середовищі
Плавка жароміцних ливарних сплавів, що містять алюміній і титан, у вакуумних індукційних печах підвищеної частоти знаходить усе більше застосування. По своїй спорідненості до кисню алюміній уступає лише магнію й кальцію. Вакуум сприяє будь-якої хімічної реакції, у ході якої з нелетучих речовин утворюються гази або летучі речовини, у результаті чого знижується температура й стає можливим протікання даної реакції
На мал. 7.5 наведені зміни вільних енергій утвору окислів титану й алюмінію залежно від температури
В атмосферних умовах вуглець може почати розкислення окислів титану при температурі 1650 °С, а окислів алюмінію при 1950 °С. Зі зниженням тиску раскислительная здатність вуглецю підвищується й при розрідженні 10 Па температура початку розкислення знижується приблизно на 500 °С, тобто окисли титану раскисляются вуглецем при температурі 1150 °С, а окисли алюмінію при 1450 °С. Досвід плавки жароміцних сплавів у вакуумних печах при розрідженні 1—4 Па підтверджує раскисляемость окислів алюмінію (плівки) при температурі 1550—1650 °С по реакції
при цьому окис вуглецю улетучивается. Технічні характеристики вакуумних індукційних печей наведені в табл. 7.4.
При використанні печей періодичної дії (див. табл. 7.4) після кожної плавки й заливання вакуумна камера повідомляється з атмосферою й відкочується. Залиту форму знімають із печі, очищають тигель, знову завантажують шихту, установлюють нову форму, камеру накочують і починають вакуумирование тигля, шихти й форми
Технічні характеристики індукційних вакуумних печей для плавки н заливання форм
Тип | печі | |
Параметр | ИСВ-0,04 ПФ-І2 * | ИСВ-0,16 НФ-І1 * |
Номінальна ємність тигля (по сталі), т | 0,04 | 0,16 |
Установлена потужність, кв-а | 250 | 525 |
Потужність живильного перетворювача, кВт Частота, Гц: | 120 | 250 |
контуру | 2400 | 2400 |
живильної мережі Напруга, В: | 50 | 50 |
контуру | 500 | 300 |
живильної мережі | 380 | 380 |
ланцюгів керування | 220 | 220 |
силових ланцюгів | 220/380 | 220/380 |
Максимальна температура розплаву в тнгле, °Із Середовище в робочому просторі (плавильна камера) | 1650 | 1700 |
Вакуум або нейтральний газ | ||
Граничне розрідження в холодній печі, Па | 5-0,133 | 5-0,133 |
Максимально припустимий надлишковий тиск нейтрального газу, кПа. Продуктивність по розплавлюванню й перегріву, т/ч | 10 | 10 |
0,12 | 0,21 | |
Питома витрата електроенергії на розплавлювання й перегрів, квт-ч/т Габаритні розміри форм, м: | 1100 | 2000 |
ширина X довжина | 0,5X0,6 | 0,7X1,6 |
висота | 1,0 | 1,0 |
Маса електропечі, т | 10 | 30 |
Місткість (по сталі) змінних індукторів, якими додатково комплектуються печі, т | 0,01 і 0,025 | 0,06 і 0,1 |
* П — періодичного дії; Н — безперервної дії
.
Таким чином, вакуумна система працює нераціонально на відновлення загубленого вакууму. Крім того, відбувається втрата теплоти й різка зміна температури тигля, що знижує стійкість футеровки, а також окиснення залишків розплаву на стінках тигля. Утворюються так звані настили, що забруднює рідкий метал наступних плавок і знижує якість виливків
Для усунення відзначених недоліків випускають вакуумні установки напівперериваної дії на різну місткість тиглів (див. табл. 7.4). У цих установках крім індукційної печі для плавки металу є пекти опору для підігріву форми до 900 °З.
Особливості плавки сплавів для постійних магнітів. Зміст домішок, особливо вуглецю, у шихтових матеріалах повинне бути мінімальним. У магнітних сплавах повинне бути не більш0,03 % З;Ч),35 % Мп, 0,15 % Si, 0,025 % S і 0,025 % Р. У сплаві ЮНДК18 зміст 0,1 % Зі знижує залишкову індукцію на.
20 %, коерцитивну силу на 40 % і максимальну магнітну енергію на 50 %.
•.
Для одержання високоякісних магнітів необхідно застосовувати наступні шихтові матеріали: низьковуглецеву електротехнічну сталь (залізо армко) марок ЄА й Є у вигляді прутків або аркушів; нікель марок Н-0 і Н-1 у вигляді катодних аркушів або злитків за ДСТ 849-70; кобальт марок ДО й К.1А в чушках шг ДЕРЖСТАНДАРТ 123-78; алюміній первинний марок А95, А7, А6, А5 у чушках за ДСТ 11069-74; мідь марок МО й Ml у вигляді катодних аркушів за ДСТ 546-79; повернення й відходи магнітного сплаву (літники, шлюб магнітів по зовнішніх дефектах і ін.).
Кількість відходів, що вводяться в плавку, повинне бути не більш 40 % маси шихти
Вихідні шихтові матеріали підлягають обробленню тільки в холодному стані. Газове різання шихтових матеріалів не допускається. Повернення й відходи, що надходять на плавку, повинні бути очищені від формувальних матеріалів, а також від окислів, масляних, плям і інших забруднень. Крім основних шихтових матеріалів у сплав часто додають сірчисте залізо з метою здрібнювання структури й зміцнення сплаву. При плавці сплаву ЮНДК18 сірчистого заліза звичайно додають 0,3 % маси шихти
Магнітні сплави виплавляють у високочастотних індукційних печах з кислої або основний футеровкой. Для одержання магнітів зі стабільними властивостями плавку слід вести форсовано; швидкість розплавлювання всієї шихти даної плавки 0,7—1,2 кг/хв. Щоб скоротити тривалість плавки, шихтові матеріали підбирають оптимальних розмірів залежно від ємності плавильного тигля (табл. 7.5).
.
Таблиця 7.5.
Розміри шихтових матеріалів залежно від місткості тигля
Місткість плавильного тигля, кг | Розміри прутків заліза, мм | Маса чушок кобальту,. кг | Розмір заготовки, мм | Маса чушкн. алюмінію,. кг | ||
діаметр | довжина | иикеля | міді | |||
10—20. 20—30. 30—50 | 15—20. 20—35. 20—50 | 110—130. 150—200. 200—230 | 0,9-1,5. 1.5-2,5. 2.5-4,0 | ЗОХ100 60Х160 80X 250 | ЗОХ 100 60X150 80X250 | 0,8-1,1 1,1-2,4 2,5-4,0 |
Рекомендується також підігрівати до температури 300—400 °С нікель, мідь і алюміній перед завантаженням у плавильний тигель. Завантаження й плавку шихтових матеріалів необхідно вести в певній послідовності: при плавці в кислому тиглі завантажують бите скло (2 % маси шихти), потім залізо, кобальт. Включають струм і ведуть плавку на максимально можливій потужності печі. Після расшгавления більшої частини заліза й кобальту в тигель завантажують нікель, мідь і сірчисте залізо, а потім повернення (літники й інші відходи). Під час розплавлювання шихти ванна повинна бути увесь час покритий шлаками, . ...
Основні характеристики поворотних тигельних печей опору CAT
Тип печі | Місткість тигля, кг | Потужність трансформатора, кВт | Маса металевої конструкція печн, кг | Габаритні розміри (длниа, ширина, висота), м |
САТ-0Д5А | 150 | 40 | 960 | 1,75X1,34X2,30 |
САТ-0.25А | 250 | 60 | 1170 | 1,87X1,44X 2,38 |
САТ-0,50А | 500 | 80 | 1570 | 2,0X1,59X2,62 |
Після розплавлювання всієї завантаженої шихти й деякого перегріву розплаву знімають шлаки й швидко завантажують великі шматки алюмінію. Потім ванну ретельно перемішують (штангою з електротехнічної сталі) і, витримавши 2—3 хв, знімають готовий розплав, що знову утворювався шлаки й, зливають у ківш, попередньо підігрітий °до 700-850 С. Перед випуском розплаву температура його повинна бути 1550—1600 °С. Температуру вимірюють
термопарою занурення. Сильний перегрів розплаву приводить до одержання тендітних магнітів, що фарбують при шліфуванні. Плавка алюмінієвих сплавів. У виробництві лиття по виплавлюваних моделях з алюмінієвих сплавів звичайно застосовують плавильні печі місткістю 0,15- 0,50 т, до них ставляться й електропечі опору типу CAT (тигельні) (табл. 7.6, мал. 7.6). Для плавки алюмінієвих сплавів застосовують також більш економічні індукційні печі промислової частоти із залізним сердечником, які працюють за принципом своєрідного короткозамкненого трансформатора: первинна обмотка — мно-говитковая котушка (індуктор), а вторинна — розплавлений метал у каналах. Роботу на цих печах слід вести безупинно. У перервах між плавками в печі повинен обов`язково залишатися розплав («болото») у такій кількості, щоб плавильні канали замикалися. У цей час пекти працює на потужності холостого ходу, яка в 5-6 раз менше номінальної потужності
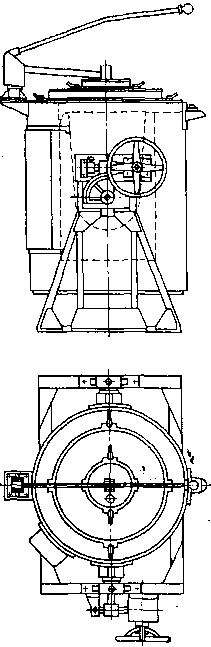
Рис. 7.6. Поворотна тигельна піч типу CAT.
.
.
.
Для алюмінієвих Сплавой Мінімальної, по корисній місткості є індукційна канальна піч ИА-0,5 (мал. 7.7).
Печі ИА-05, постачені гідравлічним механізмом із плунжерами для повороту. Розплав зливають при нахилі печі через злив* ний носок
Індукційні електропечі ИА-0,5 застосовують для безперервної роботи. Пусковий період включаючи час на футеровку печі триває
1 —1,5 мес, тому в експлуатації повинне бути не менш двох печей. Стійкість футеровки канальної частини печей ИА-0,5 виконаної із шамотно- кварцитової маси, 2000-3000 плавок. У процесі роботи канали печі заростають окисом алюмінію, їх доводиться система-тичзски прочищати 1- 2 рази в зміну спеціальним інструментом (труби, йоржі й г. буд.). Повна місткість каналів 0,3 т і робочої ванни 0,5 т. Номінальна потужність печі 125 кВт, потужність трансформатора 180 кВт. Питома витрата електроенергії 450- 445 квт-ч/т. Тривалість плавки 2 ч. Потужність холостого ходу 22 кВа. Видача розплаву може проводитися в заданому темпі до 250 кг/ч.
Доцільно застосовувати індукційні тигельні печі (ИПА-250 і Й ПА-500) промислової частоти місткістю 250 і 500 кг, які добре себе зарекомендували в експлуатації (табл. 7.7).
Таблиця 7.7.
Технічні характеристики індукційних тигельних печей ИПА-250 н І ПА-500 для плавки алюмінієвих сплавів і печі ИПМ-350 для плавки магнієвих сплавів
Параметр | ИПА-250 | ИПА-500 | ИПМ-350 |
Середня потужність печн, кВт | 70 | 120 | 100 |
Потужність конденсаторних батарей, кв-а | 190 | 320 | 420 |
Середня снла струму сетн, А | 270 | 400 | 260 |
Ємність тнгля, кг | 250 | 500 | 350 |
Час плавки в гарячому тиглі, мнн Продуктивність печн, кг/год | 110 | 110 | 100 |
136 | 273 | 210 | |
КПД, % | 70 | 75 | 83 |
Питома витрата електроенергії, квт-ч/т Габаритні розміри печн (довжина, ши | 450 | 400 | 450 |
1,5X2,0Х | 1,5X2,0Х | 1,25Х 1,25Х | |
рина, висота), м | Х1,6 | Х2,0 | XI,5 |
Примітка. Частота живильного струму 50 Гц; напруга на індукторі печя живильної мережі й конденсаторної батареї 380 В.
На мал. 7.8 показана тигельна індукційна пекти промислової частоти. Пекти складається з товстостінного тигля із кришкою, індуктора, теплоізоляції й магнітопроводу. Тигель установлений у каркас печі, який повертається гідравлічним підйомником. Нагрівання й плавка шихти відбуваються за рахунок теплоти, индуктированной у матеріалі шихти, і тепловипромінювання тигля, що нагрівається індуктивними струмами. Завдяки цьому, питома витрата єлектро-
РИС. 7.7. Піч ИА-0,5:.
а — загальний вид; б — футеровка.
Рис. 7.8. Індукційна тигельна електропіч промислової частоти для плавки легких сплавів:.
1 — тигель; 2 — теплова ізоляція; 3 — індуктор; 4 — гідравлічний підйомник; 5 — вузол приєднання печі; 6 — щит керування; 7 — приміщення для конденсаторів
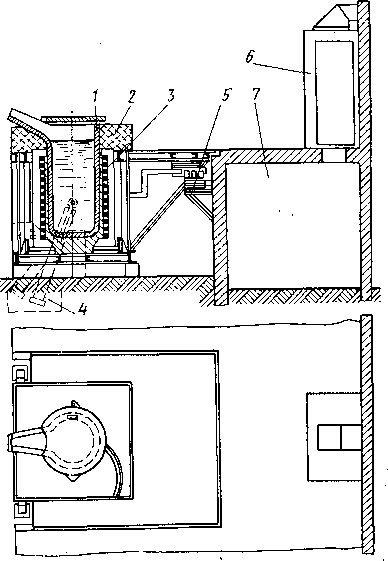
енергії значно со-кращается. КПД таких печей дуже високий і досягає 0,85.
При плавці алюмінієвих сплавів застосовують чавунні тиглі. У печах типу ИПА можна також плавити мідні сплави, але в графітові тиглях
Використання чавунних тиглів при плавці приводить до насичення алюмінієвих сплавів залізом внаслідок розчинення стінок тигля. Щоб уникнути цього чавунні тиглі в підігрівом до 150 °С стані покривають захисними фарбами, які знижують ступінь насичення залізом алюмінієвих сплавів. Щоб повністю виключити насичення алюмінієвих сплавів залізом і знизити експлуатаційні витрати, пов`язані із заміною чавунних тиглів, на ряді промислових підприємств для індукційних печей типу ИПА впроваджені тиглі з жаростійкого бетону
Бетон складається із шамотно- магнезитової крихти, скріпленої рідким склом і кремнефтористим натрієм. Твердіння цього біс-цементного бетону відбувається в результаті фізико-хімічних процесів, що протікають при взаємодії складових суміші. При цьому утворюються форстерит і кордиерит компоненти, що зв`язують усе, в однорідну міцну масу
Готування алюмінієвих сплавів полягає в сплавці алюмінію з іншими металами. У розігріту піч завантажують шихтові матеріали з розрахунку, у наступному порядку: повернення сплаву (літники, браковані деталі й сплески), вихідні метали (алюміній, силумін, магній) і лігатури (проміжний сплав). елементи, що сильно чадіють (магній, цинк) уводять у сплав в останню чергу. Такий порядок завантаження дозволяє вести плавку форсовано, не перегріваючи сплав; тим самим знижується вигар компонентів і підвищується якість сплаву
Алюмінієві сплави легко окиснять. У процесі плавки на поверхні розплаву утворюється міцна окісна плівка, що захищає сплав від подальшого окиснення. Під час плавки перемішувати розплав не випливає, щоб не руйнувати окісної плівки. Добавки вводять обережно, зрушивши плівку із частини поверхні металу. Алюмінієві сплави інтенсивно поглинають і розчиняють гази, особливо водень, що приводить до газової пористості у виливках. Тому всі шихтові матеріали зберігають у сухому приміщенні й уводять у піч у сухому виді й навіть злегка підігрітими. Індукційні печі із залізним сердечником футеруют сумішами, у які входять мелена порцеляна або шамот (50—55 %), глина вогнетривка (30—40 %) і барит у порошку або плавиковий штап (9—12 %).
Для зменшення заростання окисом алюмінію канали виконують із графітових електродів або шляхом обклеювання шаблону при футеровке спеціальними графітовими пластинами. Для попередження утвору пористості й виключення неметалічних включень алюмінієві сплави піддають дегазації й рафінуванню в рідкому стані. Для цих цілей застосовують продувку розплаву хлором, обробляють гексахлорєтаном або хлористими солями (хлористий цинк, хлористий марганець і хлористий алюміній). Попередньо солі збезводнюють переплавленням і до використання зберігають в електрошафі при температурі 120—150 °З.
Для підвищення механічних властивостей, особливо пластичності, алюмінієві сплави, що містять *>5 % Si із грубою структурою піддають модифікуванню (штучне здрібнювання структури).
При литті по виплавлюваних моделях, коли процес кристалізації вповільнений через підвищену температуру форми (100—300 °С), виходять виливки із крупнокристаллической структурою й відносно низькими механічними властивостями. У таких випадках рекомендується модифікування розплаву введенням у нього невеликої кількості натрію. Для цього використовують хлористі й фтористі солі натрію. Спочатку розплав рафінують, а потім модифікують. Досвід показав, що під час модифікування подвійним (34 % Nacl + 66 % Naf) або потрійним (62,5 % Nacl + 25 % Naf -f-+ 12,5 % КСЛ) модифікатором розплав знову насичується газами й неметалічними включеннями. Щоб уникнути цього, а також для прискорення й здешевлення процесу плавки застосовують так званий універсальний флюс, який одночасно рафінує й модифікує розплав. Універсальний флюс розчиняє, переводить у прозорий розплав 1,2—1,6 % ( по масі) А1
0
, адсорбирует б-б—12 % А1
0
і дегазує розплав активніше хлористого цинку. Тому що заливання різних виливків роблять при різних температурах, застосовують три сполуки універсального флюсу, наведені в табл. 7.8.
Рафінують і модифікують розплави універсальним порошковим флюсом у такий спосіб. Солі, що входять до складу флюсу, попередньо сушать при 200—250 "С протягом 3 ч. Висушені солі змішують у бігунах або в кульовому млині до одержання
}. Номер флюсу | Зміст, % | Температура, °З | ||||
фтори. стий. натрій | хлористий натрій | хлористий калій | кріоліт | плавле. ния | мінімальна модифициро. вания | |
1 | 60 | 25 | 15 | 850 | 750 | |
2 | 40 | 45 | — | 15 | 780 | 730 |
3 | 30 | 50 | 10 | 10 | 730 | 710 |
однорідної суміші. Готовий флюс, попередньо нагрітий до 250— 300 °С, уводять у кількості 0,75—1,0 % на струмінь розплаву, що подавати в разливочний ківш ( при заповненні його). Після закінчення 2—4 хв після заповнення ковша розплав ретельно очищають і потім заливають у форми. Ще більш ефективна дія універсального флюсу в рідкому стані. Для розплавлювання флюсу застосовують трифазну дугову піч із центральним нагріванням солей (мал. 7.9).
Рафінують і модифікують розплав рідким універсальним флюсом у такий спосіб. У нагрітий разливочний тигель на невеликий шар розплаву мірною ложкою заливають рідкий флюс у кількості 0,3—0,5 % маси розплаву й заповнюють тигель розплавом. При цьому флюс спливе. Проходячи через увесь розплав флюс взаємодіє з ним, дегазуючи, рафінуючи й модифікуючи розплав. З моменту заповнення тигля розплав витримують втечение.
3 хв, після чого флюс знімають із дзеркала розплаву й останній розливають вформи.
Плавка магнієвих сплавів. Магній і його сплави при нагріванні на повітрі окисняться й загоряються, оскільки окісна плівка магнію пухка й не захищає його від подальшого окиснення. Тому плавку магнієвих сплавів треба вести під захистом флюсів або з добавкою 0,01—0,02 % Be. У цехах лиття по виплавлюваних моделях для плавки магнієвих сплавів рекомендується застосовувати індукційні тигельні печі промислової частоти ИПМ (мал. 7.10) із вставним сталевим тиглем (див. табл. 7.7). Магнієві сплави готовлять у два приймання: спочатку попередній сплав, у потім робітник сплав
У розпеченому тиглі розплавляють флюс ВИ-2 у кількості 1—2 % маси шихти, потім у нього завантажують чушковий магній, алюміній, лігатуру й розплавляють шихту. Розплав нагрівають до 680—700 °С и вводять у нього легуючі низкоплавкие елементи ( залежно від сполуки сплаву). Потім розплав доводять до температури 700—720 °С и рафінують його флюсами з перемішуванням протягом 5—6 хв. З поверхні розплаву знімають шлаки й забруднений флюс, наносять свіжий флюс, підвищують температуру розплаву до 750—780 °С и витримують при цій температурі 12— 15 хв, щоб розплав відстоявся. Після цього беруть проби на аналіз

Рис. 7.10. Схема індукційної тигельної печі промислової частоти для плавки магнієвих сплавів:
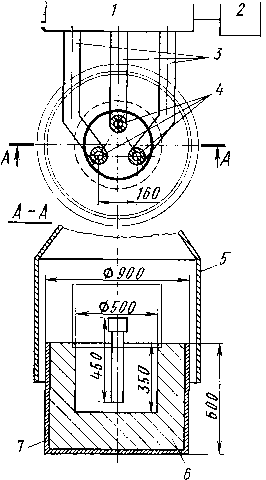
Рис. 7.9. Схема дугової електропечі для плавки універсального флюсу:.
1 — трехфазиий трансформатор 380/24;.
2 — щит керування; 3 —* шини: 4 —* графітові електроди; 5 — витяжний зоит; 6 — футеровка із шамотиого цегли; 7 — каркас печі
1 — сталевий тигель; 2 —• індуктор
хімічного складу, прохолоджують розплав до 700—680 °С и розливають в изложници. Тигель очищають від залишків флюсу, шлаків і інших забруднень і підготовляють до наступної плавки
Робітник сплав у тигельній печі готовлять так само, як попередній сплав, тільки в шихту для робочого сплаву крім чушкових свіжих металів і лігатур завантажують відходи даного сплаву. Після нагрівання розплав модифікують вуглецевмісними матеріалами (крейда, мармур, магнезія) і рафінують флюсом ВИ-2, потім прохолоджують до температури заливання й розливають у форми. При цьому зливають не весь розплав, 10-15 % залишається в тиглі і його зливають в изложници. Тигель очищають і готовлять до наступної плавки
Плавка титанових сплавів. Внаслідок великої спорідненості титану до кисню й утвору нітридів титану при нагріванні його в повітряному середовищі плавка титану і його сплавів можлива тільки у вакуумі або в середовищі нейтральних газів
Для лиття по виплавлюваних моделях найбільше поширення знаходять дугові гарииссажние електропечі з електродом, що витрачається (мал. 7.11). Графітовий тигель 2, у якому відбувається плавка, прохолоджується водою, що протікає в мідній обоймі 5. Температуру внутрішньої поверхні тигля регулюють із таким розрахунками,
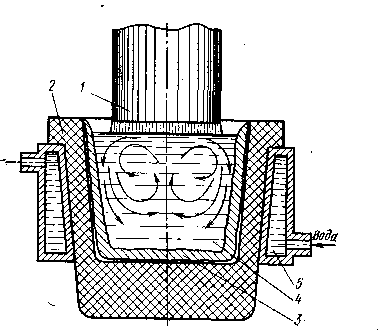
Рис. 7*11. Схема плавні в дуговий гарнис-саж ой електропечі з електродом, що витрачається,
.
щоб на стінках тигля протягом усього процесу плавки залишався нерозплавленим шар титанового сплаву товщиною 10-15 мм, так званий гарниссаж 3. Гарниссаж перешкоджає безпосередньому контакту тигля з ванною розплаву 4,отриманої від розплавлювання електрода, що витрачається, /, і, таким чином, охороняє сплав від насичення вуглецем
У табл. 7.9 наведені технічні характеристики електропечей для плавки титанових сплавів. Одна з печей (ОКБ-956) з поворотним тиглем для заливання розплаву у форму представлена на мал. 7.12.
Для заливання тонкостінних виливків у плавильно-заливальних камерах установлюють відцентрові установки
.
Таблиця 7.9.
Технічна характеристика дугових вакуумних гарниссажних електропечей
Параметр | ОКБ-956 | ОКБ-Ю72 | ОКБ-1007 |
Ємність плавильної ванни, кг | 25; 60 | 100 | 250 |
Постійний струм, А | 14 000 | 14 000 | 25 000 |
Напруга, В | 28-32 | 34 | 38-40 |
Залишковий тиск, Па | 0,13 | 0,13 | 0,65 |
Максимальні розміри електрода, мм: | |||
довжина | 500 | 650 | 485 |
діаметр | 200 | 300 | 460 |
Число встановлюваних електродів | 1 | 1 | 4 |
Максимальні розміри форми, мм: | |||
довжина (діаметр) | 800 | 600 | 800 |
ширина | - | 600 | 800 |
висота | 500 | 600 | 1200 |
Число встановлених форм | 1 | 1 | 4 |
Швидкість плавки, кг/хв | 5-8 | 3-6 | 10-15 |
Питома витрата електроенергії, | 7,4 | 2,3 | 2,5 |
квт-ч/кг | |||
Тривалість циклу, год | 2; 2,5 | 0,2 | 6,5 |
Витрата охолодної води, м 8 /год | 25 | 40 | 45 |
Габаритні розміри печі, мм: | |||
довжина | 7400 | 12 000 | 11 350 |
ширина | 2 800 | 7 560 | 6 750 |
висота | 5 275 | 6 800 | 5175 |
Маса печі, т | 176 | 50 | 42 |
Рис. 7,12* Дугова гарииссажиая електропіч ОКБ-960.
.
Плавка в електродугових гарниссажних печах з електродом, що витрачається, має й недоліки-утруднений перегрів розплаву й переплав відходів, неможливо витримувати розплав у печі й ін, У зв`язку із цим ведуться роботи із застосування інших джерел теплоти для вакуумних гарниссажних печей. Для цих цілей исполь-
Рис. 7.13. Електронно-променева четирехпушечная гарннссажиая установка
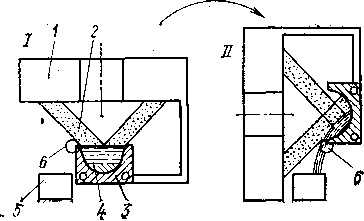
Рис. 7.14. Схема гарннссажной електропечі з поворотною радіальною гарматою;.
/ — положення при плавці; II — положення при заливанні; 1 — єлектроиио-лу-чевая пушка; 2 — електронний промінь; 3 — мідний тигель; 4 — розплав; 5 — форма; 6 — вісь повороту
.
зуют аксіальні й радиаль-ние електронні пушки. На їхній базі створені гарниссажние установки для плавки титану й інших тугоплавких ме таллов.
На мал. 7.13 показана електронно-променева гарниссажная промислова установка для лиття тугоплавких металів, у якій перебувають чотири аксіальні пушки потужністю 120 кВт кожна. Ємність тигля для плавки титану 6 л. Пекти постачена системою дистанційного спостереження й керування процесом
На відміну від дугової плавки з, що витрачається електродом електронно-променеве нагрівання дозволяє розплавляти грудковий шихтовий матеріал, у тому числі й відходи застосовуваних сплавів, легувати сплав уведенням легуючих компонентів у тверду шихту або в розплав у хбде плавки. При цьому представляється можливим витримувати розплав протягом будь-якого часу й перегрівати його до необхідної температури. Крім того, електронне нагрівання дозволяє створювати глибокий вакуум безпосередньо над дзеркалом ванни розплаву для максимального очищення його від шкідливих домішок
На мал. 7.14 показана схема гарниссажной електропечі з поворотною радіальною гарматою, що дозволяє ефективно обігрівати ванну в процесі повороту тигля для зливу розплаву вформу.
Поряд з подальшими роботами із впровадження єлектр онно-лу-чевой плавки ведуться роботи із плазмового нагрівання. Для одержання плазми використовують електричний розряд у середовищі газу. Звичайно плазму одержують за допомогою дугового розряду в плазмовому пальнику. Проходячи в плазмовому пальнику через дуговий розряд, газ іонізується й виходить із сопла з температурою в кілька тисяч градусів. Отриману в такий спосіб плазму застосовують для гарниссажной плавки титану й інших тугоплавких металів