На мал. 1.14 показана неправильна тонкостінна деталь зі стінками I товщиною 2 мм і найбільшим розміром 344 мм, відлити яку можна тільки методом лиття по виплавлюваних моделях, тому що тільки в нагрітій до 850—900 °С формі можна забезпечити заповнення гінких стінок. Для одержання виливка застосовували спеціальний спосіб виготовлення моделі. У стрижневому ящику одержували розчинні стрижні (мал. 1.15, а), які набирали в прес-форму (мал. 1.15, б), і заливали модельна сполука, після чого модель поміщали у воду для розчинення стрижнів. На мал. 1.15, у показана модель (частина стрижнів розчинена).
Раніше таку деталь виконували з 80 П-Образних елементів, що зварюються, вирубаних і штампованих з листової сталі товщиною 2 мм. Застосування лиття взамен`щтамповки й зварювання в 3, 5 рази
Рис. 1.13. Виготовлення деталі з п`яти заготовок (/ - про): а — зварюванням їх (стара технологія); б — виливок деталі по виплавлюваних моделях (нова технологія).
.
знизило втрати металу при холодному штампуванні й трудомісткість при зварюванні
Розчленовування деталей. Іноді доцільно розчленувати великогабаритну деталь на кілька литих заготовок меншого розміру, а потім з виливків за допомогою зварювання виготовити деталь. На мал. 1.16, а показана лите-зварена деталь із найбільшим розміром 650 мм. Виготовлення такої деталі зварюванням із чотирьох однакових литих частин (мал. 1.16, б) виявилося найбільш доцільним
Армування, деталей. Застосування армування виливків вкладишами значно поліпшує технологічність деталей. Армуванням можна усунути скупчення металу на окремих ділянках. За допомогою трубок можна одержати складні криволінійні отвори, які не можна виконати керамічними стрижнями. Прикладом служить турбінна лопатка (мал. 1.17). Сталеві трубки внутрішнім діаметром 2,4 мм і товщиною стінок 0,3 мм застосовували у вигляді вставок у прес-форму. При заливанні лопаток стиснене повітря
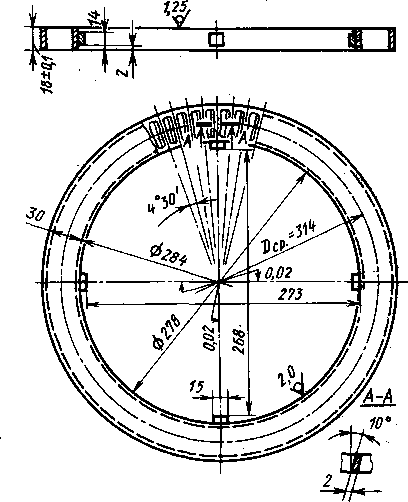
Рис. 1.14. Складна тонкостінна деталь
у трубки не подавали, тому що перетин виливка був невеликим. Кінці сталевих трубок були закриті, щоб уникнути влучення в них суспензії
.
.
Аналогічним способом виготовляли форсунки, використовувані для подачі палива в камеру згоряння. Форсунка має два отвори (одне діаметром 4,75 мм, інше
з,2 мм). Прес-форма для виплавлюваної моделі була зроблена так, щоб можна було встановити трубки з коррозионно-стійкою стали зі стінками товщиною 0,8 мм.
і, таким чином, виготовляти моделі з розташованими усередині них трубками. Моделі литниково-живильної системи приєднували до моделей виливків. Трубки з боку ливникової системи з`єднували між собою. У такому виді на модельний блок наносили оболонку й заформовивали в опоку з висновком трубок у нижню частину. Після виплавления моделі й прожарювання форми до одному кінцю трубки приєднували шланг для стисненого повітря. У процесі заливання й затвердіння металу трубки прохолоджували стисненим повітрям, що йдуть по трубках під тиском 0,05 Мпа. Таким чином, була вирішена проблема одержання дрібних отворів у виливках складної форми
Вибір товщини стінки виливка. При виборі товщини стінок виливка слід ухвалювати найменш розрахункову міцність, що забезпечує необхідну. Якщо необхідно зберегти товщину стінки, а міцність її недостатня, слід підбирати більш міцний сплав. Найменша товщина стінок виливка, який може бути виконана, 0,5-2 мм. товщина, що найбільше часто зустрічається, 2-5 мм. Тонкі стінки виливків можуть бути виконані тільки при площі їх поверхні не більш ЮОХ 100 мм. Якщо площа більше, те стінки або не заповнюються, або виходять зі значними коливаннями по товщині внаслідок деформації оболонки. Замість прямих стінок краще виконувати скривлені, передбачати технологічні отвори (вікна) діаметром 10-20 мм (мал. 1.18) або ребра
Рис. 1.16. Великогабаритна деталь, зварена із чотирьох литих однакових заготовок (а), і лита заготовка (б)
Рис, 1.17. Турбиииие лопатки:.
а — креслення лопатки; б — пресс-фора для моделі й виплавлювана модель; в — лита лопатка й модельний блок
.
Сполука протилежних шарів оболонки через отвори в стінках за умови, що відстань між отворами або між отворами й границею стінки не перевищує 50 мм, попереджає прогин оболонки навіть без додаткових ребер. Наприклад, на досвідчених виливках розміром 100x150 мм зі стінкою товщиною всього 1,2 мм при чотирьох отворах прогин оболонки не спостерігався
Не виключається можливість виготовлення товстостінних деталей, але при цьому в серцевині виливка, що не одержує харчування, будова металу менш щільна; причому при товщині стінок більш 6 мм може утворюватися осьова пористість усадочного походження. Чим товстіше стінка, тим більше осьова пористість
Таким чином, збільшення товщини стінок не обумовлює пропорційного збільшення міцності. Тому краще підсилювати виливок ребрами. Ребра сприяють також кращому заповненню тонких стінок виливків........
Сполучення двох стеиок, розташованих паралельно. Слід уникати стінок у виливку з нерівномірною товщиною, скупчень металу на окремих ділянках і різких переходів від великого перетину до малого. Дотримання плавних переходів є основною вимогою, пропонованим до конструкції литому деталі. Плавний перехід забезпечує деталі більшу надійність, чому збільшення товщини стінки. Якщо не можна уникнути сполучень масивних перетинів з тонкими, то потрібно передбачити плавні переходи між ними
.
.
Товщини двох стінок, що сполучаються, розташованих паралельно (мал. 1.19), повинні різнитися не більш ніж в 4 рази. Якщо ця відмінність більш ніж в 4 рази, слід застосовувати клинове сполучення. Довжина похилої частини повинна бути не менш чотирьох величин різниці толщин, що сполучаються стінок. При різниці толщин менш чому в 2 рази застосовують жолобники
Радіус жолобника повинен бути обраний таким, щоб з одержанням плавного переходу запобігти місцевому скупченню металу. Радіус R жолобників установлюють залежно від толщин малої
.
Рис. 1.18. Виливок з ливниковою системою: / — технологічні отвори; 2 — ребра
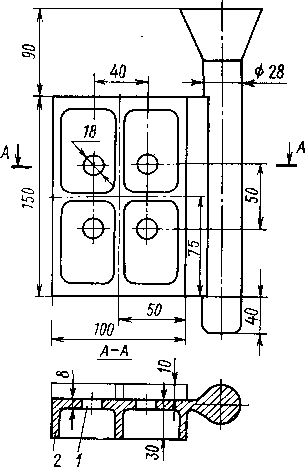
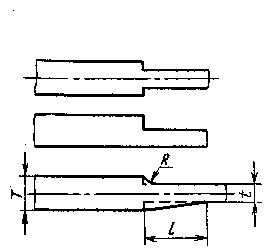
Рнс. 1.19. Сполучення двох стінок паралельне:.
T>4t I > 4 (T-t) R = 2t
Рис. 1.20. Сполучення двох стеиок під різними кутами (а), утвір усадочної пористості й тріщин (показане стрілкою) у внутрішньому куті при малому радіусі жолобника (б);.
T1>4 (Г-0; з = Г-#; г — (Г + 0/S; R= — Г + t.
стінки рівним 21. Слід прагнути гранично зменшувати різноманітність радіусів жолобників і скруглений у виливків; бажане звести їх до одному радіусу. У цьому випадку значення радіуса може бути зазначене на кресленні литому деталі, тільки в примітці, наприклад, «ливарні радіуси внутрішніх кутів R
». Радіус вибирають у межах 1/5-1/3 середнього арифметичного товщини стінок, що сполучаються, якщо по призначенню й конструкції деталі не потрібно іншого радіуса. Слід ухвалювати радіуси жолобників відповідно до кращого рядом чисел: 1, 2, 3, 5, 8, 10, 15, 20, 25, 30, 40 мм.
Сполучення двох стінок під різними кутами. Таке сполучення відрізняється від попереднього тим, що в ньому утворені зовнішній і внутрішній кути (мал. 1.20). Залежно від величини внутрішнього кута й радіуса жолобники затвердіння може відбуватися з утвором усадочної пористості в зоні від центральної частини сполучення до поверхні внутрішнього кута. Якщо внутрішній кут і радіус жолобники в ньому дуже малі, усадочна пористість і тріщини утворюються в куті на внутрішній поверхні сполучення
У міру збільшення радіуса жолобники й внутрішнього кута сполучення між стінками виливка усадочна пористість і раковини переходять у центр вузла сполучення. Зі збільшенням кута або радіуса жолобники при сполученні двох стінок характер затвердіння такий же, як при затвердінні однієї стінки, де можна застосовувати методи по усуненню осьової усадочної пористості так само, як і в одній стінці. У випадку сполучення стінок різної товщини їх співвідношення й довжину конічної частини призначають за умовами, зазначеним у попередньому сполученні. Найбільш важливою завбільшки цім сполученні є радіус жолобника у внутрішньому куті, який визначають залежно від останнього, утвореного стінками виливка й товщини стінок, що сполучаються. Радіус жолобника г = (Т + f)/S (де Г и f — товщини стінок, що сполучаються, виливка; S — ступінь замкнутості) визначається по мал. 1.21.
Сполучення трьох стінок під різними кутами (мал. 1.22). Таке сполучення відрізняється від попереднього (див. мал. 1.21) тим, що в ньому утворено два внутрішні кути. Усі величини визначають у цім сполученні по методах, зазначених для розрахунків їх у попередньому. Сполучення більш трьох стінок в один вузол не рекомендується; наприклад, сполучення чотирьох стінок (мал. 1.23) необхідно виконувати за схемою трьох стінок (див. мал. 1.22).
Конструювання пазів, порожнин і отворів. При конструюванні литих деталей випливає по можливості уникати глибоких пазів і вузьких порожнин, для оформлення яких можуть знадобитися стрижні. Ширина паза або відстань між виступами або ребрами, що утворюють ширину й висоту його (мал. 1.24), можуть бути виконані при Я
< 2d, якщо для кольорових сплавів d 1 мм, а для сталі d 2,5 мм.
Рис. 1.21. Графік для визначення ступеня замкнутості
.
.
Рас. 1.23. Сполучення чотирьох стінок під різними кутами
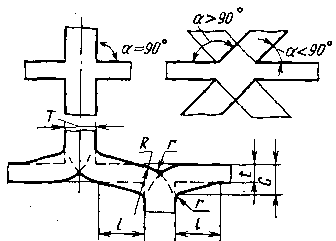
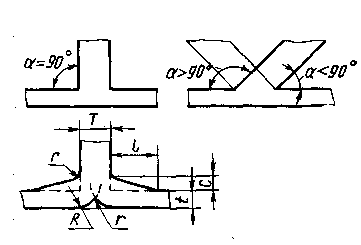
Рис. 1.22. Сполучення трьох стінок під різними кутами:
Г
< 4f; 14 (T — i); C = T — t, r = = {T + t)/S-. R-T+t
Рис. 1.25. Виконання порожнин у виливках:.
а —- неправильне; б-б- правильне
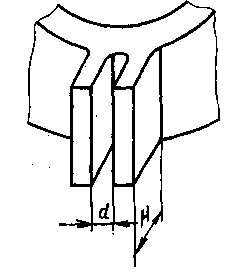
Рис. 1.24. Паз у виливку
Внутренняяполость отливкидолжна мати вихідні отвори, достатні для надійної й міцної сполуки внутрішньої частини оболонки із зовнішньої. Вихідні отвори повинні бути по можливості продовженням порожнини литому деталі. Оболонка, що утворює порожнина Л деталі, зображеної на мал. 1.25, а, має тільки один вихідний отвір, який не може забезпечити стійке положення внутрішньої оболонки при прожарюванні форми і її заливанню. У виправленій конструкції деталі (мал. 1.25, б) порожнини А и В з`єднані й утворюють загальну порожнину С. Якщо отвір використовують як опорне для обробки або міряльного інструмента, його поверхня необхідно обробляти, тому що лита поверхня отвору для зазначених цілей непридатна. Якщо отвір використовують під болт вільної посадки, під мастильний отвір, де не потрібні тверді допуски, то обробляти відлиту поверхню не потрібне
Одержання малих отворів, оточених великий масою металу, викликає відомі труднощі при литті на відміну від виконання більших і простих за формою отворів. Наприклад, наскрізний отвір діаметром 5 мм легко одержати при глибині його до 8- 10 мм, а при глибині 100 мм — тільки за допомогою керамічних стрижнів (див. п. 6.9). Якщо отвір круглий, то застосування стрижнів практично доцільно, але якщо отвору мають спеціальний контур, те їх одержання обходиться дорого, тому що ускладнюється виготовлення стрижня. Одержати у виливку глухий отвір завжди значний сутужніше, чим наскрізне. Для одержання в моделі отворів складної форми можна використовувати розчинні стрижні, там де металеві стрижні прес-форми не можна витягти з моделі (див. гл. 5). Доцільно в ряді випадків армування виливків (див. мал. 1.17).
Мінімальні отвори до 0,5 мм допускають у стінках деталей товщиною до 1 мм.
Застосування литому різьблення. Литі різьблення слід використовувати тільки в тому випадку, якщо вони спеціальні й з великим кроком, тому що виконання різьблень литтям представляє більші трудносги, особливо при дрібному кроці, коли ускладнюється виготовлення моделей, а на виливках у поглибленнях різьблень часто виникають дефекти у вигляді металевих припливів
Щ Виконання конусности або ухилів на виливках. При проектуванні деталей конструктор повинен мати на увазі, що моделі слід виймати із прес-форми без поломок і порушення їх геометрії. Тому необхідна конусность на поверхнях, перпендикулярних до площини рознімання прес-форми. Якщо модель оформляють у декількох частинах прес-форми, то конструктор деталі повинен указати, які поверхні можуть мати конусность, а які ні.
Конусность відповідно до ДЕРЖСТАНДАРТ 3212-80 може бути виконана (мал. 1.26, а-в) трьома способами: збільшенням товщини стінки, зменшенням її або одночасним зменшенням і збільшенням
мал. 1.26. Конусность (ухили) иа виливках
.
Конусность щодо висоти стінки задається в градусах або міліметрах. При цьому вона на ту саму висоту може бути різної залежно від матеріалу прес-форми
Якщо вертикальні стінки обробляють, то конусность дають завжди «у плюс». Також «у плюс» дають конусность, якщо стінку виливка не обробляють, але товщина її менше 3 мм. При товщині стінки 3-6 мм конусность, як правило, дають «у плюс-мінус», а при товщині більше 6 мм — «у мінус». Конусность може спотворити форму необроблюваних поверхонь і побільшати масу виливків. Тому литому деталі доцільно надавати конструктивні ухили
Для спрощення виготовлення й зниження собівартості виливків бажане мати просту рознімну прес-форму, при якій виключалося б застосування складних стрижнів і додаткових маніпуляцій із прес-формою й моделлю
Конструювання виступів, бобишек і заплічок для виходу інструмента. У стінках виливків, де необхідно виконувати отвору, у більшості випадків роблять спеціальні виступи й бобишки. Висоту виступу встановлюють залежно від діаметра отвору або товщини стінки (мал. 1.27, а, б), звичайно ухвалюють Я = (4н-6) D або Я Ss 2,5t. Товщину етенки виступу призначають залежно від товщини стінки виливка t
= (14-1,5) t. Якщо отвір механічно обробляють і воно базове, то діаметр виступу ухвалюють мінімальним. Якщо отвір не базовий, то діаметр виступу призначають із урахуванням допусків на розмір від бази до центру виступу. Якщо отвір розташовується на торці стінки, то форму виступу конструюють так, як показано на мал. 1.28. Розмір Я = 2,25D, З — 0,5 В, А = 1,5 В. Виступи слід розташовувати на зовнішніх поверхнях виливків, щоб не ускладнювати конструкцію прес-форми
Литі заплічка для виходу інструмента часто позитивно впливають на розподіл напруг. Їх важко одержати механічною обробкою звичайним різальним інструментом. Для деяких деталей виконання заплічок обов`язково. Заплічка легше
Рис. 1.27. Виступи різної форми з отворами:.
а — на плоскій стінці; б — у куті стінок; в — на торці в центрі стінки; г — уздовж стінки; д — на зовнішній поверхні отлнвкн: неправильне (/) і правильне (2) розташування виступу
.
обробляти шліфуванням вручну, чому прямі внутрішні кути (див. мал. 1.27, б). Рекомендується ухвалювати b>h 3 мм (див. мал. 1.28).
Технологічні бази й припуски на механічну обробку
Бажане, щоб лита деталь мала одні базові площини для виготовлення й перевірки прес-форм, для виробництва виливків і механічної обробки. Базові поверхні повинні утворюватися мінімальним числом елементів прес-форми, бажане — одним, наприклад, якщо вони розташовані в одній половинці прес-форми
По кожній із трьох просторових осей координат необхідно мати тільки одну головну базову площину, а розміри її повинні бути можливо меншими, отже, і допуск на базовий розмір буде меншим. Якщо неможливо одержати загальну базу для виливка і її механічної обробки, відстань між прийнятими базами потрібно брати мінімальним. У цьому випадку допуск на базовий розмір буде найменшим. Бажане, щоб такі базові поверхні були сторонами однієї стінки, а ще краще — перебували в одній площині. Базову площину необхідно розташовувати в центрі литому деталі. Тоді розміри від бази до самої вилученої поверхні литому деталі, а отже, і допуски на ці розміри будуть найменшими
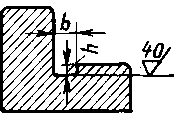
Рис. 1.28. Заплічка на виливках для виходу різального інструменту
Рис. 1.29. Креслення литому деталі:.
.
.
.
Якщо допуски на розміри якої або частини литому деталі по конструктивних або технологічним міркуванням повинні бути мінімальними, те базову площину слід поміщати в цій частині деталі
При відсутності в деталі площини, що задовольняє наведеним вище умовам для вибору бази, рекомендується робити спеціальні технологічні припливи й поверхні їх ухвалювати за бази. Розміри між литою й механічно оброблюваної поверхнями рекомендується проставляти, як правило, тільки в тих випадках, коли обидві поверхні є базовими; розміри до литої небазової поверхні слід проставляти тільки від базової литому поверхні. При проставлянні розмірів ланцюжком замикаючий розмір (товщина виступу, фланця, стінки) може мати значні коливання, що викликають шлюб деталей або необхідність додаткової механічної обробки й додаткового припуску
Припуски, мм, на механічну обробку
Найбільші габаритні розміри виливка, мм | Номінальний розмір виливка до | бази, | ММ | ||||
До. 30 | 30-80 | 80 - 120 | 120- 250 | 250 — 400 | 400-. 500 | 500- 80 Q | |
До 30 | 0,7 | ||||||
30-80 | 0,8 | 0,9 | |||||
80-120 | 0,9 | 1,2 | 1,3 | - | - | - | - |
120-250 | 1,1 | 1,3 | 1,4 | 1,5 | - | - | - |
250-400 | 1,3 | 1,4 | 1,6 | 1,8 | 2,0 | - | - |
400-500 | 1,5 | 1,6 | 1,8 | 2,0 | 2,2 | 2,4 | - |
500-800 | 2,0 | 2,2 | 2,4 | 2,6 | 2,8 | 3,0 | 3,5 |
Примітка. Для виливків, виконуваних з підвищеною точністю, прнпускн на механічну обробку призначають на 10 — 15 % менше, а зі зниженої — на 10-15 % більше зазначених
.
Розміри на кресленнях литому деталі повинні правильно визначати базові площини й відповідати технологічним процесам виливка й механічної обробки
На мал. 1.29 наведене креслення литому деталі, у якої ливарні базові площини перебувають на мінімальних відстанях від базових площин для механічної обробки (базові поверхні 2, 3). Усі основні розміри, що підлягають перевірці у виливку, проставляють від однієї базової [поверхні 4, що є базою для механічної обробки й для контролю виливка (розміри JI
). Проставляти ці розміри ланцюжком ( як Л
) не допускається. Для зменшення допусків на розміри Е, Г, Т и для стінок, оброблюваних з однієї f сторони,
необхідно застосовувати базу
5. Розміри, підлягаючі перевірці, проставляють як розміри Л
Припуск на механічну обробку визначають розрахунковим шляхом. Він складається із двох величин: мінімально припустимого припуску Я и допуску на розмір виливка D від бази механічної обробки до оброблюваної поверхні. Мінімальний припуск Я на механічну обробку, необхідний при розрахунках числа переходів, режимів різання й інших параметрів, установлює технолог-механік
Припуск, який треба виконати на моделі, складається з мінімального припуску з додаванням до нього мінусової частини допуску на розмір від бази механічної обробки до оброблюваної поверхні. Крім того, потрібно враховувати формувальні ухили (див. мал. 1.28).
Середні значення припусків на механічну обробку виливків, виготовлених по виплавлюваних моделях, наведені в табл. 1.3.