..
Готування легкоплавких воскообразних сполук. Модельні сполуці групи 1 на основі парафіну, церезину й інших легко-.
плавких матеріалів готують у водяних, гліцеринових або масляних лазнях з електричним або газовим підігрівом. Застосовують для цієї мети також термостати
Вихідні матеріали перед завантаженням подрібнюють до шматків розміром не більш 50 мм, що прискорює процес розплавлювання. При виготовленні сполук з, що добре змішуються матеріалів компонента завантажують і розплавляють у порядку зростання температур їх плавлення
При виготовленні сплавів, що містять етилцелюлозу, спочатку розплавляють складові, у яких етилцелюлоза добре розчиняється, наприклад церезин, каніфоль, стеарин. Температуру „ розплаву підвищують до 120—140 °С, після чого поступово, у кілька приймань, при безперервному перемішуванні вводять єтил-целюлозу у вигляді тонкого порошку (просіяного через сито № 020). Після розчинення етилцелюлози ( через 20-25 хв) уводять інші складові сплаву, перемішують отриманий розплав, фільтрують його через металеву сітку або через марлю, їло-женную в 2-3 шару. Готові сполуки розливають у ванночки або листи (изложници), щоб одержати плитки товщиною не більш 40 мм.
Готування пастообразних сполук. Пастообразние сполуки готують охолодженням розплаву при одночасному безперервному перемішуванні його до пастообразного стану. Обладнання для готування пастообразних сполук або виконують у вигляді окремих установок, або поєднують із машинами для виготовлення моделей
Установки для готування пастообразних сполук можуть бути з лопатевими, поршневими й шестеренними змішувачами
Установка з лопатевими змішувачами, показана на мал. 6.1,* призначена для готування пастообразних модельних. срета* вов типів ИПЛ-2, Р-3, ПС 50-50 або аналогічних їм по властивостей* і подачі до запресувального обладнання
Бачки-Змішувачі 2 (2 шт.), а також верхній 3 і нижній £ циліндри, що служать для подачі готової модельної сполуки шзд. тиском до запресувального обладнання, помешени в резервуар б
) заповнений теплопередающей рідиною (водою, маслом, глице- рином), яку нагрівають за допомогою єлектр онагревательньигєле-ментовку. Температура теплопередающей рідини автоматично підтримується на рівні, що відповідає пастообразному стану модельної сполуки
Бачки-Змішувачі працюють по черзі. У той час як в одному з них приготовляется паста, з іншого готова сполука подається до зайрессовочному обладнанню. Осі змішувачів 9 із закріпленими на них лопатами 10 приводяться в обертання від електродвигуна через редуктор. Електродвигун з редуктором і перехідною втулкою змонтовано на поворотному кронштейні 14, жорстко з`єднаному з вертикальною віссю. Повертаючи кронштейн 14, можна приєднувати електропривод за допомогою втулки /
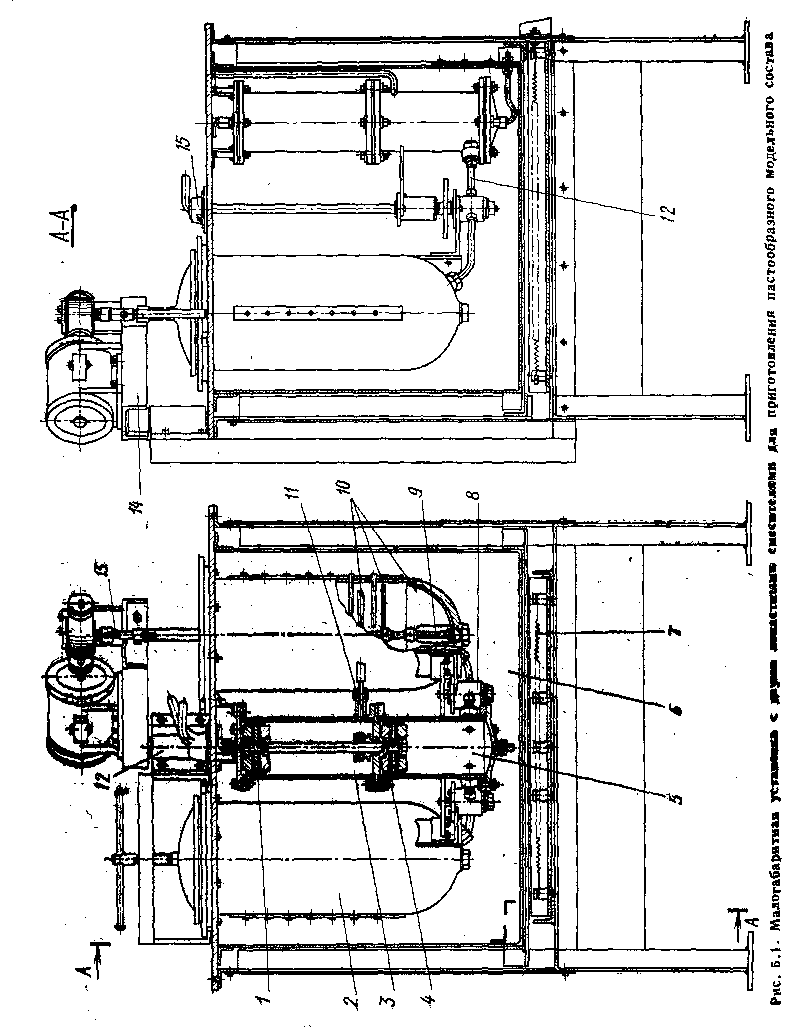
Модельна сполука за 20—25 хв перемішування здобуває пастообразное стан. Потім електропривод відключають і приєднують до осі другого змішувача, а бачок з готовою сполукою закривають кришкою. Далі поворотом рукоятки 15, пов`язаної із пропускними клапанами 8 трубами 12, з`єднують порожнини бачка, що містить готовий пастообразний сполука, з порожниною нижнього циліндра 5, службовця для нагнітання модельної сполуки до місця запресовки його в прес-форми. Поршень 4 нижнього циліндра 5 і поршень 1 верхнього (пневматичного) циліндра 3 закріплені на загальному штоку. При подачі стисненого повітря через штуцер И в верхній циліндр шток з поршнями піднімається нагору, поступово займаючи крайнє верхнє положення. При цьому модельна сполука засмоктується в нижній циліндр 5. Потім перекривають клапан 8 і подають стиснене повітря через штуцер у верхню частину циліндра 3. При цьому поршень 1, а отже, і поршень 4 опускаються, і модельна сполука під тиском подається до запресувального обладнання
Малогабаритні обладнання з поршневими змішувачами, а також зі змішувачами у вигляді шестеренного насоса являють собою одне ціле з установками для виготовлення моделей. Тираспольський завод ливарних машин ім. С. М. Кірова випускає установки мод. 651 для готування пастообразних сполук типів ИПЛ, Р-3, ПС, температура розплаву яких не перевищує 80 °С. В установці об`єднані плавильний агрегат, ємнісної бак, пастоприготовительний агрегат, дві насосні станції, що забезпечують подачу нагрівальної води з температурою, що відповідає розплавленому й пастообразному станам модельної сполуки, а також шафи керування
Установка універсальна, тому що може працювати й в автоматичній лінії в комплекті із двома карусельними автоматами мод. 653, і в комбінації зі шприцами клапанного типу різної конструкції, що приводяться в дію вручну, при обслуговуванні до 20 робочих місць запресовування. Вихідні матеріали (повернення й свіже д(єбавки) завантажують у плавильний агрегат, що полягає з верхнього й нижнього баків. Днище верхнього бака виконане. у вигляді трубчастої решітки, на яку попадають і швидко розплавляються шматки твердих свіжих добавок. По трубах циркулює пара. Температура води, що надходить від насосно-обігрівальної станції ■ автоматично підтримується на рівні 80—90 °С. Цією водою обігрівається сорочка баків. Із плавильного агрегату розплав модельної сполуки перекачується відцентровим насосом у ємнісний бак, з якого самопливом надходить у пастоприготовительний агрегат із шестеренним змішувачем. Необхідне для замешивания до модельного складу кількість повітря може надходити або за рахунок підсмоктування з атмосфери при заповненні змішувача розплавом через відкриту лійку, або через ротаметр стиснене повітря вводиться в герметично приєднану до змішувача трубу для підведення розплаву. Приготовлена модельна сполука надходить в, що обігрівається пастосборник, звідки пневмати-.
ческими насосами подвійної дії по трубопроводу транспортується при заданому тиску до запресувального обладнання автоматів для виготовлення моделей
Установка мод. 651 має електричне й пневматичне керування виконавчими механізмами й може працювати як в автоматичному, так і в налагоджувальному режимі. Температура пастообразного сполуки регулюється в межах 40—60 °С. Зміст повітря в складі також регулюється й може становити до 20 % за обсягом. Найбільша продуктивність установки при безперервному режимі роботи 0,063 м
3
/ч. Тиск модельної сполуки при подачі в запрес-совочние обладнання (у пастопроводе) регулюється й може становити до 1 МПа. Температура пари 100—110°С, тиск 0,11— 0,14 МПа, витрата 25 кг/год, витрата стисненого повітря при тиску 0,5 МПа не більш 0,5 м
3
/год, тиск його 0,4—0,6 МПа, витрата води не більш 1 м
3
/год, загальна встановлена потужність 34,1 кВт, габаритні розміри установки ( при розташуванні агрегатів у лінію) 7600 X X 270ОХ185Омм.
Для готування пастообразного модельного сполуки з розплаву з температурою не більш 80 °С при більших масштабах виробництва призначена установка мод. 652А с найбільшою продуктивністю до 0,5 м
3
/ч. Принцип готування пастообразного сполуки й обладнання агрегатів для здійснення цього процесу аналогічні використовуваним в установці мод. 651, але число пастоприготовительних агрегатів збільшене до чотирьох, насосно-нагрівальних станцій до восьми. Загальна потужність установки 133,1 кВт ( у тому числі електродвигунів 37,1 кВт), а габаритні розміри при розташуванні агрегатів у лінію 21350 x 5620 x 2410 мм.
Шестеренні змішувачі найбільш продуктивні, надійні в роботі й компактні, тому ними в останні роки заміняють змішувачі інших типів (лопатеві, поршневі), як у великих, так і в малогабаритних установках. Перевага шестеренних змішувачів-насосів у малогабаритних установках для готування й запресовування пастообразних сполук полягає в тому, що стабільність їх роботи меншою мірою залежить від властивостей модельних сполук, насамперед реологических. Є досвід застосування установок із шестеренними насосами навіть для виготовлення моделей з такої грузлої й тугоплавкої модельної сполуки, як КПсЦ.
На мал. 5.2 зображена схема автомата для виготовлення моделей конструкції НИИТАвтопром і обслуговуючої його установки для готування пастообразного сполуки із шестеренним змішувачем конструкції Московського прожекторного заводу (автори Ю. Д. Іванов і А. Р. Рабинович).
Плавильний агрегат 1, бак-відстійник 2, обігрівальні й інші обладнання, що обслуговують ці вузли, подібні застосовуваним в установці мод. 651 (описана вище). При використанні модельної сполуки ПЦБКо 58-24-13-5 температура води, що подавалися насосною станцією III, підтримується в межах 95—97 °С. Обігрівальна бак 2 вода, що подавати насосною станцією II, має температуру
Повітря від мережі
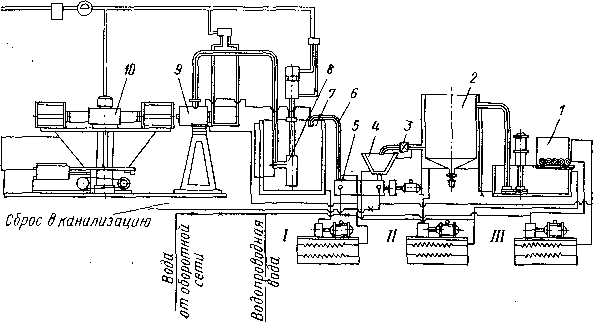
Рис. 5.2. Схема автоматичної установки конструкції НИИТАвтопромадля виготовлення моделей з пастообразного сполуки
.
75—80 °С. Температура води, що подавалися насосною станцією I відповідає температурі зазначеної модельної сполуки в пастообразном стані, тобто рівна 52—56 °З.
, Що Перекачується відцентровим насосом з бака плавильного агрегату 1 у бак 2 сплав Р-3 повинен мати температуру 80—85 °С. Трубопровід щоб уникнути утвору настилей після операції перкачивания слід продувати
Дл"я готування пасти розплав модельної сполуки з бака-відстійника 2 надходить через кран 3 і лійку 4 у шестеренний змішувач 5. Готовий пастообразний сполука зі змішувача 5 по трубопроводу, що обігрівається, 6 подається в бак-накопичувач 7, а з нього насосом 8 в автоматичне запресувальне обладнання 9, що обслуговує десятипозиционний автомат 10.
Перед початком роботи шестеренного змішувача (мал. 5.3) корпус його підігрівають водою, що подавалися насосною станцією III (див. мал. 5.2), або пором для очищення від затверділих залишків модельної сполуки. Після прогріву змішувача в його охолоджувальну сорочку бйускают воду з водопровідної мережі, забезпечуючи інтенсивне охолодження розплаву, що переробляється в пасту, модельної сполуки. Одночасно з охолодженням змішувача починається подача в нього розплаву. У корпусі змішувача на двох валах змонтовані
10 пара шестірень. Кожна пара шестірень, що перебувають у зчепленні, відділена від сусідніх сталевою перегородкою. У кожній парі одна із шестірень вільно посаджена на вал, а друга — на шпонці, у сусідній парі — навпаки. Вали обертаються від загального привода в одному напрямку
Таким чином, шестірні на одному валу парні, а на іншому непарні обертаються разом з валом, приводячи в рух вільно насаджені парні шестірні, у результаті чого суміжні пари
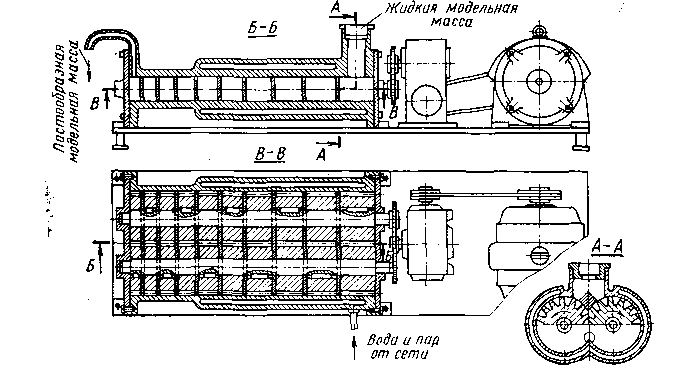
Рис. 5.3. Схема шестеренного багатоступінчастого змішувача конструкції заводу «Прожектор*.
.
шестірень обертаються в різні сторони. Ширина шестірень у кожній парі поступово зменшується в напрямку руху модельної сполуки, чим забезпечується постійний напір його в напрямку видавлювання, а також поліпшується заповнення западин зубів і перемішування сполуки
Вступник до першої пари шестірень розплав заповнює западини зубів, переноситься в нижню зону й видавлюється вхідними в зачеплення зубами через отвір перегородки в сусідню обойму, де зазнає впливу обертової у зворотному напрямку другої пари шестірень, що переміщає модельну сполуку нагору. Із другої пари шестірень сполука попадає на третю й так, прохолоджуючись до температури пастообразного стану й багаторазово перетираючись, проходить змішувач і видавлюється 10-й парою через бак-накопичувач, що обігрівається трубопровід у пасти
У процесі просування через шестеренний змішувач модельна сполука не тільки багаторазово перемішується, здобуваючи однорідність, але й інтенсивно прохолоджується, тому що заповнює невеликі об`єми між зубами, у результатечего питома поверхня охолодження в порівнянні із циліндричними (поршневими й лопатевими) змішувачами збільшується в 20—30 раз
Конструкція шестеренного змішувача забезпечує не тільки висока якість готування пасти й більшу продуктивність цього агрегату, але й надійність його роботи через те, що практично виключена небезпека застивания в змішувачі модельної сполуки, активно подаваного шестірнями через перегородки обойм
Повітря, що замішується в пасту, надходить через отвір у завантажувальному каналі
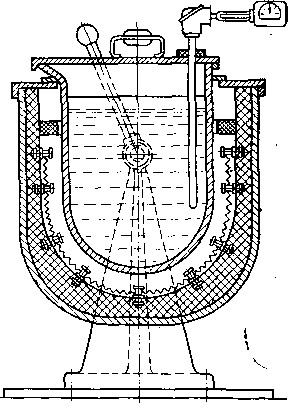
Рис. 5.4. Поворотна електропіч опору для варіння тугоплавких модельних сполук
.
Готування тугоплавких модельних сполук. Модельні сполуки на основі каніфолі, типів КПсЦ, МАИ й ін. готують у поворотних електропечах, оснащених терморегуляторами (мал. 5.4).
Підготовка складових полягає в роздрібненні їх до шматків розміром не більш 40 мм. Звичайно спочатку розплавляють каніфоль, потім при температурі 140—160 °С додають високообразние компоненти, підвищують температуру до 200—220 °С и вводять у розплав полістирол (невеликими порціями, при постійному перемішуванні).
Усі модельні сплави необхідно готувати в добре вентильованих приміщеннях. Лазні, термостати й електропечі для готування модельних сплавів слід поміщати у витяжні шафи або під спеціальні парасолі із примусовою витяжною вентиляцією. При цьому необхідно дотримувати правил протипожежної безпеки
Готування сполук групи 7 із твердими наповнювачами може бути розглянуте на прикладі сполуки РМ, основою якого служить Р-3, твердим наповнювачем — порошок карбаміду, а добавкою, що стабілізує суспензію, що полягає з розплаву воскообразного матеріалу й твердих часток сечовини, є каніфоль. Спочатку в баку-термостаті із гліцериновою лазнею розплавляють сполука Р-3, узятий у кількості 55—56 % загальної маси состава, що приготовляемого. У нагрітий до температури не більш 110 °С розплав замішують здрібнену каніфоль (4—5 % загальної маси сполуки)з про повного розплавлювання й змішування її з матеріалом основи. Карбамід попередньо подрібнюють у кульовому млині, просівають через сито із гніздами не крупніше № 020 і висушують у печі-термостаті при 100—110 °С, після чого поступово, при безперервному перемішуванні, уводять у розплав Р-3 і каніфолі. У наведеному рецепті кількість карбаміду становить 40 % усієї маси состава, що приготовляемого, однак воно може бути збільшене до 60 % шляхом скорочення кількості Р-3.