Модельні сполуки можуть бути класифіковані по ряду ознак, наприклад, залежно від природи й кількісного співвідношення утворюючих їхніх компонентів, властивостей, методів виготовлення моделей, способу видалення останніх з форм. Найбільш істотним є перша класифікаційна ознака, тому що природа й співвідношення компонентів модельної сполуки визначають його фізико-механічні, хімічні й технологічні властивості, отже й раціональні методи використання
За зазначеною ознакою модельні сполуки розділені В. А. Озеровим на сім груп (табл. 5.1).
Група 1 — воскообразние сполуки, використовувані для виготовлення моделей як з розплавів, так і з паст. Ці сполуки найбільш універсальні й широко поширені як у СРСР, так і за рубежем. Їхні головні компоненти — парафини, натуральний і синтетичний церезин, стеарин, буроугольний або гірський (монтановий) і торф`яний воски (бітуми), складні ефіри вищих кислот, в окремих випадках ( у цей час рідке, переважно в закордонній практиці) — натуральні воски; бджолиний, кандилльский, карнаубский.
Груп. па | Найменування | Приклади сполук * |
1 | Воскообразние виплавлювані сполуки | ПС 50-50; ПСЄ 70-25-5; Пцбко 70-12-13-5 (Р-3); Пцпєв 62-25-13 ( МВС- ЗА); Пбпсм 60-25-15 (ИПЛ-2); Пбттє 25-35-35-5 (ВИАМ-102) |
2 | Сполуки на основі натуральних і синтетичних смол з добавками воскообразних і інших компонентів | Кпсц 50-30-20; Кцпєбн 80-18-1,6-0,4 ( Травні-Зш) |
3 | Водорозчинні сполуки | Кббк 98-2; Кбнк 90-10 (МОН-ЮК); Кбпвсмс 95,5-2-2,5 (МПВС) |
4 | Термопласти компактні, що й спінюються, віддаляються з оболонок форм випалюванням | Полістирол блоковий, полістирол суспензионний, що спінюється (наприклад, ПСВ-ЛД) |
5 | Легкоплавкі метали й сплави | Ртуть, амальгами ртуті (у практиці вітчизняного виробництва не застосовуються) |
6 | Модельні сполукисуміші, що представляють собою, або сплави сполук різних груп | MB ( мочевинно-воскової сполука, наприклад, суміш розплавів карбаміду й сполуки Пбттє 50-25-20-5) |
7 | Виплавлювані сполуки із твердими наповнювачами | РМ (сме |
* У дужках зазначені умовні найменування (торговельні марки), ие несучі інформацію про компоненти сполуки. Наприклад, «ИПЛ» означає Інститут проблем лиття, де сполука була створи
У якості добавок, що поліпшують реологические властивості сполук, що підвищують їхня міцність і теплостійкість, що знижують крихкість, використовують такі продукти, як, наприклад, кубовий залишок гарячого крекінгу парафіну, касторове масло, триєтанола-мін, пластичне змащення, сибірський віск, етилцелюлозу, каніфоль, а також полиєтилен.
У початковій стадії промислового застосування процесу лиття по виплавлюваних моделях у СРСР широко використовували парафиностеариновие сполуки ПС 50-50, ПС 70-30, Пскм 65-32-3,.
ПСЄ 70-25-5 *, що володіють гарними реологическими властивостями в пастообразном стані й придатні для виготовлення моделей як на машинах, так і за допомогою ручних (шприців. Однак через ряд істотних недоліків (малої міцності й теплостійкості; наявності дорогого, дефіцитного стеарину, схильного до взаємодії з розчинниками єтилсиликатних сполучних і омиленню в гарячій воді) ці легкоплавкі сполуки були пізніше в большдагстве цехів замінені більш економічними бесстеариновими, застосування яких забезпечувало одержання більш міцних і теплостійких (отже, більш точних) моделей, невзаємодіючих зі сполучними суспензії й водою при виплавлении з оболонок форм. Найпоширенішими із другого покоління воскообразних модельних сполук є ПЦБКо 70-12*13-5, ПБПсм 60-25-15, ПБТТє 25-35-35-5 [41 ].
В останні роки створені й набули промислового застосування воскообразние сполуки третього покоління, особливість яких полягає в тому, що в них крім парафіну й інших перерахованих вище головних компонентів уводять синтетичні полімери, наприклад, поліетиленові воски ПВ-200 і ПВ-300 властивості, що поліпшують, сполук, в основному їхню теплотривкість і міцність. До таких сполук ставляться МВС- ЗА, МВС-15, ППК.-1- Властивості найпоширеніших сполук групи 1 наведені в табл. 5.2. Сполуки Р-3, ИПЛ-2, МВС- ЗА, ВИАМ-102, ПЦБ 62-25-13 випускають централізовано [46, 54, 74].
Воскообразние сполуки з буроугольного воску ( до 55 % по масі) і церезину (15—45 %) з добавкою 7—12 % каніфолі широко використовують у ГДР і ЧССР. Для поліпшення технологічних властивостей у ці сполуки додають синтетичні воски, неочищений парафін, стеарин
Воскообразние сполуки різного призначення, що централізовано випускаються в США й Англії, містять каніфоль, парафін, церезин, бджолиний і карнаубский віск, акравоск У и інші синтетичні воски, полиєтилен, дигликольстеарат і інші продукти. Різні сполуки із цих компонентів мають температуру краплі-падіння 65—95 °С, міцність при статичному вигині 4,8—8 МПа, зольність 0,07—0,38 %, вільну лінійну усадку 0,5—1,5 %.
Область раціонального застосування сполук групи 1 досить широка — від масового випуску дрібних сталевих виливків для
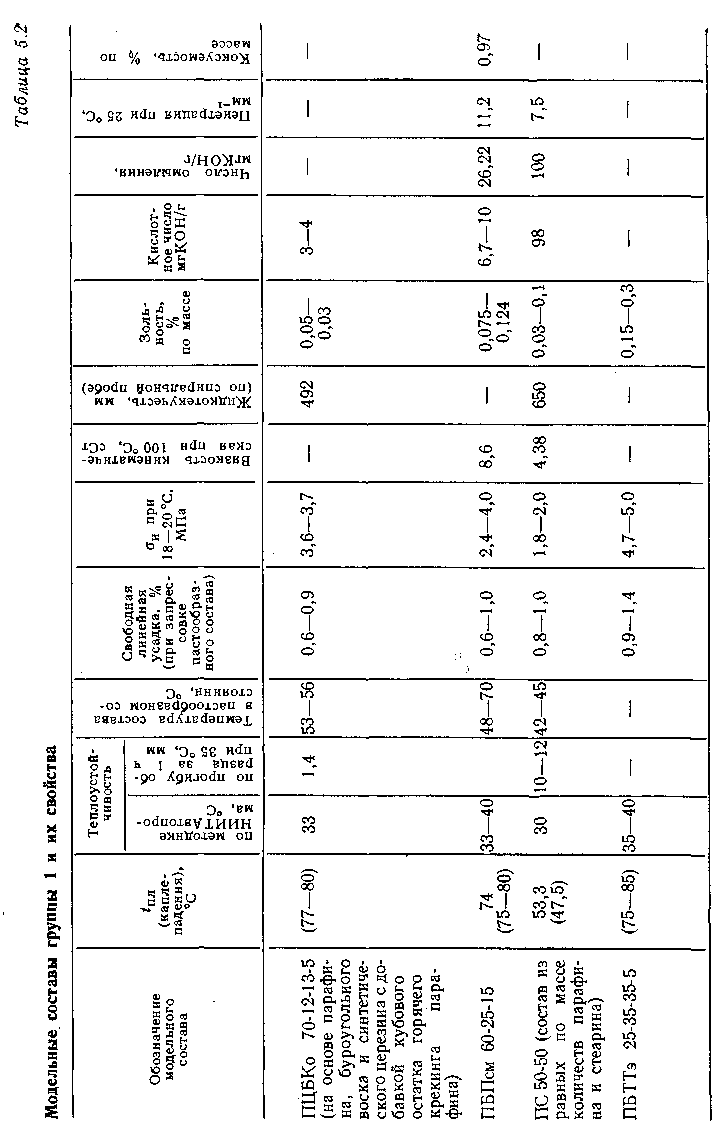
автомобілів, тракторів, сільськогосподарських і дорожніх машин до серійного виробництва складних по конфігурації тонкостінних виливків зі спеціальних сплавів, наприклад жароміцних, у тому числі зі складними внутрішніми порожнинами, виконуваними за допомогою керамічних або, що розчиняються сольових стрижнів
Група 2 — сполуки на основі натуральних і синтетичних смол, термопластов, наприклад полиєтилена й полістиролу, з добавками воскообразних матеріалів (наприклад, синтетичного церезину й парафіну). Використовуються ці сполуки для виготовлення виплавлюваних, а в ряді випадків — випалюваних моделей
Типові представники сполук групи 2 — КПсЦ 50-30-20 і КЦПєБн 80-18-1,6-0,4, головні характеристики яких наведені в табл. 5.3. Вони відрізняються від сполук групи 1 більш високою міцністю й теплотривкістю. Однак застосування цих сполук обмежено внаслідок специфічних недоліків у кожного з них. Сполуки типу МАИ мають високу температуру плавлення й запресовування, температуру каплепадения -~100
З, що виключає віз-.
Таблиця 5.3.
Властивості деяких модельних сполук груп 2 і 3
Модельна сполука | Сполука, % по масі | °н. при 20"З, МПа | Вільна лииейиая усадка, % |
КЦПєБн 80-18-1,6-0,4 | 80 каніфолі, 18 церезину, | 6,2 | 0,7 |
( Травні-Зш) | 1,6 полиєтилена, 0,4 бітуму нафтового | ||
КПсЦ 50-30-20 | 50 каніфолі, 30 полістиролу, 20 церезину | 7,5—8,0 | 0,9—1,43 |
КПсЦ 73-8-19 (модернізований варіант) | 70—75 каніфолі, 5—12 полістиролу, 18—20 церезину | 0. 1. N0 | ПРО. 00. & |
КбПвсМс 95,5-2-2,5 (МПВС-2) | 94—96,5 карбаміду, 1,5—3 полівінілового спирту, 2— 3 Mgs0 4 | 12,0—17,0 | 0 to. 1. про. ъ> |
_КбНк 90-10 (МОН-ЮК) | 90 карбаміду, 10 калієвої селітри (KN0 3 ) | 15,0—19,0 | 0,15—0,4 |
Модельна сполука | Коефіцієнт термічного розширення,. 1/°З | Теплостійкість, °З ( за методикою Ниитавто-Прома) | ПЛ ° з | Зольність, % по масі | Пліт ность. кг/м 8 |
Кцпєбн 80-18-1,6-0,4 | 12-10- 6 | 35 | 90-92 | 0,05—0,08 | 1000 |
( Травні-Зш) КПсЦ 50-30-20 | 25-10" 6 | >40 | Краплі- | 0,03—0,05 | 1000 |
КПсЦ 73-8-19 (модерни | падіння 140 | 0,04—0,05 | 1000 | ||
зированний варіант) КбПвсМс 95,5-2-2,5 | 2,5-10- 6 | 68—72 | 110 | 0,1—0,15 | 1300 |
(МПВС-2). КбНк 90-10 (МОН-ЮК) | 2,6-10- 6 | 70—78 | 125 | 0,15-0,18 | 1320 |
можность застосування при їхнім використанні типового встаткування для готування модельних сполук і виготовлення моделей, у якому теплоносієм в обігрівальних обладнаннях служить гаряча вода. У цих сполук — підвищена зольність і схильність до утвору тріщин, погана смачиваемость суспензією й високий коефіцієнт розширення при нагріванні. поверхневі дефекти, Що часто утворюються на поверхні моделей із цих сполук дрібні (звичайно — усадочного походження) важко помітні при візуальному контролі, тому що сполуки типу МАИ мають темно-бурий колір
Міцні й теплотривкі до 60 °С сплави на основі каніфолі й полістиролу з добавками церезину або парафіну (типу КПсЦ і КПсП) мають наступні недоліки: високу в`язкість у розплавленому стані необхідність, що викликає, перегрівати сполука до 160-175 С при запресовуванні й застосовувати тиску пресування до 1 Мпа й вище, погану виплавляемость із форм, внаслідок чого повернення модельних матеріалів для повторного використання звичайно не перевищує 60 %, а при виготовленні досить тонкостінних виливків настільки невеликий, що моделі використовують, як випалювані. Через високу температуру початку плавлення й поганих реологических властивостей цих сполук моделі при виплавлении з форм тривалий час розширюються, перебуваючи у твердому або високов`язкому стані. Внаслідок цього оболонка випробовує поступово наростаючий тиск модельної сполуки, що розширюється, і повинна мати високу міцність, щоб протистояти цьому тиску, не руйнуючись. Для підвищення опору оболонки руйнуючій дії моделі, що розширюється, доводиться застосовувати дорогою й трудомісткий спосіб формування з рідким наповнювачем, що твердіє. Внаслідок необхідності застосовувати значні тиски при запресовуванні модельних сполукою КПсЦ і КПсП виключається використання гіпсових прес-форм, економічних в умовах дрібносерійного й досвідченого виробництва
Група 3 — водорозчинні сполуки на основі карбаміду, азотних і азотнокислих солей лужних металів" (нітрати й нітрити калію й натрію), гидратированних сірчанокислих солей ( алю-моаммонийних квасцов, сірчанокислого алюмінію й магнію), що плавляться при температурі не вище 35р °З, що володіють малою усадкою, добре розчинних у воді. Такі сполуки застосовують у вітчизняному виробництві точного лиття більш 30 років. У ці сполуки вводять поліпшуючі добавки, наприклад борну кислоту, полівініловий спирт
Найпоширеніші представники сполук групи 3— КбБк 98-2, КбНк 80-20, НкНн 55-45, а також наведені в табл.5.3 КбНк 90-10 і КбПвсМс 95,5-2-2,5. Модельна сполука на основі карбаміду, недавно запатентований у Швейцарії, використовують при виготовленні великих тонкостінних виливків (наприклад, повітряних коліс компресора) масою до 35 кг.
Як видне з табл. 5.3, сполуки групи 3 міцні, теплотривкі, мають малу лінійну усадку, в 2—5 раз меншу, чому у воскообразних сполук (див. табл. 5.2). Головні компоненти сполук дешеві й недефіцитні. Сполуки на основі карбаміду мають високу плинність у розплавленому стані, що в комбінації з малою усадкою дозволяє одержувати моделі, навіть складні й тонкостінні, методом вільного заливання розплаву. Це послужило підставою для використання карбамідних сполук при изготов-лении тонкостінних виливків із глибокими вузькими порожнинами, виконуваними керамічними стрижнями. При цьому послу установки керамічного стрижня в прес-форму запресовування модельної сполуки, що часто викликає деформацію й поломку стрижня, заміняють заливанням карбамідного розплаву, через що стрижень практично не випробовує силових впливів. Схоронність стрижня забезпечується й тим, що після виготовлення оболонки форми моделі на основі карбаміду видаляють без нагрівання розчиненням у воді, отже, вони не виявляють тиски на стрижень, як виплавлюван, розширюються при нагріванні їх до температури початку плавлення модельної сполуки
Використання модельних сполук групи 3 обмежене через наступні специфічні їхні недоліки: гигроскопичности, крихкості, порівняно високої температури плавлення (вище 100 °С), великої об`ємної маси ( до 2,1 г/см
), практичної непридатності для повторного використання (після розчинення), труднощів утилізації розчину. Крім того, що володіють лужними властивостями сольові розплави і їх водяні розчини можуть взаємодіяти з кислими вогнетривами основи оболонки й плівками сполучного, викликаючи утвір дрібних поверхневих дефектів виливків (типу засоров). Захист поверхні сольових моделей шляхом нанесення на них тонких плівок негигроскопичних і хімічно інертних стосовно матеріалів суспензії речовин, поки у виробництві не використовують. Цей метод практично може бути застосований, мабуть, тільки в умовах серійного виробництва великих виливків
Спеціальною областю застосування сполук групи 3 є виготовлення з них стрижнів, що розчиняються у воді, для одержання у виплавлюваних моделях (переважно зі сполук групи 1) складних каналів і порожнин, нездійсненних у прес-формі, за допомогою металевих стрижнів (див. п. 5.6).
Група 4 — термопласти, з яких на практиці застосовують тільки компактний (монолітний) полістирол, що й перебуває в стадії виробничого випробування, обмежено використовуваний полістирол, що спінюється
Тому що полістирол при нагріванні не плавиться, а тільки розм`якшується (температура.початку розм`якшення ~80 °С), переходячи у вязкопластичное стан, технологічні властивості його прагнуть підвищити спеціальними добавками, наприклад, уведенням до 10 % жирних кислот для зниження в`язкості, підвищення плинності в нагрітому стані ( при пресуванні моделей) і зменшення крихкості готових моделей
Суспензионний полістирол Для вспенивания перспективний, як матеріал для одержання випалюваних моделей в умовах масового виробництва дрібних виливків, замість воскообразних виплавлюваних сполук, а також при серійному випуску порівняно великих тонкостінних і змінного перетину виливків, наприклад лопаток турбін довжиною до 0,5 м [551. До переваг розглянутого матеріалу ставляться: теплотривкість моделей, що дозволяє сушити шари оболонки форми прискорено, при 70—80 °С, достатня загальна й поверхнева міцність при малій гаданій щільності: 120—250 кг/м
для дрібних тонкостінних і навіть 40— 80 кг/м
для окремих великих моделей. Зменшення об`ємної маси моделей супроводжується зниженням їх міцності, точності розмірів і підвищенням шорсткості поверхні. Для виключення останнього недоліку О. К. Кошовим, В. М. Белецким й.
Н. Д. Шулаком запропонований метод нанесення акрилатного покриття на робочу поверхню прес-форми перед заповненням її гранулами полістиролу для вспенивания.
По даним розроблювачів процесу лиття в багатошарові оболонкові форми по випалюваним пенополистироловим моделям, відлитим під тиском (ХФ ВНИИЛитмаш), точність одержуваних деталей перевершує точність, що досягається при литті по виплавлюваних моделях з легкоплавких модельних сполук [5]. Однак, як показали експерименти [1], виконані в умовах комплексномеханизированного виробництва сталевих виливків по випалюваним пенополистироловим моделям, підвищена в порівнянні з литтям по виплавлюваним воскообразним моделям точність деталей може бути забезпечена тільки при строгому дотриманні певних умов їх виготовлення (температура модельної сполуки, що впорскується, --• °180 С, прес-форми 29-34 С щільність, що видасться, моделей р = 200-ь220 кг/м®, оптимальний час витримки моделей у прес-формі й на повітрі після витягу з останньої), а також з обліком інших факторів, у тому числі конструкції моделі в місця підведення, модельної сполуки. Стабілізація розмірів пенополисти-ролових моделей завдяки забезпеченню найбільш сприятливих умов їх формування дозволяє одержувати виливки з точністю розмірів вище квалітету 13 (СТ СЄВ 144—75), тоді як при традиційному процесі лиття по виплавлюваних моделях зі сполук типу Р-3 це звичайно не досягається
Для виготовлення литих пенополистиролових моделей Охтинским НПО «Пластполимер», разом із ХВ ВНИИЛитмаш, розроблена спеціальна марка полістиролу, що спінюється, ПСВ-ЛД (, що випускається ПО «Пластик» у г. Вузлова (по ТУ 6-05-05-148—78). Основні технічні характеристики ПСВ-ЛД: відносна в`язкість 1,55—1,65; зміст порообразователя 4,5—5,5 %; зміст мономера стиролу не більш 0,035 %; вологість не більш 1 %; зольність не більш 0,02 %; показник плинності розплаву (ПТР) (15 ± 6) г/10 хв; зміст третинного додецил-меркаптану 0,025 %.
До групи 4 слід віднести й розроблювальні в Московському авіаційному технологічному інституті ім. К. Є. Ціолковського (МАТИ) сполуки з, що спінюються в прес-формі й отверждающихся поліефірів
Група 5 — легкоплавкі метали й сплави. З металів промислове застосування як модельний матеріал одержала ртуть, що вільно заливається в прес-форми при кімнатній температурі, що й заморожується в ацетоні, охолодженому до —60 °С. Процес лиття по ртутних моделях (« меркаст-процес»), докладно описаний в англійській і американській спеціальній літературі, незважаючи на високу якість одержуваних виливків, широкого поширення у світовій практиці лиття по виплавлюваних моделях не одержав і в СРСР не застосовується внаслідок виняткової токсичності пар ртуті, складності методу, високої вартості модельного матеріалу
У закордонній літературі неодноразово повідомлялося про можливість використання для виготовлення моделей легкоплавких, переважно євтектических сплавів металів, наприклад сплаву Вуда (основа — вісмут, t
„ = 68 °С). Однак відомостей про промислове застосування таких модельних сплавів ні.
Група 6 — модельні сполуки, що представляють собою механічні суміші або сплави сполук, наприклад, водорозчинних (група 3) і воскообразних (група 1). За даними Н. С. Севостья-Нова й В. В. Апиллинского, у таких сполуках вдається значно зменшити Недоліки утворюючих їх складових: гигроскопичность, крихкість і схильність до взаємодії з формою карба-мидних сполук, малу міцність і теплотривкість воскообразних легкоплавких матеріалів. Однак готування комбини* рованних сполук ускладнюється через погану сумісність компонентів, а при запресовуванні їх необхідно застосовувати тиску (>0,5 Мпа), що суттєво перевищують застосовувані для воскообразних сполук. Наявність же останніх у суміші приводить до зниження міцності й теплотривкості, характерних для карба-мидной складовій
При видаленні моделей у гарячій воді повторно може бути використана тільки воскообразная частина комбінованого сполуки й виникають труднощі з утилізацією карбамиднош розчину
Група 7 — сполуки із твердими наповнювачами. Основа їх — переважно сполуки групи 1, у які вводяться порошки, наприклад, синтетичних смол або тугоплавких восков; щільність їх близька до щільності розплаву основи. Такі порошки утворюють тверду суспензію в розплавах основи сполуки, знижуючи й стабілізуючи усадку, отже, підвищуючи точність моделей, а також збільшуючи їх міцність і формостійкість. Уведення в розплав воскообразного модельної сполуки 10-15 % порошку синтетичної смоли знижує вільну лінійну усадку цієї сполуки при зат-рердеванщ із 1,5-2 до 0,5 %,