Формування холодних оболонок сипучим наповнювачем. На дно
опоки, що представляє собою коробці, насипають невеликий шар наповнювача, щоб верхній рівень торця ливникової вороньи оболонки був приблизно на рівні верху опоки; ставлять оболонки, лійки закривають кришками й насипають наповнювач. У нього можуть бути введені сполучні, наприклад борна кислота (табл. 6.23). Опоку ставлять на вибростол з амплітудою коливань 0,5—0,6 мм і частотою коливань близько 1400 у хвилину. Після ущільнення наповнювача знімають кришки й форми направляють для прожарювання впечь.
Оболонки прожарюють 7—10 год і заливають їхніми гарячими, при литті стали вони мають температуру 800—900 °С; з моменту витягу форм із печі й до їхнього заливання впаковані оболонки не встигають прохолоджуватися. При використанні опорного наповнювача оболонки нагрівають поступово й заливають гарячими. Однак процес прожарювання заформованних оболонок тривалий, вимагає значних витрат енергії й великої витрати жаростійких опок. При цьому до оболонки, просоченої модельних сполукою, утруднений доступ кисню повітря, необхідний для випалювання залишків модельної сполуки. У якості наповнювача найчастіше застосовують звичайний кварцовий пісок (кристалічний кварц) як один з доступних матеріалів. Однак це нерідко приводить до викривлення розмірів оболонок і, отже, виливків, тому що зовнішні шари, що примикають до опоки, піску нагріваються до температури поліморфного °превращенйя (573 С) і розширюються раніше, чим прилягаючі до оболонки шари піску й сама оболонка. пісок, що розширюється, обмежений стінками опоки, розширення якої невелике, давить на оболонку, що може викликати її деформацію або руйнування. При подальшому нагріванні оболонки до температури поліморфного перетворення кварцу, її розширенню в цей період перешкоджає наповнювач, виявляючи на оболонку значний тиск. У результаті наповните стискає оболонку, у ній утворюються тріщини. Тиск може викликати навіть деформацію (витріщання) опоки, або утвір у ній тріщин
Отже, кращим варіантом є прожарювання оболонок і заливання їх без опорного наповнювача. Якщо це неможливо, то раціонально прожарювати оболонку без наповнювача, а потім заливати в контейнерах, що обігріваються (також без опорного наповнювача), або впаковувати перед заливанням у гарячий опорний наповнювач. При цьому слід застосовувати оболонкові й наполнительние матеріали, що не мають поліморфних перетворень, наприклад НК.З, шамот, електрокорунд
Формування прожарених гарячих оболонок. У серійному виробництві доцільно використовувати установки із псевдоожиженним шаром і розташовувати їх біля печі прожарювання. Відрізняються вони
Таблиця 6.24.
опорні наповнювачі, Що Твердіють,
Складові | Кількість, % по масі | Складові | Кількість, % по масі |
1. Цемент глиноземистий | 12-15 | . 2. Пульвербакелит (смо | 1,0-1,5 |
марки 500 | ла № 104) | ||
Пісок кварцовий 1 ДО020 | 88-85 | Пісок 1 ДО020 | 99-98,5 |
Вода | 30-40 | Смачиватель піску | 0,5-0,6 |
( понад 100) | ( понад 100) |
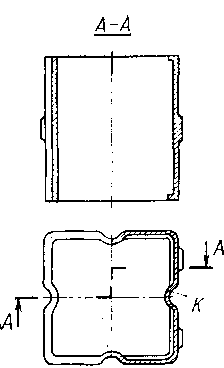
Рис. 6.27. Нероз`ємна опока з жаростійкої сталі з компенсатором теплового розширення УВОДИТИ, УВЕСТИ ДО ЛАДУ.
.
тим, що пісок приводять у псевдоожи-женное стан, включаючи подачу гарячого повітря за допомогою ножної педалі тільки в момент занурення в нього оболонки, а після осідання піску в оболонку заливають розплав і далі в цій же установці виливка остигають до наступної плавки
Формування опорним наповнювачем, що твердіє. Зразкові сполуки сумішей наведено в табл. 6.24. Суміш 1 готовлять у лопатевому змішувачі, наливають воду, насипають цемент і перемішують 2— Змин; не припиняючи перемішування, насипають пісок і перемішують ще 6—7 хв. На стіл вібратора ставлять стругану подопочную плиту, на яку встановлюють блок моделі з оболонкою, приклеюють його модельною сполукою й установлюють опоку без дна з жаростійкої стали
.
Внутрішню поверхню опоки обкладають картоном для обра-зовани зазору між опокою й наповнювачем (мал. 6.27). Наливають наповнювач, включають вибромашину з амплітудою 0,3—0,4 мм при частоті вібрації 1600—1500 коливань у хвилину й у міру осідання суміші її додають совком. Стіл вибромашини має приймач для стекания води. Тривалість вібрування 10— 15 хв, після чого форми знімають зі стола й установлюють на стелажі для повільного сушіння
У способі, запропонованому М. Г. Оком і Н. М. Черняком, використовують переваги сухого сипучого наповнювача, при цьому застосовують суміш 2 (див. табл. 6.24). Внаслідок переходу пульвер-бакеліту зі стану А в стан Із при нагріванні форм для виплавления моделей суміш здобуває високу міцність, а в процесі покаливания вона, внаслідок деструкції сполучного, стає неміцною й не перешкоджає- усадці виливків. Формовать блоки можна тільки в опоках сдном.
6.8. ПРОЖАРЮВАННЯ ОБОЛОНКОВИХ ФОРМ
При прожарюванні вирішуються три завдання: видалення газотворних складових, підвищення міцності, нагрівши оболонки для кращого заповнення порожнин металевим розплавом. Прожарюють оболонки в окисному середовищі нагріванням до 800—1100 °С с наступною витримкою. При цьому протікають процеси: нагрівання оболонки; видалення з неї газотворних складових, джерелом яких є волога; видалення залишків модельної сполуки й продуктів
деструкції сЁЯзующегб; гидролитическая поліконденсація сполучного; утвір кристалічних структур сполучного; термічне розширення оболонки й поліморфні перетворення; утвір капілярних каналів
Передача теплоти оболонці й переміщення теплоти в товщі останньої — головні процеси; усі інші — наслідок їх. Відзначимо, що оболонкова форма має низку ефективною теплопровідністю й вона збільшується зі збільшенням температури. Наприклад, теплопровідність кварцової оболонки 0,29 Вт/( м-м-°З) при 600 °С,.
0,35 Вт/(м • °З) при 1100°С, 0,56 Вт/( м-м-°З) при 1500 °З.
Оболонкові форми, як правило, заливають гарячими й тому не можна відривати прожарювання їх від заливання. Температура форми повинна бути при заливанні сплавів: на основі заліза 800—900 °С, на основі нікелю 900—1100 °С, на основі міді 600—700 °С, на основі алюмінію й магнію 200—250 °С. При заливанні сплавів на основі міді, алюмінію й магнію оболонки після прожарювання прохолоджуються
Головні джерела газів: модельна сполука (табл. 6.25), що вбралася в оболонку, і продукти деструкції сполучного [85, 86]. Процес їх видалення складається із двох стадій: газифікації й спалювання продуктів деструкції; випалювання вуглецю, що відклався в капілярах оболонки. Колір зламу повністю прожареної оболонки білий або. рожевий. Колір зламу від чорного до сірого — ознака того, що в капілярах є вуглець і оболонкова форма недостатньо газопроницаема; отримані виливки уражені газовими раковинами й мають підвищений вміст вуглецю в поверхневому шарі сталевих виливків
.
Таблиця 6.25.
Зміст модельної сполуки н вуглецю в зразках оболонок після виплавления
N. Теплоносій | Кількість модельної сполуки | Зміст вуглецю, % до маси оболонки | |
г/кг оболонки | % до маси оболонки | ||
Вода, 97—99 °С | 38 | 3,8 | 3,0—3,2 |
Модельна сполука, 125—130 °С | 70 | 7,0 | 5,8-6,0 |
Повітря (потік), 170—180 °С | 51 | 5,1 | 4,2-4,4 |
Відзначимо, що надмірна міцність оболонки може привести до тріщин у виливках внаслідок гальмування їх усадки
До оболонки, що представляє собою капілярно-пористе тіло, Теплота може бути передана випромінюванням (радіацією), конвекцією, теплопровідністю або комбінацією цих процесів. Сполука газів у печі повинен бути окисним, щоб вигоріли всі залишки модельної сполуки й продукти деструкції сполучного, включаючи вуглець. Продукти згоряння слід безупинно видаляти з області нагрівання оболонок. Із цих позицій розглянемо печі для прожарювання оболонкових форм
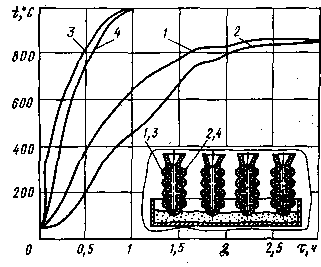
Рис. 6.28. Термограмми иагреваоболочек у прохідній електропечі опору (/ і 2) і прохідної газової печі 4).
.
Електричні печі. У печах опору оболонкові форми одержують теплоту випромінювання від спіралей і кладки печі. При цьому тіньові частини форм безпосередньо не одержують теплоту,, у результаті чого неминуче соi здается температурний градієнт у різних частинах оболонки й уповільнюється процес нагрівання (мал. 6.28). Останній особливо тривалий при прожарюванні оболонок в опорному наповнювачі, маса якого в 8—16 раз більше маси оболонок. В електропечах важко підтримувати надлишок кисню, необхідний для окиснення продуктів деструкції залишків модельної сполуки, що связующего й вуглецю. Електричні печі опору мало придатні для прожарювання оболонок і зовсім непридатні, коли застосовують випалювані моделі; їх заміняють газовими
Газові печі. У печах цього типу також теплота передається, головним чином, від гарячих газів більш холодним оболонкам або опокам. Але на відміну від нагрівання в електричних печах гази обмивають оболонки й опоки, і немає тіньових ділянок (див. мал. 6.28). При цьому в газових печах легко підтримувати необхідна окисна сполука газів. Особливо інтенсивно протікають процеси при 550—600 °С, газифікується й згоряє модельна сполука, і при 80 є-Є—900 °С, вигорає вуглець із оболонки. При прожарюванні в опорному наповнювачі потрібна теплота для нагрівання останнього й утрудняється доступ кисню до оболонки. Це збільшує тривалість прожарювання прймерно в 10 раз у порівнянні із прожарюванням дійсних оболонок
Кращий режим нагрівання в газових печах —■ м`який; він можливий при нижніх (мал. 6.29) топленнях, тому що це забезпечує рециркуляцію газів, що знижує витрата палива на відміну від печей тільки з гострим верхнім нагріванням. Гази при русі з нижніх топлень нагору захоплюють частину газу, що відходить, змішуються з останнім і в такий спосіб здійснюється рециркуляція
При русі газу й продуктів згоряння вниз відбувається пері-дача теплоти оболонкам або опокам, установленим на піддонах. Між днищами піддонів передбачають проміжки 50—60 мм для здійснення рециркуляції й видалення газів, що відходять, через кабанів у димар. Через верхні пальники вдмухують газ із надлишком повітря тільки для горіння модельної сполуки й вуглецю. Обладнання для введення в піч піддонів з оболонками й витягу їх з печі аналогічні застосовуваним у прохідних електропечах. Дверки піднімають і опускають за допомогою редукторів з єлектромо
Рис. 6.2 9. Схема газової прокалочной печі
.
торами, причому електрична схема така, що неможливо відкрити двері А при відкритих дверях Б, щоб у працюючій печі не порушувати рух газів і не створювати неконтрольованого підсмоктування повітря [47].
Печі з високотемпературним псевдоожиженним шаром вогнетриву
Схема такої печі з обладнанням для заливання до охолодження оболонок ( без механічної частини й кришок) наведена на мал. 6.30 [19]. Паливом служить газ, що надходить через трубки 1 у шар електрокорунду 2 із зернами розмірами 0,1—0,12 мм. Газ у суміші з повітрям нагріває електрокорунд і викликає його «кипіння». Оболонкові форми із закритими лійками встановлюють у ґратчасту касету й занурюють у нагрітий до 900—1000 °С псевдокипящий електрокорунд. Оболонка обмивається з усіх боків, що перебувають у зваженому стані зернами гарячого електрокорунду й газами, що містять надлишок кисню, достатній для спалювання залишків меблевої сполуки й продуктів деструкції сполучного
Таким образом, при цьому способі прожарювання нагрівається тільки оболонка, без наповнювача; теплота оболонці передається одночасна випромінюванням (радіацією), конвекцією й теплопровідністю; у газовій суміші підтримується кількість кисню, достатнє для згоряння продуктів деструкції модельної сполуки, що связующего й вуглецю; температура псевдокипящего шару відповідає оптимальної для швидкого протікання реакції газифікації й окиснення органічних залишків воболочке.

Рис. 6.30. Схема установки для прожарювання, заливання й охолодження оболонок у псевдокипя-щем шарі єлектрокоруида:.
/ — прокалнванне; II — затока* ка й охолодження виливків
Внаслідок викладених особливостей тривалість прожарювання шестислойной оболонки становить 6—10 хв. За цей час вигорає практично весь вуглець, що важливо при одержанні виливків, у яких неприпустиме підвищення його змісту. Поруч із піччю прожарювання розташована установка для заливання оболонок у гарячому наповнювачі й створення умов спрямованого затвердіння виливків. Оболонки в касеті переносять і занурюють у псев-доожиженний електрокорунд, потім припиняють подачу газоповітряної суміші, наповнювач осідає й обжимає оболонку. Вона готова до заливання. Після заливання в шар електрокорунду знизу подають стиснене повітря для створення умов спрямованого затвердіння виливків. Якщо неприпустимо обезуглероживание поверхневого шару виливків, повітря заміняють газом, що не містять кисень. Газ перешкоджає вступу кисню повітря до поверхні виливків і служить джерелом пироуглерода, що відкладається воболочке.
Слід зазначити, що прожарювати в псевдоожиженном шарі електрокорунду необхідно оболонки з термостійких матеріалів, що дозволяють нагрівати оболонки без розтріскування з будь-якою швидкістю. Такою властивістю найбільшою мірою має НКС (табл. 6.26). З нього слід також виготовляти захисні ковпачки для запобігання влучення зерен, що витають електрокорунду
Таблиця 6.26.
Режими прожарювання й заливання оболонкових форм (розплав типу стали)
Форма | Основа оболонки | Лінійне розширення при иагреве до 1100°С, % | Тривалість нагрівання при прожарюванні, год | Температурячи оСолочки, °З | |
после. пуття ливания | при заливанні | ||||
Істинно оболонкова | нкс | До 0,04 | 0,1—0,2 | 900—1100 | 20—1000 |
Оболонкова | Білий єлектроко-руид. Суспензія — дистен-силлиманит Обсипання — білий електрокорунд Шамот високоглиноземистий | До 0,4. До 0,4 До 0,4 | 2.5—3. 2.5—3. 3—3,5 | 900—1100. 900—1100. 850—900 | 850—950. 850—950. 800—850 |
Оболонкова в сипучому сухому опорному наповнювачі | Кристалічний кварц | 1,2—1,4 | 5-6 | 900—950 | 850—900 |
Примітки. I. При иагреве оболонок із кристалічного кварцу відбувається стрибкоподібне поліморфне перетворення прн 573 °З.
2. Тільки оболонкові форми із кристалічного кварцу заформовивают в опорний наповнювач, інші прожарюють і заливають без опорного наповнювача
у порожнину оболонкових форм. Можливі два способи виготовлення ковпачків: спіканням з порошків НКС або за технологією одержання оболонкових форм із використанням НКС у якості вогнетривкої основи суспензії й обсипочного матеріалу
Ковпачки повинні герметично закривати внутрішню порожнину ливникової лійки й легко зніматися