Рис. 4.1. Прес-форма з вертикальною пласко* стью рознімання зі стандартних деталей
.
окремими конструктивними єле-ментами. Прес-форми встановлюють на обертових столах із приводом і централізованим підведенням і відводом води для охолодження. Прес-форма — складний дорогий інструмент, що полягає з безлічі елементів, основними з яких є: матриці й обойми (рухливі й нерухливі), стрижні й обладнання для їхнього витягу (копіри пальцеві, диски, похилі штирі), пристосування випередження виштовхування моделей, штовхальники й контртолкатели, різноманітні плити й елементи для охолодження прес-форм
У прес-формах останніх конструкцій передбачені обладнання для регулювання тиску модельної сполуки за допомогою механізму, що відтинає. Специфічні елементи мають прес-форми для виготовлення моделей з пінопластів, наприклад пено-полістиролу
У прес-формах складної конструкції використовують додаткові частини: пристосування повернення виталкивателей, що перетинаються стрижнями; рейкові пристосування для витягу стрижнів і др.
Многогнездние прес-форми з вертикальною площиною рознімання
У масовому виробництві прес-форми цього типу найбільше перед* шанобливі, що пояснюється більш простим розв`язком автоматизації їх складання й розбирання И виключенням ручної операції знімання готових ланок моделей
Розроблені стандарти ( ДЕРЖСТАНДАРТ 19947-74 — ДЕРЖСТАНДАРТ 19999-74) на прес-форми для виплавлюваних моделей, установлювані на автомати для виготовлення модельних ланок. На мал. 4.1 показана конструкція прес-форми зі стандартних деталей
У ході освоєння прес-форм виявлені нові вимоги до їхніх конструкцій, особливо в умовах масового виробництва. Це привело до використання на заводах деяких відмінних від прийнятих у стандартах нових конструктивних розв`язків. Наприклад, застосований зворотний клапан, що відтинає модельна сполука в прес-формі (мал. 4.2), що дозволяє підтримувати оптимальний тиск у затвердевающих моделях і цим стабілізувати їх розміри
Голівка шприца 4 торцем упирається в штангу 3, яка повертає важіль 2 проти годинникової стрілки- Другий кінець важеля тол-
f.
Рис. 4.3. Пастоперекриватель Рис. 4.4. Пристосування випередження виштовхування моделей

кает заслінку нагору до сполучення отвору заслінки з каналом 5 ливникової втулки, установленої в рухливій матриці 6 прес-форми. Модельна маса запресовується в прес-форму. При відході голівки шприца від прес-форми штанга 3 вертається у вихідне положення під дією пружини 1. Важіль 2 повертає заслінку 9 у первісне положення, і заслінка перекриває отвір каналу. При розкритті прес-форми заслінка 9 по скосу штанги 10 піднімається, відкриваючи канал 5.
Надлишковий тиск замішаного до модельного складу повітря до витягу моделі із прес-форми скидається завдяки неповному перекриттю каналу 5 у втулці заслінкою 9. Через утворену в такий спосіб щілина віддаляється повітря, при цьому модельна сполука із прес-форми не випливає. Величину щілини регулюють обертанням ковпака 7, який пересуває обмежник 8 ізаслінку 9. Для фіксування положення ковпака на корпусі нанесені розподіли, а на ковпаку 7 є стрілець-покажчик
У ПО ЗИЛ в одноланкових прес-формах застосовують пастоперекриватель простий конструкції, без регулювання тиску повітря (мал. 4.3). Модельна сполуку запресовують Через канал рухливої втулки 3, яка під дією голівки шприца переміщається до упору в плиту 4. Рухомий стрижень 2 відходить вправо, стискаючи пружину 1 і відкриваючи канали в плиті 5, по яких модельна сполука надходить у порожнину прес-форми. Після відводу голівки шприца деталі 2 і 3 вертаються пружиною у вихідне положення
Для запобігання ушкодження ланок моделей про штовхальники при падінні із прес-форми в бак з водою, у ПО ЗИЛ застосований простий і надійний механізм. При розкритті прес-форми (мал. 4.4) рухлива матриця 1 відходить від нерухливої 2. Штовхальники, упираючись у плити 7 виталкивателей, переміщають їх, а разом з ними переміщають плити 3. Пройшовши хід l
, що забезпечує виштовхування ланки з нерухливої матриці, важіль 6 упираючись одним кінцем в упор 4, обертається навколо Ьси 5 і іншим кінцем повідомляє випереджальний додатковий рух плитам 3, висуваючи їх на хід /
. На це ж відстань центральна втулка, що виштовхує, відкидає ланку моделей від штовхальників
Для збільшення продуктивності в ПО ЗИЛ застосовують двосекційні прес-форми (мал. 4.5). При малих розмірах ланок і їх компактному розміщенні модельна сполуку запресовують через єдиний канал з пастоперекривателем. Запобігання їм витікання модельної сполуки із прес-форми сприяє підтримці тиску під час затвердіння моделей і зменшенню усадочних дефектів у них. Модельна сполука подається до ланок через загальний канал перетином 4X2 мм. У двухзвеньевой прес-формі обоє механізму колективного переміщення стрижнів можуть мати або один загальний привод, або два
автономних привода — по одному на кожний механізм. У першому випадку дискові копіри обох механізмів з`єднані між собою зубчастим зачепленням
Рис. 4.5. Двосекційна прес-форма:.
1 — рим-болт; 2 — напрямні стовпчики постаменту; 3 — штуцер для підведення води; 4 — Плити штовхальників центральних втулок секцій; 5 — висувний стрижень; б — фіксатор висувного стержия; 7 — система охолодження; 8 — втулка підведення модельної маси; 9 — рухлива матриця; 10 — напрямний стовпчик; 11 — нерухлива матриця; 12 — опорні плнти; 13 — штовхальник центральної втулки секції; 14 — штовхальники живильників; 15 — штовхальники моделей; 16 — плнти штовхальників моделей
Рис. 4.6. Пневматична прес-форма з видаленням стрижнів похилими пальцями
.
і обертаються в протилежних напрямках. Другий варіант переважніше, тому що стандартизовані приводи несуть менше навантаження
Многогнездние прес-форми з горизонтальною площиною рознімання. Прес-форми цього типу порівняно рідко застосовують на автоматах для виготовлення виплавлюваних моделей. Механізація складання й розбирання таких прес-форм здійснюється різними способами. На мал. 4.6 показано один з них
Прес-форму встановлюють на спеціальному постаменті, на якому змонтований пневмоцилиндр. За допомогою рукоятки шток пневмоцилиндра піднімає або опускає плиту із закріпленими на ній двома штоками 3. Після запресовування й остигання модельної сполуки штоки 3 піднімають верхню матрицю — кришку 1, у якій
установлені похилі пальці 2. Останніми висуваються стрижні 4. Стрижні 8 видаляють також похилими пальцями 2, які надають руху повзунам 12, а ті, у свою чергу, повзуни 7, із вмонтованими в них стрижнями (вузол 1). При подальшому підйомі штоків 3 тяги 6, які укріплені в кришці прес-форми (перетин Б-Б), підхоплюють плиту 10 зі штовхальниками 11 і виштовхують ланки моделей. У прес-формі застосоване охолодження водою, що проходить по трубках 5. Для безпеки роботи в прес-формі передбачене спеціальне фіксуюче обладнання 9, що втримує рухливі частини прес-форми у верхньому положенні при видаленні ланок моделей
Недоліком прес-форм розглянутої конструкції є незручність очищення й змазування робочих порожнин, розташованих у кришці прес-форми
Зазначеного недоліку немає в прес-формах із кришкою, що відкидається (мал. 4.7). Схема її роботи наступна. Після запресовування модельної сполуки через втулку 8 з пастоперекривателем і охолодження моделей 10 приступають до розкриття прес-форми. Для цього поворотом рукоятки 17 впускають стиснене повітря в циліндр 2. При русі поршня 1 уліво за допомогою з`єднаної зі штоком рейки 14 обертається зубчастий валик 15. У свою чергу, валик входить у зачеплення з рейкою стрижня 16, який при русі нагору піднімає плиту 13, з`єднану із кришкою 9 прес-форми за допомогою стійок 4. Для рівномірного знімання кришки в плиті 13 укріплені штовхальники 3. При подальшому русі плита 13 упирається в плиту 12, у якій укріплені знімачі 11 моделей. У кришці прес-форми жорстко закріплені зубчасті колеса 6, які входять у зачеплення з рейкою 7, відкидають кришку навколо осі 5, даючи можливість зняти виштовхнуте із прес-форми ланка моделей
Рис. 4.8. Прес-форма з ручним обслуговуванням:.
1 — підстава; 2 — плита підтискна; 3 — плнта піднімальна; 4 — стійки; S — стовпчик; 6 — рама; 7 — контртолкатель; 8 — трубчастий штовхальник; 9 — плита стрижнів; 10 — стовпчик напрямна; 11 — вузол підйому піднімальної плнти сфиксатором.
.
Після прочищення отвору для шприцевания й змазування порожнини прес-форми поршень вертається в крайнє положення, потім відбувається складання прес-форми
У випадку, коли при крупносерийном, а іноді й масовому виробництві, автомати не використовуються, застосування прес-форм із горизонтальною поверхнею рознімання полегшує складання й розбирання їх оператором вручну (мал. 4.8).
Складні одногнездние прес-форми. Найбільш продуктивний метод виготовлення ланок моделей у многогнездной прес-формі застосуємо для відносно простих і невеликих моделей. Є деталі більших розмірів або моделі дуже складної конфігурації, які можна виготовити тільки в одногнездних прес-
Рис. 4.9. Комбінована прес-форма для ротора із вставними вкладишами
.
формах. Високі вимоги, пропоновані до таких деталей, обумовлюють виготовлення прес-форми механічною обробкою
До фасонних деталей, що мають складні обриси й глибокі внутрішні криволінійні порожнини, відносять, наприклад, окремі лопатки турбін і пакети лопаток, турбінні колеса, деталі соплових апаратів
У деяких випадках конфігурація деталі настільки складна, що одержати виплавлювану модель в одній прес-формі взагалі неможливо. Тоді виготовляють кілька прес-форм. Модель одержують вроздріб і потім збирають за допомогою пайки. При такому процесі виготовлення моделей спрощується конструкція прес-форм і знижується їхня вартість, але він трудомісткий і не забезпечує необхідної точності. Для досягнення високої технологічності, підвищення точності моделей, а часто — для одержання порожнин, які неможливо виконати, що извлекаемими нз моделі металевими стрижнями, застосовують установлювані в прес-форму перед запресовуванням модельної сполуки карбамідні або керамічні стрижні
На мал. 4.9 показана прес-форма, що полягає з матриці 1 і кришки 2, між якими поміщений кільцевий бандаж 3. Ці три частини закріплюють обоймою 4 за допомогою гвинтів 5 і 6. У прес-форму проставляють стрижні з карбаміду або кераміки 7, потім прес-форму збирають і в неї запресовують модельна сполука 8. Стрижні виготовляють в іншій прес-формі (мал. 4.10), що полягає із двох корпусів 1 я 2, у яких закріплені вкладиші 3 я 4. Фіксують корпуса штирями 5 і закріплюють гвинтами 6 з гайкою 7. Карбамід або керамічну масу заливають через отвір у кришці 9
на яку встановлена склянка
Рис. 4.10. Прес-формі для виготовлення стрижнів
.
Якщо конфігурація моделі дозволяє використовувати одну прес-форму для одержання всіх неметалічних стрижнів, то слід застосовувати саме такий спосіб, тому що він забезпечує найбільшу точність виливка. На мал. 4.11 показані прес-форма > для изгото-вления ротора, у якій контури лопатки оформляються однаковими розчинними (карбамідними) стрижнями, одержуваними в одній прес-формі, і готова модель ротора після розчинення у воді карбамідних стрижнів
Прес-форми для одержання моделей з пінополістиролу. Прес* форми можуть бути одномісними, багатомісними й ланковими. Вони мають специфічні особливості й тому традиційні прес* форми для одержання виплавлюваних моделей, при використанні пінополістиролу повинні бути перероблені
Типова прес-форма для моделей з пінополістиролу показана На мал. 4.12. Конструкція прес-форми повинна забезпечувати швидке ( за 0,2—0,8 с) і рівномірне заповнення полістиролом, що спінюється, видалення газів л мінімальна витрата пенополисти
Рис. 4.12. Прес-форма для моделей з пінополістиролу
рола на літники. У прес-формах повинне бути передбачене обладнання для підігріву ( до 35—40 °С) у вигляді каналів з гарячою водою або електропідігрівачі для попередження тріщин у моделях. При високій продуктивності слід мати також систему охолодження
При розрахунках розмірів порожнини прес-форми необхідно враховувати усадку моделей на 25-30 % меншу, чому у воскоподобних матеріалів. Особлива увага при проектуванні прес-форм потрібно приділяти ливниковим системам, що підводять пінополістирол. Літники повинні бути як можна коротше, а живильники у вигляді крапки або щілини (мал. 4.13). Пінополістирол краще впорскувати в порожнині, що формують тонкі стінки моделі
В одномісних прес-формах рекомендується застосовувати живильник, показаний на мал. 4.13, а, у багатомісних живильник, показаний
Рис. 4.13* Живильники:.
U й — крапковий при безливниковому литті в одномісні прес-форми; б — щілинні з ливниковим каналом; в — крапковий з ливниковим каналом; 1 — ливникова втулка; 2 — крапковий літник; 3 — порожнина прес-форми; 4 — ливниковий канал; 5 — щілинний живильник
Рис. 4.15. Вентиляційна система в прес-формі:.
1 — порожнина втулкн ланки; 2 — ливникова втулка; 3 — напівформи; 4 — гиездо прес-форми; 5 — втулка; 6 — стрижень
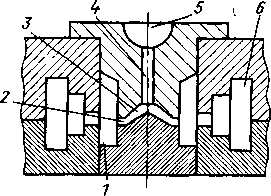
Рис. 4.14. Ливникова система для модельних ланок:.
1 — порожнина втулки ланки; 2 — живильник; 3 — колектор з рассекателем; 4 — літник; 5 — ливникова втулка; 6 — гніздо прес-форми
на мал. 4.13, в. Щілинний живильник (мал. 4.13,6) ефективний у тому випадку, коли напрямок упорскування матеріалу в прес-форму не збігається с напрямком протяжних порожнин. Розміри елементів живильників наведені в табл. 4.2.
При виготовленні модельних ланок застосовують ливникову систему, що підводить пінополістирол в усі гнізда прес-форми (мал. 4.14).
Для швидкого відводу газів рекомендується передбачати вентиляційні канали по поверхні рознімання, у глухих місцях (оформлювані гвинтами), у вигляді зазорів на хвостовиках стрижнів. Можна використовувати металокерамічні мікропористі вкладиші або гвинти з отворами діаметром 0,3-0,4 мм.
Одне з розв`язків видалення газів з порожнини прес-форми, що утворює втулку ланки, показане на мал. 4.15. D
на 0,15- 0,2 мм; D
< D на 5-6 мм. гази, що виділяються, містять в основному легкозаймисті пари изопентана, тому їх не можна виводити в місця розташування електронагрівників
Штовхальники моделей повинні бути широкими, установлювати їх випливає в тонких частинах моделі, що мають більшу щільність і твердість. Система штовхальників повинна забезпечувати механізоване відділення ливникових систем від моделей
.
Таблиця 4.2.
Рекомендовані розміри крапкових н щілинних живильників
Об`єм моделі, | Крапкові | Щілинні | ||||
D, мм | Площа | Площа | В, мм | |||
см® | L, мм | перетину,. мм 2 | не більш | сечеиия,. мм* | ||
До 5 | 0,5-0,8 | 1,5 | 0,2-0,5 | 1,5 | 3-4 | 1,0-1,5 |
ЙМ5. 1530 | 0,5-0,8 | 2,0 | 0,2-0,5 | 2,0 | 4-5 | 1,2-1,5 |
0,8-1,0 | 2,0 | 0,5-0,8 | 2,0 | 5-6 | 1,6-2,0 | |
30-50 | 1,0-1,5 | 2,5 | 0,8-1,8 | 2,5 | 6-8 | 1,6-2,0 |
50-75 | 1,5-2,0 | 2,5 | 1,8-3,1 | 2,5 | 6—8 | 2,0—2,5 |
75—100 | 1,5—2,0 | 2,5 | 1,8—3,1 | 2,5 | 6—10 | 2,5—3,0 |
Виготовлення прес-форм із гіпсу найбільш швидкий і економічний спосіб, застосовний для виготовлення серійних ( до 50 шт. з однієї прес-форми) моделей, від яких не потрібно високої точності й малої шорсткості поверхні
Прес-форми виготовляють заливанням водної суспензії гіпсу на еталон, який може бути виконаний практично з будь-якого матеріалу — від пластиліну до металу. Найчастіше застосовують дерев`яні еталони, пофарбовані модельним лаком. При затвердінні гіпс має малу усадку
Процес виготовлення гіпсової прес-форми (мал. 4.16) полягає в наступному. Еталон 7 з дерева, виготовлений з урахуванням ливарної усадки, може бути рознімним або цільним. Його встановлюють на постамент 9, що оформляє контур поверхні рознімання прес-форми. Для спрощення можна еталон заформовать в опоці з піщаною сумішшю, у пластиліні або залити модельною сполукою з наступним доведенням по поверхні рознімання
В еталон вставляють металеві деталі, які оформляють найбільш відповідальні елементи моделі або ж вставки й стрижні (1, 5 і 4), одержання яких з гіпсу важко. Постамент 9 оточується обичайкою 6, висота якої дорівнює висоті майбутньої прес-форми. Площина рознімання змазують тонким шаром мила або масла. Для запобігання прес-форми від руйнування извлека-
Рис. 4.16. Схема виготовлення гипсо&ой прес-форми
емими стрижнями 3 і 4 на них надягають металеві втулки 2 і 5. Після нанесення розділового мастильного матеріалу в обичайку заливають гіпсову суспензію (мал. 4.16, а). Затверділу напівформу 8 повертають на 180° і встановлюють на металличе
ские стрижні втулки. Після змазування поверхні рознімання й еталона розділовою сполукою заливають другу напівформу й дають гіпсу затвердіти (мал. 4.16, б). В одній з напівформ просвердлюють канал для модельної сполуки 11. Еталон извлекается із прес-форми (мал. 4.16, в).
Як правило, гіпсові прес-форми скріплюють за допомогою універсальних пристосувань або струбцин. Для запобігання гіпсу від руйнування шприцом 10 на прес-форму накладають металеву плиту 12 сотверстием.
Прес-форми можна виготовляти з будівельного гіпсу, але краще застосовувати високоміцний гіпс марок 350 і вище. При хра* нении в сирому приміщенні гіпс втрачає властивість схоплюватися, тому перед використанням його слід просушити й просіяти через сито. На 7 травні. ч. сухого гіпсу беруть 3—4 травні. ч. води. Більш рідка гіпсова суміш після затвердіння має меншу міцність, а густа — утрудняє заливання. Перемішують воду з гіпсом доти, поки в суміші не зникнуть сухі грудки й не буде вилучена основна маса повітряних міхурів. Останні прилипають до поверхні еталона, утворюючи в затверділій формі раковини. Щоб уникнути цього можна попередньо кистю наносити шар гіпсу на модель, а потім заливати іншу суміш
В окремих випадках, наприклад при виготовленні великої кількості суміші, потрібно тривалий час для її перемішування. Щоб попередити загустение суміші, у неї додають сповільнювач твердіння; розчин у воді столярного клею, бури або борної кислоти. Кількість сповільнювачів підбирають дослідним шляхом. Клейового сповільнювача додають 0,1—0,2 % маси води, бури 0,35-0,50 і борної кислоти 1,5—2,0 % маси сухого гіпсу
Для підвищення міцності гіпсові прес-форми можна армувати металевими каркасами, додавати в гіпс 15—30 % цементу або замішувати гіпс на водяному розчині сполучного МФ-17.
Для додання порожнини гіпсової прес-форми гладкої поверхні, а також підвищення поверхневої міцності й негигроско-пичности, просушену прес-форму просочують протягом 30— 60 хв в оліфі, нагрітої до 50 °С. Після цього прес-форму протирають, просушують на повітрі й красять спиртовим лаком або нітролаком. Поверхня прес-форми можна упрочнить нанесенням на неї шару органічного скла, розчиненого в дихлорєтане (60 г оргскла на 1 л дихлорєтана). Роботу слід проводити під витяжкою, так. як пари дихлорєтана токсичні. Після про-суцпси протягом 2—3 год при 40—50 °С товщина шару органічного скла становить 50—60 мкм.
Гарні результати дає застосування незабарвлених гіпсових прес-форм, які перед запресовуванням опускають на 2—3 хв у холодну воду. Така прес-форма не вимагає ніякого змазування
Литі металеві прес-форми мають найбільше поширення, тому що вони більш дешеві й можуть бути швидше виготовлені, чому механічною обробкою. Виготовлення моделі-еталона, по якому відливають прес-форму, завжди менш трудомістко, чому виготовлення самої прес-форми механічною обробкою. Лиття многогнездних прес-форм по одній моделі-еталону, як правило, забезпечує менший розкид розмірів, чому при одержанні такої прес-форми механічною обробкою. Особливо зручні литі прес-форми при освоєнні нової номенклатури виливків і виготовленні перших зразків. У цьому випадку необхідні конструктивні зміни можуть бути швидко здійснені на моделі-еталоні, а потім перенесені на відповідну прес-форму, відлиту по цій моделі
Процеси одержання литих металевих і гіпсових прес-форм аналогічні, але для виготовлення металевої форми потрібен металевий еталон. У металевій прес-формі можна одержати велику кількість моделей, тому в її конструкції передбачають пристосування, що забезпечують зручність роботи, що й подовжують строк її служби. Такими пристосуваннями служать рознімний корпус, точно пригнані штирі з напрямними втулками, пристосування для виштовхування моделей із прес-форми й при необхідності для комбінованих прес-форм — різні металеві вставки
Корпус прес-форми звичайно виготовляють звареним з листової сталі або ж відливають із алюмінію, штирі, втулки й штовхальники виготовляють зі стали
Для попередження приварювання сплаву, що заливається, до еталона, поверхню останнього натирають лускатим (сріблистим) графітом, або покривають фарбою з пилоподібним кварцом на рідкому склі або єтилсиликатном сполучному. Гарні результати дає копчення поверхні еталона
У табл. 4.3 наведені сполуки й властивості легкоплавких сплавів. Сплав Вуда можна застосовувати при виготовленні прес-форм по металевих і дерев`яних еталонах. Низька температура плавлення й відсутність усадки є основними перевагами сплаву. До його недоліків ставляться порівняно мала міцність і висока вартість. Вісмутові сплави мають більш високі міцність і температуру плавлення, вони не мають усадки, а іноді об`єм їх при охолодженні збільшується. Цинковий сплав при відносно невисокій температурі плавлення має значну міцність і зносостійкістю, його можна заливати вільним заливанням на підігрітий еталон
Рекомендується верхню й нижню частини прес-форм відливати з різних сплавів, з різною температурою плавлення. Найбільш оптимальним матеріалом уважають сплав, що містить 80 % РЬ, 6 % Sn, 14 % Sb з температурою плавлення 250 °С, твердістю НВ 15,4 і усадкою 0,5 %. Для іншої частини прес-форми застосовують
Сполуки й физико-мехаиические властивості легкоплавких сплавів для виготовлення прес-форм
Сполука | % | ||||||
Сплав | Pb | Sn | Bi | Sb | А1 | Zn | Інші елементи |
Вуда | 25 | 12,5 | 50 | 12,5 Cd | |||
Bi-Pb | 44,5 | - | 55,5 | - | - | - | - |
Bi-Sn | - | 42 | 58 | - | - | - | - |
Sn-Bi-Pb | 30 | 35 | 35 | — | — | — | — |
Pb-Sn-Bi | 70 | 15 | 15 | — | — | — | — |
Pb-Sb | 87 | — | — | 13 | — | — | — |
Pb-Sn-Sb | 56 | 33 | — | И | — | — | — |
ЦАМ 4—1 | - | — | — | — | 4 | 95—96 | 0,75—1,25 Си 0,08—0,1 Mg |
ЧЕРВОНИЙ2 | -- | 87—90 | - | 10—13 Si |
Фнзнко-Механнческне властивості
Сплав | ПЛ’ ° c | B, Мпа | HB | Об`ємна маса, кг/м а |
Вуда | 68 | 41,2 | 9,2 | 9 400 |
Bi-Pb | 124 | 44,1 | 10,2 | 10 500 |
Bi-Sn | 138 | 54,9 | 22 | 8 700 |
Sn-Bi-Pb | 140 | — | — | 9 100 |
Pb-Sn-Bi | 140 | — | — | 10 100 |
Pb-Sb | 247 | 49 | 30 | 10 500 |
Pb-Sn-Sb | 315 | 54,9 | — | 9 100 |
ЦАМ 4—1 | 430 | 235—274 | 70—85 | 7 100 |
ЧЕРВОНИЙ2 | 600 | 147—157 | 50—60 | 2 700 |
сплав з 30,6 % РЬ, 51,2 % Sn і 18,2 % Cri з температурою плавлення 142 °С, твердістю НВ 9,6 і усадкою 0,35 %. Із цинкових сплавів оптимальними є сполука 3,5—4 % А1, 2,4 % Сг, 0,02—0,05 % Mg, решта цинк із температурою заливання 410—430 °С, лінійною усадкою 0,85 % і сполука 3,5—4,3 % А1, 0,05—0,06 % Сг, 0,02-.
0,05 % Mg, решта цинк, з температурою заливання 410—420 °С и лінійною усадкою 0,95 %.
Чіткі контури одержують при нагріванні металевого еталона до температури наг 30—60 °С нижче температури плавлення легкоплавкого сплаву й при перегріві сплаву на 30—60 °С вище температури його плавлення
У тому випадку, коли до прес-форми висувають підвищені вимоги по точності розмірів і чистоті поверхні, застосовують обпресування її по еталону на пресі, використовуючи високі цласти-чесйше властивості застосовуваних сплавів на основі РЬ і Sn. Затверділу прес-форму розбирають, виправляють дрібні дефекти на її робочій поверхні (шабруванням) і знову збирають разом з еталоном для обтиснення на пресі під тиском до 60 Мпа.
Є досвід виготовлення лйткх прес-форм йз сплаву ЧЕРВОНИЙ2 йа машині лиття під тиском з холодною горизонтальною камерою пресування [41]. При цьому використовують звичайні блок-форми із циліндричними й прямокутними вкладишами, додатково виготовляють тільки вкладиші в блок-форми для закріплення єта-лонов-моделей.