.
.
Комплексна механізована й комплексна автоматична лінії виготовлення моделей. На мал. 10.1 наведено один з варіантів плану розташування типового серійного встаткування [31 ] із взаємно вв`язаною продуктивністю, скомпонованого у дві лінії: комплексну механізовану (мод. 652 — 654) і комплексну автоматизовану (мод. 652-653). Перша лінія призначена для виготовлення моделей серійних виливків, друга — моделей виливків масового виробництва [59, 70].
З ванни виплавления моделей 1 повернення модельної сполуки разом з гарячою водою стікає по лоткові в роздільник 2. Якщо моделі з оболонок виплавляють не у воді, а в модельній сполуці, то роздільник може бути вилучений із системи. У роздільнику модельна сполука відділяється від води, яка після очищення зливається в каналізацію, а модельна сполука накопичується в баку, звідки насосом 3 по трубопроводу 4 перекачується в плавильний агрегат 5. Сюди ж подають і свіжі модельні матеріали. У плавильному агрегаті розплавлена модельна сполука відстоюється, додатково очищається від води й сторонніх включень. Далі насосом 6 він подається по трубопроводу 7 у ємнісні баки 8, звідки направляється в пастоприготовительние агрегати 9. У них модельна сполука здобуває пастообразную консистенцію завдяки охолодженню до температури часткової кристалізації й замешиванию повітря
Пастообразний модельна сполука по трубах 10 подають _ під тиском до автоматів И и карусельним установкам 12 виготовлення моделей. Температуру обігрівальних обладнань в
Рис. 10.1. Плаи розташування встаткування для виготовлення моделей
.
усіх ланках ліній підтримують насосно-нагрівальні стан-ции 13. На поворотних столах автоматів 11 установлене по десять прес-форм. Заповнення робочої порожнини прес-форм модельною сполукою, витримка для затвердіння моделі, розкриття прес-форм, виштовхування ланки моделей, очищення ливникового отвору й обдувши робочої порожнини виконуються автоматично по заданому циклу
На карусельних установках 12 механізовані заповнення порожнини прес-форм, розкриття їх і виштовхування моделей. Вилучення ланки моделей, очищення ливникового отвору, обдувши й змазування робочої порожнини прес-форми виконують вручну.
Розглянуті лінії рекомендовані для виготовлення моделей з легкоплавких сполук
Комплексна автоматична лінія готування суспензії (мал. 10.2). Застосування цієї лінії дозволяє розв`язати завдання автоматизації важких і шкідливих для здоров`я операцій готування суспензії й подачі її до місць споживання. Лінія розроблена на Горьковском автозаводі, у ній використані автомат при-
Рис. 10.2. Схема комплексної автоматичної лінії готування суспензії
.
готовления суспензії (мод. 662), машина для разрезки мішків з пилоподібним вогнетривким матеріалом і пекти для його прожарювання констр укции Гипротр акторосель хозмаша.
Мішки розпорює машина 1. Пилоподібна складова суспензії з бункера машини закритим конвеєром 2 передається для сушіння в піч 3, потім надходить в апарат 4 для охолодження, а звідти в полігональне сито 5. З-під сита матеріал передається в бункер 7 автомата за допомогою системи закритих конвеєрів 6 (або в кюбелях). Рідкі складові суспензії із цисцерн 16 подаються насосами 15 по трубах 11 у напірні баки 8, установлені над автоматом. У напірний бак для подкисленной води кислота подається із пляшки 10, а вода з водопроводу. В автоматі 9 вихідні складові суспензії безупинно змішуються, і готова суспензія стікає в бак 12. До місць споживання вона подається під дією стисненого повітря (патрубок 13) по гумових шлангах 14.
На мал. 10.3 наведена схема основного механізму лінії — автомата готування суспензії. З видаткових баків розчинника 1, єтилсиликата 4 і подкисленной води 6, у яких підтримують за допомогою насосів 7 і переливних патрубків 3 постійний рівень, рідкі складові суспензії через клапани 2 по трубопроводах 5 надходять самопливом до дозувальної панелі автомата. Витрата рідин установлюють за допомогою голчастих кранів 8 по ротаметрах 9. Задана кількість рідких складових суспензії безупинно надходить у змішувач 12. Одночасно з рідинними дозаторами включають дозатор пилоподібної складової суспензії, яка з бункера 16 по лоткові 15 попадає на стрічку конвеєра 14. Гайкою 17 регулюють положення заслінки 18, зменшуючи або збільшуючи кількість пилоподібного матеріалу, що надходить безупинно по лоткові 13 у змішувач 12, де всі складові суспензії інтенсивно змішуються крильчатками 11.
.
Рис. 10.3. Схема автомата готування •суспензии.
.
Видача готової суспензії відбувається безупинно через переливний патрубок 10.
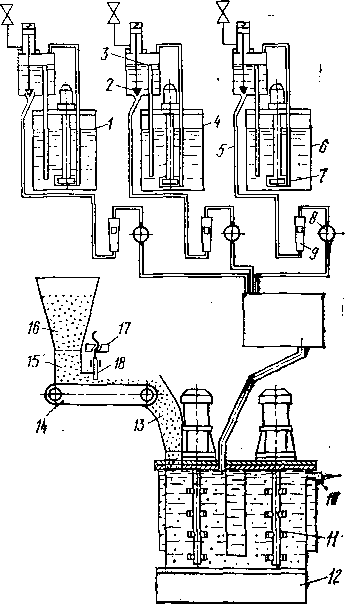
При необхідності одержання окремих порцій (120-.
150 л) може бути встановлений цикличний режим роботи й здійснене відповідне настроювання дозаторів, залежно від того, якої в`язкості й сполуки потрібна суспензія. У системі автоматичної лінії можуть працювати трохи таких автоматів
Автоматична лінія виготовлення оболонок
(мал. 10.4).
На лінії виконуються операції по формуванню оболонок на блоках моделей і виплавлению останніх. Автомати виготовлення оболонки 2 (мод. 6А67), камера сушіння 1 (мод. 6А82) і ванна виплавления моделей 3 (мод. 672) об`єднані в єдину лінію
(мод. 6Б60) конвеєром, який крім транспортних функцій завдяки конструкції підвіски виконує й робочі операції: підйом, опускання й обертання підвісок сблоками.
На ділянці складання конвеєр має спуск до робочих місць навішення модельних блоків. Модельні блоки надходять в автомат № 1, де формується перший шар оболонки, і по конвеєру направляються в камеру сушіння. Пройшовши першу галузі конвеєра блоки, що висохнули, надходять для нанесення другого шару в автомат № 2, потім знову в камеру сушіння і так далі до одержання п`ятишарової оболонки. Після проходження кожного з автоматів нанесення оболонки (№ 1-№ 5) автоматично очищається торець ливникової лійки
Блоки з п`ятьма шарами оболонки транспортуються конвеєром у ванну виплавления моделей. Тут блоки лійкою нагору поринають у гарячу воду або модельну сполуку. При проходженні через, ванну виплавления оболонки втримуються на стояку завдяки спіральній канавці на металевому ковпачку, що формує металлоприемник. Підвіски конвеєра з виплавленими оболонками при виході з ванни, наїжджають на копір і, обкатуючи
Рнс. 10.4. Схема автоматичної лінії виготовлення оболонок
.
його, піднімаються, одержуючи обертання навколо поздовжньої осі. При обертанні з оболонки виливаються вода й модельна сполука. Після виплавления моделей оболонки знімають із конвеєра. Звільнені стояки проходять мийку- і вертаються на ділянку виготовлення модельних блоків
Автомат виготовлення оболонок (мал. 10.5). Автомат складається із трьох вузлів: пескоеипа з «киплячим шаром», ванни із суспензією м бака зберігання й подачі суспензії. Блоки 1 по конвеєру 3 посту-
Рис. 10.5. Схема автомата виготовлення оболонок
.
пают до ванни 8 із суспензією. Підвіска конвеєра 4, на якій укріплений блок, обкатуючи копір 5, піднімається, переходить через край ванни й, рухаючись далі уздовж копіра, що опускається, занурює блок у суспензію. Суспензія у ванні прохолоджується проточною водою, що пропускається через сорочку під днищем ванни. Для запобігання осідання пилоподібної складової суспензії остання безупинно перемішується (мішалка не схемі на показана).
При подальшому русі конвеєра блок виходить із суспензії й надходить у пескосип «киплячого шару» 6 з перфорованою перегородкою 7. У пескосипе відбувається обсипання нанесеного шару суспензії зернистим вогнетривом. У міру витрати суспензії ванну поповнюють, для чого в бак 11, де зберігається суспензія, подають стиснене повітря, яке вичавлює її через трубу 9 і далі по шлангові 2 у ванну. Після видачі необхідної кількості суспензії подачу стисненого повітря припиняють, а тиск у баку 11 скидають. У баку суспензія безупинно перемішується мішалкою 10 і прохолоджується водою. У ванні із суспензією передбачені обладнання для зливу й промивання, а в пескосипе система очищення піску
Механізована потокова лінія заформовивания оболонок, прожарювання, заливання форм, охолодження й вибивки виливків конструкції ЗИЛ (мал. 10.6). Замкнену потокову лінію утворюють установка для заформовивания оболонок в опорний наповнювач (в опоках), пекти 1 для прожарювання, заливальний роликовий конвеєр 3, камера охолодження 5, обладнання 6 для вибивки опок і роликовий конвеєр 8 для повернення порожніх опок
В опоки, розташовані на формувальних столах 11, ставлять оболонки й зверху з бункерів 12 насипають опорний наполинитель, що ущільнюється вібраторами. Наполинитель, розсипаний при заповненні опок, попадає в прийомний бункер пневмотранспорту й вертається в бункери 12. Заформованние опоки штовхальниками 9 просуваються в газову дворядну прохідну піч 1 для прожарювання. Прожарені опоки витягають із печі за допомогою ланцюгових витаскивателей і подають на прийомні столи 2. Продукти го-
Рис. 10.6. Механізована потокова лінія для заформовива-ння оболонок, прожарювання заливання форм, охолодження й вибивки виливків
.
ренію віддаляються з печі димососной установкою 10. Прийомні столи 2 опускають і ставлять опоки на приводний рольганг 3, на якому форми заливають розплавом. Після заливання опоки по роликовому конвеєру надходять на піднімальний стіл 4, який піднімає їх до рівня роликового конвеєра камери охолодження 5. В останню опоки переміщаються гідравлічним штовхальником. Охолоджені опоки з камери надходять у поворотне обладнання 6 для вибивки. Під час повороту опок включають пневматичні вібратори й наповнювач із опок висипає через решітку на єкс-.
центриковое сито. Відсівання зсипається в ящик, що коштує на роликовому конвеєрі, а просіяний наповнювач системою пневмотранспорту 13, 14 вертається в бункери, розташовані над формувальними столами. Після вибивки машина вертається у вихідне положення й опока надходить на прийомний стіл 7 роликового конвеєра 8 повернення порожніх опок. Тут виливка видаляють із опок, а останні знову подають на формувальні столи
Якщо дозволяють умови, те заливальний майданчик краще виконувати піднятої над рівнем підлоги. У цьому випадку відпадає необхідність опускати опоки по виходу їх з печі й піднімати для подачі в камеру охолодження. Камера охолодження повинна мати об`єм, приблизно дорівнює печі прожарювання; а якщо ні, то форми не встигнуть досить остудитися. Отже, у розглянутій схемі камера охолодження повинна бути дворядної
Комплексна механізована потокова лінія прожарювання, формування, заливання оболонок форм, вибивки й охолодження виливків (мод. 675А). Ця лінія (мал. 10.7) розрахована на прожарювання оболонок без опорного матеріалу. Вона складається з печі прожарювання 1, заливальної каруселі 3 і камери охолодження 7, об`єднаних конвеєром 9.
Оболонки форми встановлюють на підвіски 10 конвеєра, ливникові лійки закривають ковпачками, які фіксують оболонки на підвісках і охороняють їхні порожнини від засміття. Конвеєр транспортує підвіски через піч прожарювання. Усередину печі
Рис. 10.7. Схема комплексної механізованої потокової лінії прожарювання, формування» заливання оболонок форм, вибнвки н охолодження блоків отлнвок.
через щілину у зводі заходить тільки нижня частина підвіски з жаростійкої сталі, ланцюг же конвеєра, ходова частина підвісок і траса працюють поза гарячою зоною печі. Зверху уздовж усієї щілини у зводі передбачена витяжна вентиляція для отсоса газів, що вибиваються з печі. Прожарені оболонки у виходу з печі поринають у гарячий пісок, яким заповнений жолоб заливальної каруселі
Привод заливальної каруселі здійснюється конвеєром через зірочку 4. Опускання підвісок виконує пневматичний ліфт 6, який перекидає каретку підвісок з верхньої траси на нижню при русі конвеєра. При опусканні штанга підвіски сковзає у втулці тягового ланцюга конвеєра. Занурення підвісок з оболонками в пісок стає можливим завдяки створенню на позиціях занурення (формования) «киплячого шару». «Кипіння» його досягається продувкою знизу гарячими газами, що надходять із печі через нерухливий колектор 2. Труби колектора опущені в жолоб каруселі через край і не заважають обертанню її, працюючи в «киплячому шарі» подібно плугу
При подальшому русі конвеєра оболонки, занурені на підвісках у пісок виходять із зони «кипіння» і виявляються за-формованними. По зовнішньому сектору обертової каруселі форми заливають розплавом. Перед заливанням відкидають ковпачки, що прикривають ливникові лійки
Блоки виливків, затвердевая й частково прохолоджуючись в опорному наповнювачі, рухаються до камери 7. У входу в камеру підвіски із залитими блоками висмикують із каруселі пневматичним підйомником 5. При цьому каретка підвіски переставляється з нижньої траси назад на верхню. Пісок з підвісок і блоків виливків зсипається в жолоб каруселі, а підвіска із блоком виливків продовжує рух по конвеєру, проходить у камеру 7, де виливка остаточно прохолоджуються водяним душем. Вишедшие з камери 7 блоки виливків знімають із підвісок, і останні вертаються на робоче місце установки оболонок. Знизу уздовж камери охолодження проходить стрічковий конвеєр 8, що передає змитий водою пісок і шматочки оболонки на загальноцеховий конвеєр убожи відходів
Для підтримки постійного рівня піску в жолобі каруселі є бункер досипання, у який сухий пісок подають зі складу пневмотранспортом
Автоматична лінія очищення виливків від оболонки й відділення виливків від стояка конструкції Ниитавтопром (мал. 10.8). Лінія має три основні механізми: установку очищення виливків II, горизонтальний гідравлічний прес для відділення виливків від стояка / (гідравлічна станція на малюнку не показана) і конвеєр III.
При роботі лінії на прийомні призми 9 візка конвеєра 15 укладають блок виливків 8. У вихідному положенні візка друга пара призм 7 із блоком перебуває на позиції очищення виливків. Переміщаючись по напрямним 6, візок передає блок 8 на позицію очищення, а очищений блок на прес. Приводом візка кін-
вейера служить пневмоцилиндр 10, що діє через кулісний механізм 11. При підході до крайніх положень візок піднімає завдяки формі напрямних 6, а при зворотному ході починає свій рух з опускання. Цим забезпечується безперешкодний вихід призм із зачеплення із затиснутими на робочих позиціях блоками при відході візка конвеєра
Механізм очищення складається із циліндра затиску блоків 16 і вібраційного обладнання 14, змонтованих на загальній станині. При підході візка конвеєра блок виливків, поданий на очищення, зажимается між упорами відбійного молотка й затискного циліндра за рахунок спрацьовування пневматичних циліндрів. Потім візок відходить, включається відбійний молоток і починається очищення виливків від оболонки. Щоб уникнути твердих ударів відбійний молоток подпружинен. шматочки, що відскочили, оболонки падають униз і через проріз станини зсипаються на стрічку конвеєра збирання відходів. Тривалість очищення регулюють за допомогою реле часу. Після закінчення очищення упори розсовуються й блок виливків спадає на призми 7.
При наступному ході візка очищений блок подається на гідравлічний прес. На робочій позиції преса блок зажимается між упором 2 робочого циліндра 1, що впирається в лійку, і штоком 4 підпірного циліндра 5, що впирається в металлоприем-никнув. Після відходу конвеєра під дією робочого циліндра
Рис. 10.9. Схема відділення виливків від стояка на горизонтальному пресі:.
1 — упор робочого циліндра; 2 — шток підпірного циліндра;.
3 — фильера.
стояк проштовхується через фильеру (мал. 10.9). Хід преса може бути пульсуючим. Робочі крайки фильери сколюють живильники й виливка падають на похилий стіл 12 (див. мал. 10.8) преса й далі в тару або на стрічку конвеєра. Підрублений стояк виштовхується з фильери штоком підпірного циліндра
Підрублений стояк убирається з робочої зони преса маніпулятором 13 із захопленням 3 і скидається їм у тару або на конвеєр. На позицію, що звільнився, преса подається для обрубання наступний блок виливків
Робота механізму очищення й преса йде одночасно, синхронність і блокування забезпечуються системою автоматики. Лінію обслуговує один робітник, який укладає блоки виливків на прийомні призми конвеєра й стежить за роботою механізмів
Напівавтоматична установка для обрубання живильників конструкції НИИТАвтопрома (мал. 10.10). Установка створена на базі преса мод. ДО2130А и оснащена поворотним столом 1, на якому встановлено шість пристосувань. У кожне з них на позиціях завантаження вручну укладають виливка. Дві позиції завантаження рас-
Рис. 10.10. Напівавтоматична установка для обрубкн живильників
покладені на виступаючий з-під преса стороні поворотного стола. Стіл повертається при кожному ході преса на 60° і по черзі подає пристосування з виливками на позицію обрубання — під ніж, укріплений на верхній плиті 5. При робочому ході повзуна преса виливки спочатку притискаються до пристосувань механізмом притиску 7, а потім ніж зрубує виступаючий живильник. Відрубані живильники провалюються через вікно під стіл преса в тару для відходів. Привод поворотного стола здійснюється від вала преса через верхній редуктор 2, карданний вал 3 і нижній редуктор 4. Підрублені виливки виштовхуються із пристосувань механізмом 6. Виливок падає на лоток і потім зсковзує в тару 8, установлену збоку преса. Продуктивність установки до 2100 виливків вчас.
Механізація зважування й транспортування шихти до плавильних печей. У цехах лиття по виплавлюваних моделях у якості шихтизвичайно використовують відходи ковальсько-штампувальних цехів (висічку, рицину), відходи власного виробництва (літники, шлюб виливків), а також феросплави й свіжий метал
На мал. 10.11 наведений план розташування встаткування для зважування й транспортування шихти, по проекту Гипротрак-Торосельхозмаша. На складі шихти є кран 1 з магнітною шайбою для розвантаження металу й роздачі його по бункерах 2. Для кожної складової шихти передбачений свій бункер. Уздовж фронту бункерів по ресльсам паредвигается вагарня візок 3, на платформу якої ставлять баддю. Робітник під`їжджає на ваговому візку до потрібного бункера, включає живильник 4 і шихта надходить у баддю. Набравши потрібну кількість, робітник відключає живильник і переїжджає до іншого бункера для зважування наступного компонента. Після набору всієї порції шихти баддя підвозиться на позицію 5, де чіпляється за єлектроталь, що розвозить шихту по плавильних печах 6.
Автоматизація за допомогою промислових маніпуляторів. На мал. 10.12 показаний план розташування механізмів автоматичної лінії для виготовлення модельних блоків конструкції Ниитаавтопрома й ХФ Вниилитмаша. На лінії виготовляються ланки моделей з пінополістиролу й збираються в блоки. Лінія складається з 10-позиційного термопластавтомата 1 для виготовлення ланок моделей, автомата складання блоків моделей 2 із вбудованим маніпулятором 3 і двох окремо вартих маніпуляторів 4 я 6 із програмним керуванням. Маніпулятор 3 забирає виготовлена ланка моделей з відкритої прес-форми на позиції А термопластавтомата й надягають його на стояк, розташований на позиції Б автомата складання. Маніпулятор 4 переважує зібрані модельні блоки з автомата складання на конвеєр, що штовхає, а маніпулятор знімає з конвеєра, що штовхає, стояки й установлює їх на поворотній стіл автомата складання. Підвіски конвеєра, що штовхає, фіксуються проти маніпуляторів остановами 5 [80, 81].
Рис. 10.11. План розташування встаткування для зважування й транспортування шихти
На мал. 10.13 показаний маніпулятор із програмним керуванням, спроектований ХФ Вниилитмаша для цехів лиття по виплавлюваних і випалюваних моделях. Маніпулятор призначений для заміни людини на важких, монотонних і шкідливих операціях, наприклад при изг товлении оболонкових форм
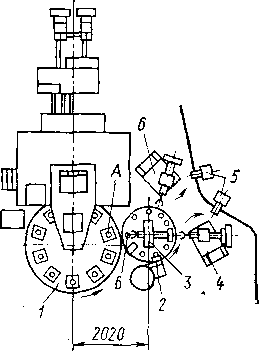
Рис. 10.12. План розташування механиз мов автоматичної лінії для изготов леиия модельних блоків
Технічна характеристика маніпулятора мод. 5102
Є позитивний досвід використання автоматичних маніпуляторів у цеху лиття по виплавлюваних моделях заводу «Авто-цветлит» ( м. Мелітополь). У цьому цеху маніпуляторами замінили робітників на важкій операції знімання залитих блоків з підвісок агрегату мод. 675А.
Механізація управлінської праці. В умовах комплексної автоматизації виробничих процесів велике значення набуває механізація й автоматизація робіт, пов`язаних з обліком і оперативним керуванням виробництвом
Рис. 10.13. Маніпулятор із програмним керуванням мод. 5102.
.
На мал. 10.14 наведена принципова схема оперативного керування великим цехом, розроблена Ниитаавтопромом. Технічні засоби оперативного керування виробництвом виконують наступні функції:.
дистанційний автоматичний облік числа зібраних блоків моделей, оболонок (придатних, забракован, що зробили на прожарювання) і підрублених блоків виливків;.
дистанційний автоматичний облік запасу оболонок на складі; дистанційний напівавтоматичний облік числа виливків по найменуваннях, що зробили на склад і виданих зі складу готової продукції цеху;.
автоматичне фіксування облікової інформації на рапорті за допомогою єлектроуправляемой друкарської машинки;.
дистанційну автоматичну передачу всієї облікової інформації в інформаційно-обчислювальний центр заводу (ІОЦ), який розробляє й видає цеху подетальние виробничі програми запуску й випуску, обробляє аналітично зведення виконання планів цехом;
Рис. 10.15. Розташування технічних засобів обліку й оперативного керування виробництвом:.
1 — зал генераторів; 11 — плавильна ділянка; 111 — ділянка обжнга, формування, заливання оболонкових форм, вибивки й охолодження блоків отлнвок; IV — ділянка виготовлення оболонкових форм; V -ділянка виготовлення модельних блоків; VI -ділянка готування модельної сполуки; VII — ділянка очищення отлнвок; VIII — ділянка термообробки; IX — ділянка обрубання й обробки отлнвок; X — склад виливків; XI — ремонтна майстерня; XII — ділянка готування суспензії; XIII — експрес-лабораторія; XIV — диспетчерський^-диспетчерський-контрольно-диспетчерський пункт; XV — склад шихти; 1 —- вимірювальний перетворювач контролю виробничого стану встаткування; 2 — вимірювальний перетворювач контролю технологічного параметра; 3 — вимірювальний перетворювач рахунку; 4 — динамічний гучномовець; 5 — цифрове табло
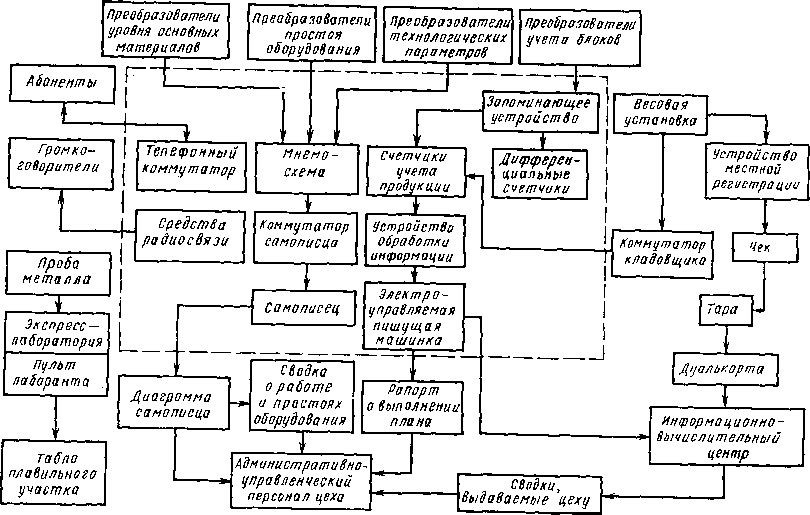
Рнс. 10.14. Принципова схема оперативного керування цехом лиття по виплавлюваних моделях (технічні засоби контроль-але-диспетчерського пункту виділені рамкою)
Рис. 10.16. Диспетчерський^-диспетчерський-контрольно-диспетчерський пункт цеху
.
сигналізацію про виробничий стан основного встаткування цеху;.
автоматичну, вибіркову реєстрацію часу роботи й простоїв основного встаткування цеху;.
дистанційний автоматичний контроль наявності основних матеріалів;.
диспетчерську телефонний зв`язок усередині цеху;.
виробничу радіофікацію цеху;.
передачу результатів хімічного аналізу металу з експрес-лабораторії на плавильну ділянку
На мал. 10.15 показане розташування технічних засобів стосовно до плану розташування встаткування цеху потужністю 4000-5000 т у рік. Уся отримана інформація зосереджує в диспетчерський^-диспетчерськім-контрольно-диспетчерському пункті (КПД) (мал. 10.16). керуюча апаратура, Що сигналізує й, розташована на панелях пульта диспетчера 1. На панель винесені диференціальні лічильники, показання яких необхідні диспетчерові для оперативної діяльності, а інші встановлено в шафах 2. Допоміжна апаратура змонтовано в стійках 3. Комутатор 4 — на столі
Функції оперативного керування виробництвом здійснюються наступним образом
Зібрані модельні блоки вважаються контактними перетворювачами на конвеєрах, що передають блоки з модельної ділянки до автоматів виготовлення оболонкових форм. Рахунок реєструється на КДП. Після виплавления моделей підрахунок оболонкових форм проводиться на конвеєрах їх, що подають, на випал. Тому що частина з них може не зніматися в агрегатів випалу й вертатися до місця рахунку, число їх визначають як різниця між числами про.
шедших пб, Що Подає й поворотної галузям конвеєра. Вирахування проводиться автоматично диференціальним лічильником. Облік забракованих оболонок здійснюється аналогічно, як різниця між числом виплавлених і суми, що зробили на склад і на агрегати випалу
Оболонки, що зробили на прожарювання, ураховуються на конвеєрах агрегатів випалу вимірювальними перетворювачами, сигнали з яких надходять на запам`ятовувальний пристрій, а після опитування — на лічильники апаратної шафи КДП.
Підрублені блоки виливків ураховують вимірювальні перетворювачі, установлені на пресах-автоматах для відділення виливків від стояка
Дистанційний напівавтоматичний облік виливків ( по найменуваннях), що зробили на склад готової продукції цеху, здійснюється за допомогою установки, що полягає із платформних ваг із циферблатним покажчиком, що дозволяють перетворювати масу зважених виливків в електричні імпульси; обладнань місцевої реєстрації маси й передачі даних зважування на відстань. При вступі на склад чергового стандартного ящика з однаковими виливками комірник ставить його на платформу ваг і на пульті набирає шифр виливків, що зважуються. Переконавшись у правильності набору шифру по контрольній сигналізації, комірник натискає кнопку «Уведення інформації». При цьому дані
про масу виливків фіксуються на стрічці реєстрації й передаються в КДП на відповідний лічильник. Крім цього, дані про масу виливків надходять на підсумовуючий лічильник, і диспетчер може стежити за загальною масою виливків, випущених цехом. Після зважування комірник направляє ящик з виливками на стелаж, супроводжуючи його чеком з даними зважування, який він відриває від стрічки реєстрації маси виливків
Для обліку виливків, виданих зі складу, служить дуаль-карта. По чеку, що перебуває в ящику з виливками, комірник відзначає масу партії, що відправляється, у дуаль-карті й відправляє її на ИВЦ.
По команді диспетчера автоматично друкується рапорт із усією інформацією, накопиченої на КДП. Цей рапорт використовується керівництвом цеху для оцінки діяльності підрозділів цеху. Дистанційна передача інформації в ІОЦ здійснюється по його запиту раз у добу в тому ж об`ємі, що й на внутрішнцеховому рапорті. В ІОЦ ця інформація використовується при складанні аналітичних зведень про виконання плану цехом, для внесення корективів у програму цеху й др.
Сигналізація про виробничий стан устаткування здійснюється за допомогою мнемонічної схеми. На зображенні агрегатів (на схемі) установлені лампи, що сигналізують про зупинку агрегатів. Крім того, на мнемонічній схемі є сигнальні лампи, що попереджають про порушення технологічних параметрів, що впливають на якість продукції, що випускається
Тривалість роботи й простоїв устаткування реєструється за допомогою автоматичного самописного приладу. Автоматична реєстрація дозволяє аналізувати роботу встаткування за об`єктивним даними й ухвалювати необхідні заходи
Контроль наявності на складі рідких складових суспензії (єтилсиликата, ацетону й ін.) здійснюється вимірювальними перетворювачами — рівнемірами, установлюваними в ємностях їх зберігання
Диспетчер має у своєму розпорядженні телефонний комутатор (з обладнаннями світлового виклику абонента в гучних місцях цеху) і 20 каналів гучномовному зв`язка, підключати які можна по одному й усі відразу. Засобу радіозв`язку використовують для пошуку й виклику працівників цеху, для розпоряджень, оголошень і т.п. Сигналізація хімічного аналізу металу забезпечує швидку передачу відомостей з експрес-лабораторії на плавильну ділянку. По команді з лабораторії на табло плавильної ділянки загоряються цифри, що позначають зміст хімічних елементів у сотих частках відсотка
10.2. ЦЕХИ ЛИТТЯ ПО ВИПЛАВЛЮВАНИХ МОДЕЛЯХ
Цехи лиття по виплавлюваних моделях у структурі машинобудівного підприємства відносять до основних (виробничим) заготівельним ливарним цехам
Цехи розрізняють (табл. 10.1) по роду сплаву, масі виливків, обсягу виробництва, серійності, ступені механізації й складності виливків
До складу цехів входять виробничі відділення (ділянки), допоміжні відділення (ділянки) і склади
До виробничих відділень, де виконується властиво технологічний процес виготовлення виливків, відносять наступні: модельне, у якому готують модельну сполуку, виготовляють моделі, збирають блоки моделей; виготовлення оболонок форм, у якому готують суспензію, виготовляють оболонки, виплавляють із них моделі; прокалочно-заливальне, у якому оболонки форм заформовивают в опорний наповнювач і прожарюють, плавлять і заливають у форми метал, прохолоджують і вибивають блоки виливків; термообрубное, де очищають виливка від залишків оболонок, відокремлюють виливка від ЛПС, зачищають живильники, проводять термообробку й виправляють дефекти виливків
До допоміжних відносять наступні відділення: підготовки формувальних матеріалів і шихти, ремонту прес-форм і іншого технологічного оснащення, майстерні механіка й енергетика, цехову лабораторію, вентиляційні й пилеочистние установки й КДП.
До складів відносять закриті склади шихтових, формувальних, горючих матеріалів, готових виливків
У цеху передбачають також приміщення для культурно-побутового обслуговування працюючих: санітарно-побутового призначення, громадського харчування, охорони здоров`я, культурного обслуговування, навчальних занять і громадських організацій, керувань
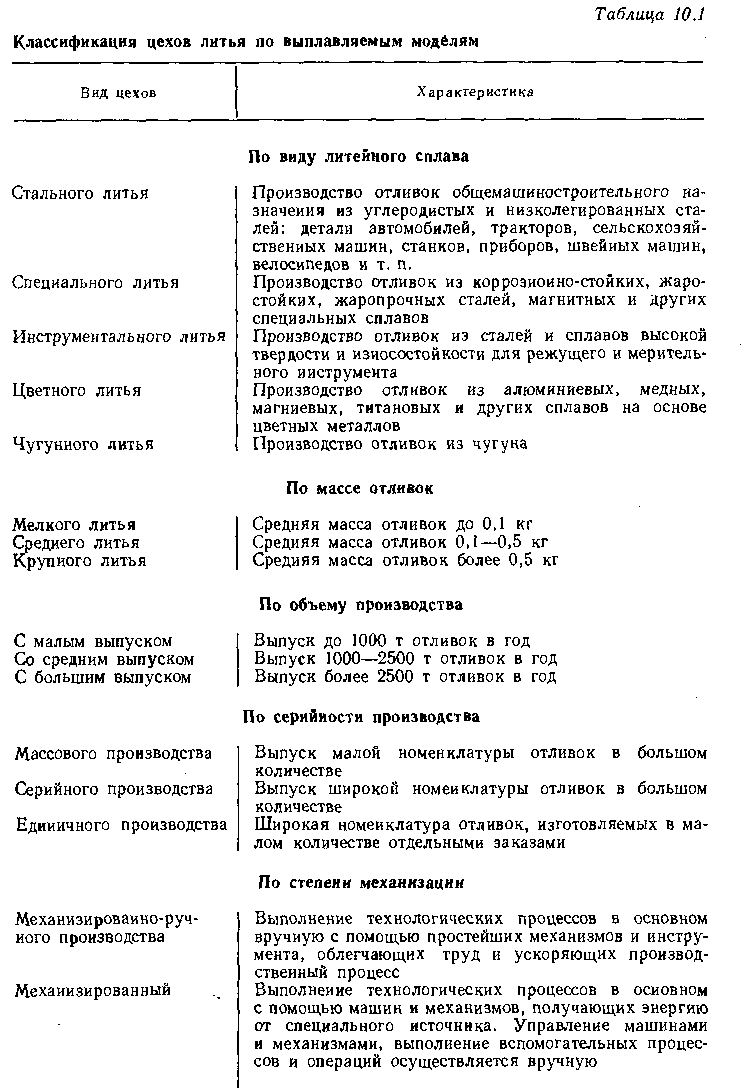
* Групи складності виливків прийняті відповідно до прейскуранта оптових цін на виливки
РОЗРОБКА ТЕХНОЛОГІЧНОЇ ЧАСТИНИ ПРОЕКТУ ЦЕХУ
Вихідними даними для розробки проекту цеху служать наступні основні документи: завдання на проектування (включає техніко-економічне обґрунтування проекту); виробнича програма; креслення й технічні умови на виливки
Виробнича програма. Програма монсет бути точної (подетальной), наведеної або умовної. Подетальную програму виробництва масових і крупносерийних виливків становлять за формою 10.1 Програму приводять по видах металу, виробам і вузлам (групам) у порядку зростання номерів вузлів і деталей. На підставі подетальной програми становлять виробничу програму за формою 10.2, яку заповнюють по видах і маркам металу
Технологічний процес і встаткування. Вибір варіанта технологічного процесу є визначальним, головним у проек-
тировании цеху. Обрані варіанти технологічного процесу й устаткування повинні забезпечувати одержання виливків потрібної якості з найменшими трудовими й матеріальними витратами. Для виконання цього завдання проектувальник повинен не тільки мати відомості про передовий вітчизняний досвід, але й ураховувати дані науково-технічного прогнозу, щоб до моменту введення в експлуатацію нове виробництво було на рівні світових технічних досягнень
Для оцінки варіанта нового технологічного процесу його порівнюють із найкращим з відомих, який ухвалюють за базовий. Оптимальною технологією виготовлення виливків уважають ту, яка забезпечує мінімум наведених народногосподарських витрат на виробництво готових деталей
Для практичних розрахунків на вибір оптимального технологічного процесу Б. В. Кнорре рекомендує використовувати спрощену формулу
де Сц і З
- собівартості виготовлення виливків у ливарному цеху й механічної обробки, руб/т, руб/шт; В
-випуск виливків, т/рік, шт/рік; Е
- коефіцієнт ефективності капітальних вкладень, £
»0,12; ДО
до Ки — капітальні вкладення по варіанту
технології виробництва виливків у ливарному цеху й у механічному цеху, руб.
_ .
.
У відповідних главах книги дані основи для вибору технології й устаткування, що відповідають особливостям виробництва виливків різного призначення
.. У табл. 10.2 наведені рекомендовані процеси й устаткування ( без плавильного) для цехів, що випускають дрібні й середні сталеві виливки
Вихідні технологічні дані окремо по кожній групі по масі розраховують і затягають у відомості за формою 10.3.
Форма 10.3.
Вихідні технологічні дані (група виливків по масі)
№ п.п | Я Ч. 03. Н | Маса отливкн, кг (А) | Про. грама | Число моделей у ланці (В) | Число звеньеа в блоці | Число моделей у блоці (Г) . | Число модельних ланок (моделей) на програму | Число блоків на програму (Д) | Маса модельної сполуки, кг | |||
шт. (Б) | кг | на одну модель (Е) | на один блок (Ж) | на. про. граму | ||||||||
Б/В | Б/Г | Api/p а | ЕХГ+ + Vnpi | ЖХД | ||||||||
Разом |
Примітка. Pi, Рг — щільності відповідно модельної сполуки й матеріалу отливкн, кг/м*; — об`єм ЛПС і модельного стояка (нлн суми модельних втулок), м
Рекомендується розподіл номенклатури виливків на вісім груп по масі, кг: 1,5. Такий розподіл виправданий тим, що для кожної групи виливків характерні свої технологічні нормативи й показники
Форма 10.3 містить тільки вихідні технологічні дані й використовувати їх для розрахунків числа встаткування не можна. У цих даних не враховані неминучі на виробництві втрати й шлюб через неякісні матеріали, помилки робітника, несправності встаткування й інших причин. Шлюб і втрати на виробництві відшкодовують шляхом збільшеного проти програми виготовлення моделей, форм або виливків по переходах процесу. Для визначення числа Підлягаючих изготовленоию моделей, форм і виливків на яке розраховують устаткування, уводять коефіцієнти технологічних потесь:

де В
п
- число виливків, форм або моделей, яке необхідно виготовити в даному відділенні для виконання програми і для заповнення шлюбу й втрат; В -число виливків, форм або моделей по програмі ( без обліку шлюбу й втрат).
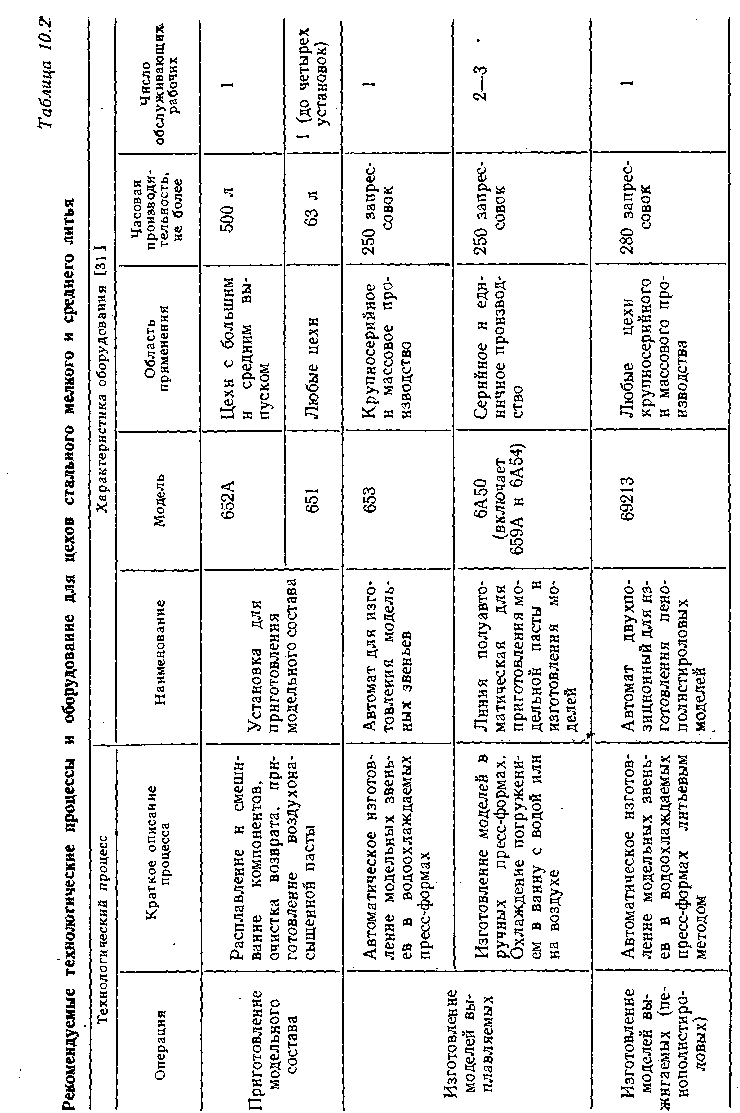
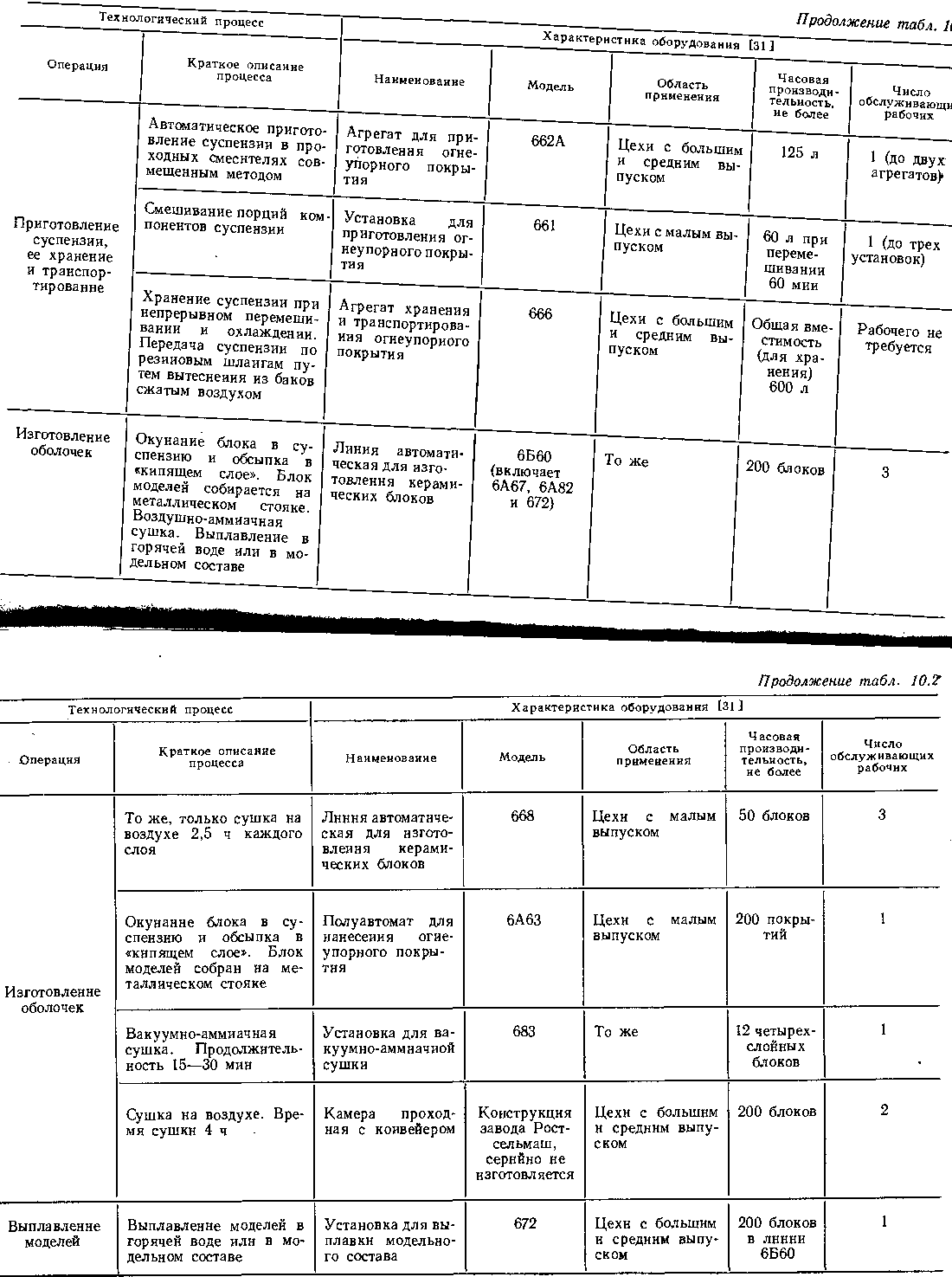
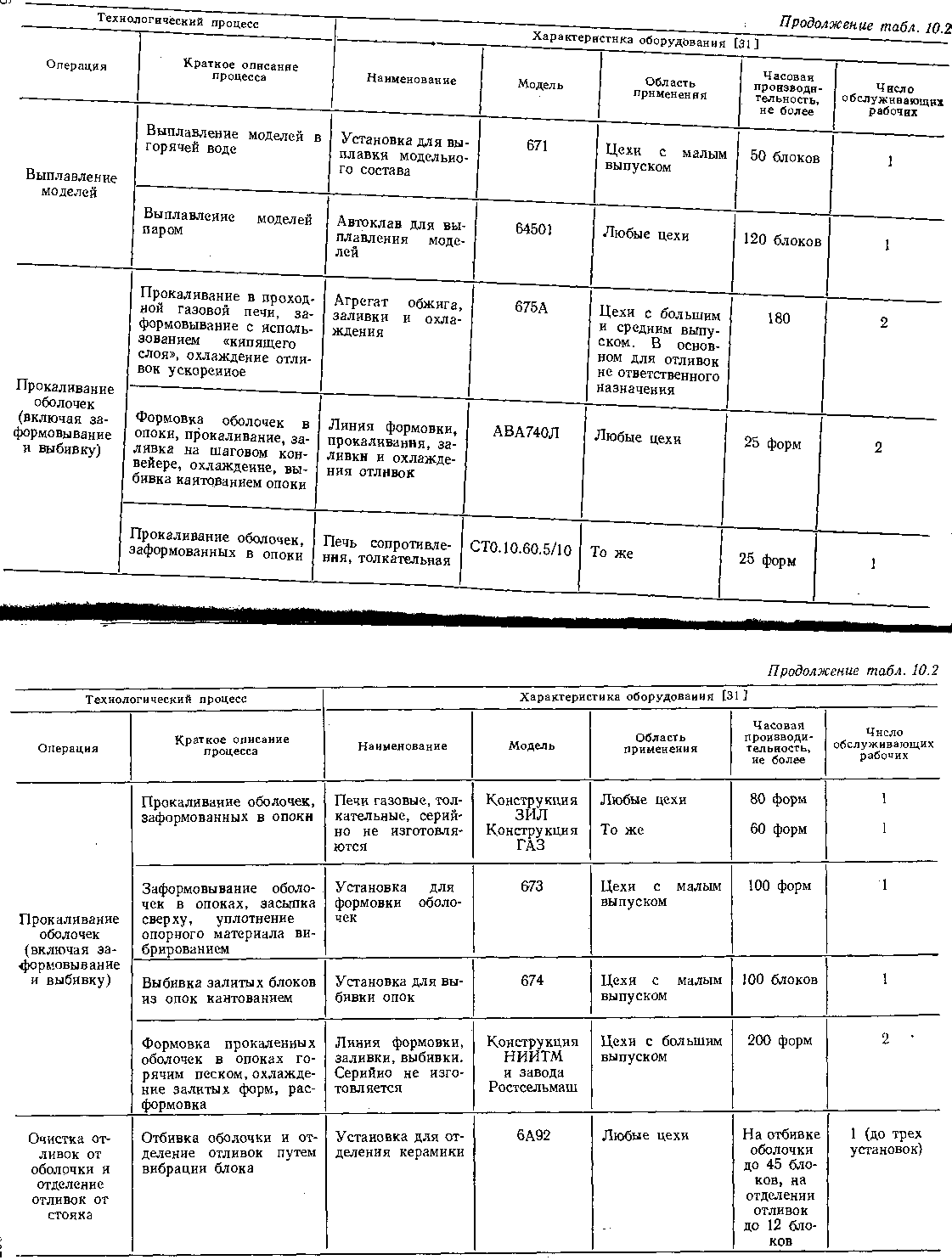
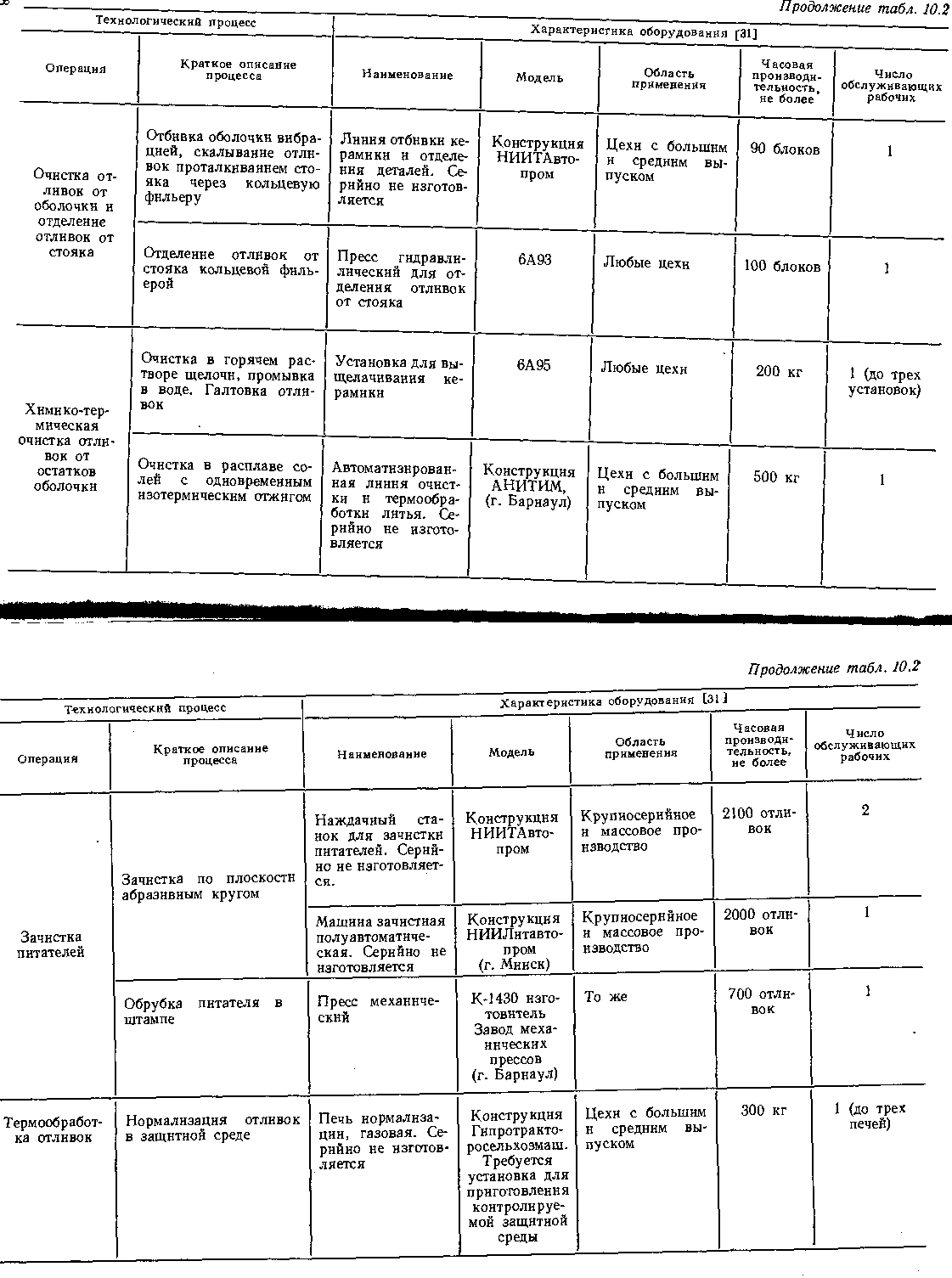
Для кожної виробничої ділянки (групи операцій) розраховують свій ДО шлюб, що враховує втрати й, не тільки цієї групи операцій, але й усіх наступних (табл. 10.3).
Таблиця 10.3.
Зразкові коефіцієнти технологічних втрат
Група операцій або виробнича ділянка цеху | Ті> нологиче-ские втрати й шлюб, % | Коефіцієнти технологічних втрат |
Виготовлення модельних блоків | 15 | 1,42 |
Виготовлення форм | 3 | k 3 = 1,2 |
Обжнг форм, плавка н заливання металу | 5 | k 2 = 1,16 |
Обрубка, термообробка н обробка отлнвок | 9 | *1“ 1,1 |
Визначивши k
-k
,можна становити відомість обсягів виробництва для розрахунків основного встаткування за формою 10.4.
Примітки. I. k — коефіцієнти технологічних втрат; n
- число моделей елементів ливникової системи на одні блок (чаша, металлопрнемннк н т.п.); — маса літників иа один блок; k
м — коефіцієнт, що враховує потерн металу на вигар, скрап, зливи й т.п., для сталі &
1.06, для кольорових сплавів k
м 1,08.
2. Масу суспензії розраховують у завиишости від числа £лоев за укрупненими показниками (див. табл. 10.4) або, якщо номенклатура виливків невелика, по поверхні отлнвок,.
Відносно точно витрата суспензії на програму можна визначити по сумарній поверхні модельних блоків. Середня витрата суспензії на 1 дм
поверхні моделі при нанесенні одного шару становить 0,001 дм
або 16-17 г ( при змісті в.
суспензії 72 % по масі пилоподібного кварцу). Приклад розрахунків витрати компонентів суспензії наведений вгл. 11.
У табл. 10.4 наведені орієнтовні показники для рас. четов вихідних даних
Таблиця 10.4.
Орієнтовні показники для сталевих виливків середньої складності
Показник | Групи | виливків по масі, кг | ||||||
До. 0,02 | 0,02 — 0,04 | 0,04 — 0,06 | 0,06 — 0,! | 0,1-. 0,2 | 0,2-. 0,6 | 0,6-. 1,5 | 1,5 н бьлее | |
Вихід придатного від зачи | 21 | 34 | 40 | 44 | 48 | 53 | 57 | >57 |
того металу, % | ||||||||
Витрата на 1 т придатних | ||||||||
виливків, кг: | , ~ год | |||||||
суспензії на один шар | 290 | 200 | 170 | 155 | 126 | 95 | ||
покриття | ||||||||
модельної сполуки | 90 | 80 | 70 | 60 | 50 | : 45 / | 40 | |
( при 10 % втрат) | • | |||||||
піску | 1300 | 1000 | ||||||
Кількість перерабати | 900 | 800 | 700 | 600 | 500 | 450 | 400 | |
ваемого модельного з | ||||||||
става на 1 т придатних отли | ||||||||
вок, кг | ||||||||
Число отлнвок (моделей) | 100 | 80 | 60 | 40 | 20 | 10 | 6 | 4 |
у блоці довжиною 500 мм |
Розрахунки числа встаткування. При проектуванні цеху число кожного виду основного технологічного встаткування визначають по формулі /
де В
-річна кількість матеріалу, що переробляється (суспензії, модельної сполуки, піску і т.д.) або число модельних ланок, блоків, виливків; Н ■- годинна продуктивність одиниці встаткування (розмірність та ж, що й для В
); ф
-дійсний (розрахунковий) річний фонд часу роботи встаткування при обраній змінності, год (табл. 10.5).
У зв`язку з тим, що в розрахунковому річному фонді часу роботи встаткування враховують тільки втрати часу на планово-запобіжний ремонт устаткування й не враховують непередбачені простій устаткування, при проектуванні ухвалюють до установки трохи більше число встаткування (з округленням у більшу сторону, до цілих одиниць), чим виходить по розрахункові
Розмір резерву, який повинен компенсувати непередбачені простої встаткування, характеризується коефіцієнтом.завантаження встаткування :•*.»,v».
де Рр -розрахункове число встаткування; Р — прийняте число, одиниць устаткування
Дійсний (розрахунковий) річний фонд часу роботи встаткуванні (рабочаи тиждень 41 год, у році вісім святкових днів)
Устаткування | Число змін | Номінальний річний фонд часу, год | Потерн, % номінального фонду часу | Дійсний річний фонд часу, год |
Устаткування для готування | 1 | 2070 | 2 | 2030 |
модельної сполуки й суспензії, | 2 | 4140 | 4 | 3975 |
виготовлення моделей і форм, ви | 3 | 6210 | 5 | 5900 |
плавлення моделей, формування й вибивки виливків, обрубки н очищення Те ж, особливо складне | 2 | 4140 | 9 | 3770 |
3 | 6210 | 11 | 5525 | |
Автоматичне встаткування н ав | 2 | 4140 | 12 | 3645 |
томатические лннни | 3 | 6210 | 14 | 5340 |
Індукційні печі підвищеної | 1 | 2070 | 4 | 1985 |
частоти для плавки стали, умісти | 2 | 4140 | 6 | 3890 |
мостью 0,06-2,5 т | 3 | 6490 | 12 | 5710 |
Печі плавильні: для мідних сплавів | 1 | 1830 | 3 | 1775 |
2 | 3660 | 4 | 3510 | |
3 | 5490 | 6 | 5160 | |
для алюмінієвих і інших ліг | 1 | 2070 | 3 | 2010 |
ких сплавів | 2 | 4140 | 4 | 3975 |
3 | 6210 | 6 | 5840 | |
Печі для прожарювання форм і термообробки виливків:. з безперервним режимом роботи, | 3 | 8760 | 11 | 7800 |
механізовані з коротким циклом роботи, не- | 2 | 4140 | 4 | 3975 |
механизнрованние | 3 | 6210 | 6 | 5840 |
Примітка. Втрати часу для встаткування визначені, виходячи нз його простоїв, при планово-предупредительиом ремонті
.
Коефіцієнт k
,
повинен бути таким, щоб забезпечувалося виконання програми в реальних виробничих умовах при відсутності невикористовуваних виробничих потужностей. Чим складніше встаткування, тем воно менш надійно в роботі, тому менше повинен бути &з.
. І навпаки, чому надійніше встаткування, тем ближче &з. про кединице.
Зразкові значення k
залежно від складності використовуваного встаткування:.
Нескладне (наприклад, установка для готування суспензії мод. 661,.
ванна виплавления моделей мод. 671) ................. 0,9.
Складне (наприклад, установка для готування модельної сполуки
мод. 651, автомат для виготовлення модельних ланок мод. 653)..... 0,8.
Особливо складне (наприклад, агрегат для готування суспензії мод. 662А, агрегат прожарювання, заливання й охолодження мод. 675А)........ 0,7.
Сполука працюючих. Промислово-виробничий персонал цеху підрозділяють на наступні категорії: робітники, інженерно-.
технічні працівники (ІТП), лічильно-конторський персонал (СК.П) молодший обслуговуючий персонал (МОП). -Робітників підрозділяють на виробничих і допоміжні. Виробничими називають робітників, безпосередньо пов`язаних з виготовленням виливків
При укрупнених розрахунках число робітників може бути прийняте за даними цеху-аналога
Орієнтовні показники для визначення числа робітників наведені в табл. 10.6.
.
Таблиця 10.6.
Орієнтовні показники для визначення числа робітників
Характеристика цеху | Середньо | ||||
Галузь виробництва | Тил виробництва н річний випуск виливків, т | Ступінь механізації | облікове число виробничого персоналу, чіл | Чи. сло. рабо. чих | Випуск на один робітника, т/рік |
Автомобилестрое. ние | Масове 7100 | Комплексна механізація й автоматизація | 796 | 708 | 10,03 |
4613 | Те ж | 821 | 738 | 6,25 | |
Мотовелостроение | Масове 1000 | Комплексна механізація | 174 | 164 | 6,1 |
680 | Механізація | 140 | 126 | 5,39 | |
Тракторні двигуни | Масове 4300 | Комплексна механізація й автоматизація | 581 | 525 | 8,19 |
Сельскохозяй. ственние | Масове 3350 | Те ж | 391 | 352 | 9,52 |
Верстатобудування | Різної серійності 2000 | » | 232 | 198 | 10,1 |
Виробництво текстильних і швейних машин | Масове 1580 | Комплексна механізація | 180 | 161 | 9,81 |
Виробництво інструмента | Різної серійності 200 | Механізація | 45 | 40 | 5,0 |
Для більш,, точного розрахунків потрібно число виробничих робітників в устаткування ( у тому числі автоматичного) визначати на підставі норм обслуговування цього встаткування, шляхом проектної расртановки робітників по робітниках місцям
На ручних роботах, там, де відсутній примусовий темп роботи встаткування й продуктивність залежить від робітника, або там, де можливо виконання робітником декількох операцій або обслуговування декількох машин, число виробничих робітників визначають по трудомісткості цих робіт (метод розрахунків наведений нижче).
Число допоміжних робітників або визначають по робочих місцях і ділянкам цеху, по нормах обслуговування, або, як при-ведено нижче, ухвалюють у відсотковому відношенні до виробничих робітників:
Число ІТП, СКГ1 і МОП ухвалюють у наступному процентному відношенні до загального числа робітників: 7 — 9 % ІТП; 0,6 — 1 % СК.П; 1,5 —2 % МОП.
Розрахунки числа виробничих робітників по трудомісткості робіт. Необхідне число виробничих робітників для виконання програми в цілому по цехові або на зданную групу операцій визначають по формулі
де 7’
- норма часу на виготовлення виливків або на дану групу операцій на річну програму, год; Т
- дійсний (розрахунковий) річний фонд часу робітників, год (табл. 10.7),
де Т
- норма часу на виготовлення одному виливка або на виконання даних операцій на один виливок, хв; п -число виливків на річну програму;
t
- норма часу на виконання окремої операції на один виливок, мін
Таблиця 10.7.
Дійсний (розрахунковий) річний фонд часу робітників
Тривалість робочого тижня, год | Номінальний річний фонд часу, год | Тривалість основної відпустки, дин | Потерн від номінального фонду часу, % | Дійсний (розрахунковий) річний фонд часу робітника, год |
41 | 2070 | 15 | 10 | 1860 |
41 | 2070 | 18 | 11 | 1840 |
41 | 2070 | 24 | 12 | 1820 |
36 | 1830 | 24 | 11 . | 1640 |
В умовах масового й крупносерийного виробництва норми часу на виливок (штучний час) по окремих операціях розраховують по формулі
де t
-оперативний час на операцію, прийняте по загальномашинобудівних нормативах часу на роботи при литті по виплавлюваних моделях, хв; а
бол — час на обслуговування рабо-.
чого місця, а
= 4-~-6 % оперативного; а
- час на відпочинок н особисті потреби, а
= 7-н9 % оперативного
Площі. При укрупнених розрахунках площа цеху визначають по показниках випуску (знімання) придатних виливків з 1 м
площі в тоннах. Цей показник тем вище, чим вище серійність і маса виливків, рівень механізації, змінність роботи цеху
Для комплексно-механізованих цехів сталевого лиття середньої й великої потужності, спроектованих з урахуванням вимог промислової санітарії й техніки безпеки, характерні наступні показники: знімання з 1 м
загальної площі цеху ( без побутових) 0,3 — 0,5 т/рік; знімання з 1 м
виробничої площі 0,4 — 0,7 т/рік
Для деяких існуючих ділянок і цехів, що не мають власних складів, що відрізняються великою скупченістю й недостатньо гарними умовами праці, показники знімання в 1,4 — 1, 5 рази вище зазначених
Точно площа всіх відділень цеху визначають розробкою плану розташування встаткування (див. с. 376 — 384.
Розраховують площі для складів, виходячи з норм запасів матеріалів, насипної маси (в укладанні) матеріалу й прийнятої висоти зберігання
Зразкові норми запасів для середнього кліматичного пояса на цеховому складі ( при відсутності базисного складу заводу) наступні:

Нижче наведена насипна (або в укладанні) об`ємна маса матеріалів для розрахунків складів, т/м
8
:
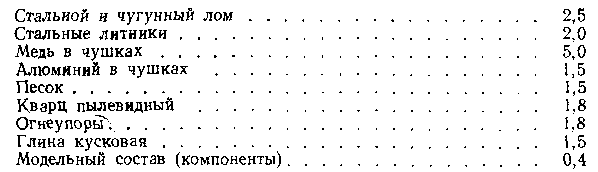
Площі (корисні) допоміжних приміщень культурно-побутового призначення ухвалюють із розрахунку 5м
на один працюючого по обліковій сполуці. У тому числі по видах обслуговування: санітарно-гігієнічне — 3,5 м
; громадське харчування — 0,78 м
; медичне — 0,09 м
; культурно-масове й цехові громадські організації — 0,3 м
; місцеве побутове обслуговування — 0,33 м
Енергетика. При розробці технологічної частини проекту визначають установлену потужність устаткування й середнє активне навантаження (кВт), витрата основних видів енергоносіїв:.
стисненого повітря (м
), природного або зрідженого газу (м
), пари (т), а також води (м
) на виробничі потреби
Дані про витрати енергоносіїв і води на технологічні потреби зводяться у відомості за формою 10.5.
Форма 10.5.
Витрата - (вид і параметри енергоносія, вода)
№ устаткування | Споживачі по відділеннях цеху | Коефіцієнт використання встаткування | Вартовий енергії влениая | витрата (устаио-. мощиость) | Річний фоид. часу,. год | Річний витрата енергії (середня активна навантаження) |
за планом | иаи-. більший | середній | ||||
Капітальні витрати на встаткування. На стадії розробки технологічної частини проекту цеху в капітальних витратах на встаткування враховують вартість усього виробничого, допоміжного й підйомно-транспортного встаткування, а також додаткові витрати, пов`язані із транспортуванням і складуванням цього встаткування, вартістю його монтажу, вартістю металоконструкцій і їх монтажу, вартістю інструмента, пристосувань, технологічного й реманенту
Нижче наведені орієнтовні розміри капітальних витрат різних видів