Примітки. 1. Самої инзкой стійкістю у вакуумі має магнезит
2: Температури плавлеиня зазначені для чистих окислів
3.
Рекомендована дисперсність пилоподібних матеріалів .
4.
Для дистен-силлиманита й муллита зазначені температури дисоціації на А1
0* і грузлу євтектическую рідина (S10
).
Рис. в.5. Схеми кремнекислородних тетраедрів у кварці:.
а — кристалічному; 6 — аморфному (плавленом). Штриховими лініями показані можливі лінії розколу при них здрібнюванні
.
Окисли. Кварци Sio
використовують кристалічної й аморфної модифікації. Перший — природний, другий одержують штучно плавленням першого й часто називають плавленим кварцом, або кварцовим склом. Відрізняються вони будовою (мал. 6.5) і термічним розширенням
Кварц кристалічний добувають у кар`єрах у вигляді кварцових пісків — формувальних і більш чистих — скляних. При нагріванні й нормальному тиску він перетерплює чотири поліморфні перетворення зі зміною щільності ( від 2650 до 2200 кг/м
):
Найбільше суттєво бистропротекающее перетворення при 573 °С, коли при нагріванні збільшується лінійний розмір на 1,4 %. Це одна із причин утвору тріщин в оболонках і засоров вотливках.
Перетворення при 870 °С - відбуваються вкрай повільно й для практики лиття значення не мають. При заливанні сталей і сплавів з високою температурою плавлення контактний шар оболонки нагрівається до 1500 °С и вище, що приводить до кристобаллитизадии кварцу зі збільшенням розмірів. Цим пояснюється низька термостійкість кварцових оболонок
Кварц кристалічний мелений пилоподібний одержують мливом чистого кварцового піску. Передбачено дві марки меленого запалі видного кварцу (МПК) (табл. 6.3).
Кварц марки А рекомендують для лицювального (контактного) шару оболонки, а марки Б — для наступних шарів з єтилсиликат-ним сполучним
Сполука кристалічного меленого пилоподібного кварцу марок А и Б,.
% по масі
Показник | А | Б |
Хімічний склад: | ||
Si0 2 , не менш | 98 | |
Fe металеве, не більш | 0,06 | 0,25 |
Fe 2 0 3 , не більш | 0,05 | 0,15 |
А1 2 0 3 , не більш | 0,5 | 1,0 |
Ti0 2 , не більш | — | 0,03 |
СаО, не більш | — | 0,15 |
Втрати при прожарюванні | 0,1-0,15 | 0,1—0,2 |
Зміст вологи, не більш | 2 | |
Зерновій сполука по залишкові на ситі, не більш: | ||
№ 016 | 1,0 | |
№ 010 | 2,5 | |
№ 0063 | 10,0 | |
Через сито № 005 повинне пройти, не менш | 85 | | 82 |
Примітка. Реакція водної витяжки нейтральна
Маршалит — природний пилоподібний кристалічний кварц, що зустрічається вкрай рідко, містить 96—98% Si0
, неоднорідний по хімічній і зерновій сполуці; його застосовувати не випливає
Кварцовий пісок застосовують для обсипання лицювального (контактного) шару марки 1 ДО016, 1 ДО020, а для наступних — більші, наприклад 1 КІЗ 15.
Кварц аморфний — кварцове скло [114]. Як показано вище, при розгляді поліморфних перетворень при 1713 °С кристо-баллит переходить у грузле кварцове скло, називане також плавленим кварцом. На відміну від кристалічного плавлений кварц являє собою затверділу переохолоджену рідину з неупорядкованою будовою. Його називають аморфним (див. мал. 6.5),.
Відомі два види кварцового скла: прозоре й непрозоре (ИКС). Перше виплавляють із найчистішого кристалічного кварцу й застосовують для оптичних приладів. Друге виплавляють зі звичайного скляного або відмитого кварцового піску. Непрозорим воно виходить тому, що містить дрібні пухирці повітря (0,003—0,3 мм), що не встигнули вийти із грузлого розплаву. Після розплавлювання піску й охолодження бруса останній дроблять, розмелюють, просівають, одержують порошки НКС, які мають мізерно низький коефіцієнт термічного розширення й високою термостійкістю, у цьому їх перевага перед іншими окислами [65]. Як і всі аморфні речовини НКС при нагріванні до температури вище 1200 °С кристалізується зі зменшенням об`єму — це його друга перевага перед порошками окислів оболонкових форм, тому що внаслідок часткової кристалізації
Порошки НКС
Позначення | Фракція | порошку | Позначення | Фракція | порошку |
Зернистість, мм | Номер сита, що обмежує фракцію | Зернистість, мм | Номер сита, що обмежує фракцію | ||
Дуже | 1,6 | 2-1,6 | Середній З | 0,315 | 0,5-0,315 |
грубий ОГ | Дрібний М | 0,16 | 0,315-0,16 | ||
Грубий Г | 1,0 | 1,6-1,0 | Тонкий Т | 0,063 | 0,063 — |
Великий ДО | 0,5 | 1-0,5 | (пилевид | і дрібніше | не ограни |
ний) | чено |
тільки поверхневого шару оболонка легко відділяється від поверхні сталевих виливків
Напівбезперервний процес одержання бруса НКС і технічні умови (ТУ 21-55-52-80) на порошки розроблені ГОСНИИКС ( м. Ленінград). У табл. 6.4 наведені відомості із цих ТУ
.. Згідно ТУ через сито № 0063 повинне проходити не менш 98 % по масі пилоподібного НКС. Слід зазначити, що для одержання якісної поверхні оболонки зернова сполука повинен бути різнорідним, а зміст зерен розміром 10 мкм і менш повинне бути більш 20
%.
Зерновій сполука (оптимальний) пилоподібного НКС:
Електрокорунд (аа1
і
) одержують у дугових печах і підрозділяють на нормальний (чорний) і білий. Нормальний, одержуваний відбудовної плавкою бокситів, містить 4-6 % шкідливих домішок (табл. 6.5), що знижують його температуру плавлення й хімічну стійкість. Білий електрокорунд може містити до 6 % алюмінату натрію у вигляді щодо м`яких включень. При дробленні злитків і седиментационном поділі алюмінат натрію осідає в пилоподібній фракції
.
Таблиця 6.5.
Хімічний склад електрокорунду, %
Марка єлектро-. коруида | А1 2 0 3 | Fe z 0 3 | Si0 2 | тю 2 | Сао | Mgo | Na z O |
Нормаль | 93,50— | 0,7—1,68 | 0,64— | 1,7—2,71 | 0,58— | 0,10— | _ |
ний ЄН | 96,08 | 1,68 | 0,74 | 0,28 | |||
(чорний) | |||||||
Білий ЄБ | 99,46 | 0,07 | 0,2 | 0,03 | 0,23 |
Алюмінат натрію зі сполучним Si0
з ЄТС при прожарюванні оболонок або заливанню в них розплаву утворюють на поверхні зерен основи сполуки типів Na
0- Al
0
-4Si0
(жадеит) з темпі-
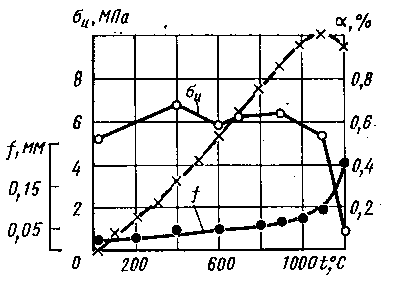
Рис. 6.6. Властивості оболонки з білого електрокорунду, що містить, % по масі: 0,68 Sto
, 0,15 СаО, 0,14 Ре
0,,.
0,34 (Najo + ДО
ПРО) зі сполучним гель SЮ
. про
— межа міцності при вигині, МПа; f-стріла прогину зразків, мм (відстань між опорами 60 мм при навантаженні 1,5 кг).
.
ратурой плавлення 1060 °С и Na
O-Al
0
-6Si0
(альбіт), що плавиться при температурі 1100 °С. Це приводить до розм`якшення оболонки при температурі 1060°С и різкому падінню міцності їх при 1200 °С [58] (мал. 6.6).
Електрокорунд хімічно стійкий, не утворює питтинга. Тому що розширення, при нагріванні плавне, оболонка має достатню термічну стійкість і її можна заливати в гарячому виді без опорного наповнювача. Для суспензій застосовують суміші дорогих класифікованих порошків білого електрокорунду, наприклад, суміш із порошків М-5, М-10, М-40 і М-50 у кількості відповідно 30, 28, 30 і 12 % по масі. Обсипають перший шар зернистим білим електрокорундом № 20, а наступні шари № 50 або сумішшю зеренрМЬ 40 і 63 у співвідношенні 1:1.
Для одержання хімічно стійкої оболонкової форми бажане застосовувати в якості її основи й сполучного той самий вогнетривкий окисел. Таке сполучне для електрокорунду — окси-нітрат алюмінію. З метою економії дорогого білого електрокорунду можна один або два лицювальні шари оболонки виготовити з білого, а наступні з нормального електрокорунду (див. табл. 6.5).
Не можна застосовувати глинозем (уА1
0
) для оболонкових форм і стрижнів, тому що він внаслідок активної хімічної взаємодії з окислами сплавів утворює пригар і питтинг на виливках. Крім того, при прожарюванні й при заливанні форм відбувається необоротне поліморфне перетворення ya1
0
->- аА1
0
зі зменшенням об`єму, тому що щільність першого р
= 3700 кг/м
, а другого — Ра = 4000 кг/м
Окис магнію (Mgo) одержують випалом природного магиезита Mgc0
при 1500—1600 °С. З
возгоняется, а шматки окису магнію розмелюють до потрібної зернистості. Використовують Mgoj для хімічно стійкої оболонки при заливанні високомарганцевих сталей
Кращими сполучними для магнезитових форм і стрижнів є азотнокислий магній і азотнокислий кальцій, тому що хімічна природа вогнетривкої основи й сполучного однакова. Можливе застосування єтилсиликатного сполучного орг-1 (див. с. 210), тому що воно слабко реагує з окисом магнію, особливо при температурах, близьких до нуля. Хімічна стійкість таких оболонок
до високомарганцевим сталям пояснюється утвором форстериту (2Mg0-si0
) на поверхні зерен магнезиту
У вакуумі при температурах розплавів на залізній або нікелевій основах окис магнію возгоняется. Це lie дозволяє примейять Mgo для форм, що заливаються ввакууме.
Сполуки окислів. Найболее широке прйменение одержали алюмосилікати — муллит, високоглиноземйстий шамот, ди стін-силлиманит.
Муллит 3Al
0
-2Si0
невеликий коефіцієнт, що має, термічного розширення (див. табл. 6.2), стійкий при високих температурах. У закордонній практиці його широко застосовують для форм. Запаси природного муллита обмежені. Однак він утворюється в шамоті при випалі каоліну, що містить у своїй сполуці не менш 36 % окису алюмінію
Високоглиноземистий шамот 3A1
0
-Si0
, одержуваний випалом каолінових глин, складається із двох фаз — муллита й кристобаллита у вигляді стеклофази.
У СРСР випускають шамот наступного хімічного складу, % по масі: не менш 36 А1
0
; 60 Si0
; 2,0 Ti0
; 1,5 Fe
0
; 0,5 СаО; 0,4 Mgo; 0,15 ДО
0; 0,15 Na
0. Огнеупорность — більш 1750 °С; вологовбирання — менш 5 % (ТУ 37.002.0010—80).
Нижче наведена зернова сполука шамоту марок 0315 і 063:
Перший (лицювальний) шар оболонок слід обсипати зернистим шамотом марки 0315, а наступні шари — шамотом марки 063. Для обсипання шару суспензій застосовують шамот із кристалічним кварцом, що збільшує термостійкість оболонки, тому що її розширення становить 1,0—1,1 % замість 1,4—1,5 % при використанні для обсипання кристалічного кварцового піску
Силлиманитовая група алюмосилікатних сполук включає силлиманит, андалулузит і дистен-силлиманит (кіаніт). Вони мають однакову форму Al
0
*Si0
, але різняться поліморфним станом
Найбільше широко застосовують концентрат дистен-силлиманито-вий марок КДСЗ (зерновий) й КДСП (пилоподібний) зі змістом 57/ ° про А1
0
; 20
; 2. При 1300—1350 °С у дистен-силлиманите йде реакція утвору муллита з виділенням Si0
і збільшенням об`єму до 15 %. Тому перед виготовленням оболонок дистен-силлиманит обпалюють при температурі понад 1000 °С для часткової його муллитизации, чому сприяють домішці лужноземельних металів
Слід обертати увага на форму зерен КДСП. При одержанні його струминним мливом без наступного обкатування в кульових млинах різко погіршується якість поверхні виливків
У ряді випадків дистен-силлиманит використовують замість пилоподібного електрокорунду
Циркон (силікат цирконію) Zr0
*Si0
, зустрічається в ряді країн (наприклад, в Австралії) у вигляді природних цирконових пісків. У СРСР циркон одержують як побічний продукт збагачення титаномагнієвої руди. Поставляють концентрати цирконовий порошкоподібний (КЦП), тонкодисперсний (КЦПТ) і зернистий (КЦЗ), пропоновані вимоги до яких наведені в табл. 6.6 (згідно ОСТ 48-82-81).
Таблиця 6.6.
Вимоги до циркоиовому концентрату
Показник | Норма для | марки | |
кцп | кцпз | КЦПТ | |
Зміст, % по масі, не більш: | |||
двоокиси цирконію, не менш | 65 | 65 | 60 |
окиси заліза | 0,09 | од | Не норми |
руется | |||
двоокиси титану | 0,3 | 0,4 | Те ж |
окиси алюмінію | 1,8 | 2,0 | » |
пятиокиси фосфору | 0,14 | 0,14 | » |
тория і урану | 0,1 | 0,1 | 0,1 |
вологи | 0,5 | ||
Питома поверхня, м 8 /кг | Не нормується | 500 |
Примітка. Безпекова-радіаційно-безпечна норма змісту долгоживущих природних елементів у цнрконовом концентраті менш 1 нки/г гарантується технологією виробництва
Регенерати — зернисті матеріали, одержувані з оболонок, що відробили, їх застосовують для обсипання третього й наступних шарів суспензій. Від сухих шматків оболонок відокремлюють постійним магнітом металеві (залізні) складові, далі оболонки подрібнюють, отриману крихту розділяють по фракціях. Для розсіву можна застосовувати барабанне сито (мал. 6.7) [92].
Регенерат оболонок із кристалічного кварцу ( до 70 %) має форму зерен, подібну зерен свіжого піску. Доцільно використовувати конгломерати зерен середнім розміром 0,6-1,6 мм для обсипання третього шару. Наступні шари також обсипають регенератом, але розміри зерен його, як у свіжого піску, або трохи більше. При такому використанні регенерату товщина чотиришарової оболонки збільшується на 20-40 %, руйнівне навантаження збільшується на 15-35 %, хоча сг
зразків небагато знижується 192].
Регенерати НКС характерні тим, що природа основи й плівок сполучного однакові. Використовують зерна після розсіву здрібненої оболонки по двом варіантам: без додаткової обробки для обсипання третього й наступного шарів; після мокрого збагачення для зниження до 0,2 % окиси заліза (яка є в поверхневому шарі оболонки) і відділення залишків пилоподібних
Рис. 6.7. Барабаииое сито:.
1 — бункер; 2 — шнек; 3 — барабан; 5 — електродвигун; 6 — редуктор; 7 — ящики для придатного матеріалу; 9 — ящик для відходів
.
складових. Більш високий зміст окису залоза знижує температуру розм`якшення оболонки [3].
Регенерат електрокорунду одержують після розчинення плівок двоокиси кремнію у водяному розчині їдкого лугу. Спосіб заснований на тому, що аморфний двоокис кремнію сполучної плівки розчиняється в їдкому лузі з утвором водорозчинних силікатів, а зерна електрокорунду практично не взаємодіють із лугом. У лузі також не розчиняється й дистен-силлиманит, який часто застосовують як замінник дорогого пилоподібного електрокорунду. Після перекладу плівок сполучного в розчинне рідке скло пульпу промивають, нейтралізують, сушать, класифікують і зерно використовують для обсипання. Цей спосіб має недоліки: регенерує тільки шліф-зерно, а найдорожчі й дефіцитні мікропорошки й зерна .
Відомий також спосіб, що полягає в оттирке плівок із зерен корунду при вібродинамічному впливі на пульпу, що полягає із трьох частин розмелених корундових оболонок і однієї частини води (30 J. Оттирка дозволяє використовувати й мікропорошки (>5 мкм). Після активації продукту соляною кислотою його використовують із добавками, свіжого електрокорунду для виготовлення оболонкових форм
Підготовка матеріалів основи. Підготовка матеріалів основи включає дроблення, мливо, промивання, хімічну активацію, прожарювання й просівання
Мливо. Набули застосування два способи млива:, що мелють тілами й без тіл, що мелють,
Перший спосіб — мливо в кульових або вібраційних млинах. Продукт одержують окатанной форми, розосередженої зернової сполуки. У вібраційних млинах матеріал одночасно й стирають. Продуктивність вібраційних млинів в 10-20 раз вище, чим кульових, а забруднення матеріалу продуктами зношування
куль менше. Другий спосіб — мливо в струминних установках. Здрібнювання відбувається при зіткненні зерен, що рухаються назустріч один одному з надзвуковою швидкістю; пилоподібний матеріал не забруднюється залізом, однак його зерна мають осколкову форму, що суттєво погіршує робочу поверхню оболонок
Пилоподібні матеріали, отримані першим і другим способами при однаковій питомій поверхні зовсім різні по технологічних властивостях. Для одержання суспензії однакової в`язкості в 1 л єтилсиликатного сполучного можна замішати до 2,5—3,0 кг пилоподібного кварцу вибропомола, а струминного — в 2 рази менше. Оболонки з матеріалу струминного млива пухкі, з низькою міцністю й великою відкритою пористістю, тому виливки виходять із шорсткуватою поверхнею
Раціонально спільне застосування описаних способів млива: попереднє струминне мливо до питомої поверхні 300— 250 м
/кг із наступним здрібнюванням і обкатуванням зерен у вібраційних млинах до питомої поверхні 400—600 м
/кг. Короткочасне обкатування незначно забруднює матеріал, але суттєво поліпшує форму зерен
Останнім часом запропонований принципово новий спосіб млива в планетарних млинах, у яких можливо безперервне здрібнювання матеріалів без, що мелють тіл
Пилоподібні складові суспензій не можна промивати, тому що тонкодисперсние частки, що позитивно впливають на міцність і шорсткість поверхні оболонок, несуться водою
Сушити пісок найбільше доцільно в установках псевдокипящего шару з обладнаннями для його охолодження й пневматичного транспортування до місця споживання. Для сушіння пилоподібних матеріалів рекомендують ті ж Печі, що й для прожарювання
Просівання. Пилоподібні матеріали слід просівати через сито № 0063 або 005, у барабанних або вібраційних установках [14].
Прожарювання. Матеріал, забруднений намеленим залізом і іноді органічними домішками, прожарюють в окисному середовищі при 900—950 °С; залізо окисниться до Fe
0
і не виявляє шкідливої дії на суспензію
Магнітна обробка. Намелене залізо при одержанні пилоподібних матеріалів видаляють магнітною обробкою суспензій. Для цього у внутрішніх стінок змішувача зміцнюють дві-три пластини, що намагнічуються електромагнітами, розташованими із зовнішньої сторони. При безперервному перемішуванні частки заліза відриваються від зерен пилоподібного матеріалу й осідають на пластинах
Готування шликера. При використанні матеріалів, забруднених окислами заліза й лужних металів, доцільно їх обробку проводити при готуванні шликера, використовуваного надалі для одержання суспензії. У подкисленную воду замішують пилоподібні вогнетриви, наприклад, кварц пилоподібний [781. Відомі два способи готування шликера:.
1) в 0,7—0,8 об`єму змішувача наливають подкисленную воду й у неї при перемішуванні порціями насипають пилоподібний матеріал до співвідношення твердої й рідкої складових 4:1 по масі; температура шликера внаслідок тертя підвищується, і при t = = 60 °С подають воду в сорочку бака, прохолоджуючи шликер до 35— 37 °С; 2) у ємність наливають подкисленную воду й у неї всипають пилоподібний вогнетрив, витримують до готування суспензії 1-2 сут.
Переваги шликерного способу готування суспензії пояснюють тим, що відбувається нейтралізація заліза, а також лужних і лужноземельних домішок. Крім того, поверхня зерен кварцу гидратируется з утвором Si(OH)
, і руйнуються грудочки. Цей спосіб дозволяє зменшити витрата єтилсиликата в 1,3-1, 5 рази, побільшати живучість водно-спиртових суспензій до 5-7 сут, і зменшити схильність оболонок до утвору тріщин при сушінні
Необхідну масу соляної кислоти (г) на 1 кг пилоподібного матеріалу визначають по формулі
де xfe — зміст заліза в пилоподібному вогнетриві, % по масі
Сполучні матеріали оболонок. Властиво сполучним оболонкової форми служить тугоплавкий неорганічний окисел або сполуки окислів, що утворюються зі сполучних розчинів при сушінні н прожарюванні оболонок. Їх розділяють на кислі, амфо-терние й основні (табл. 6.7).
Таблиця 6.7.
Характеристика вихідних сполучних матеріалів оболонок
Характеристика | Сполучний окисел | |||
Вихідний матеріал | Содер. жание. связу. ющего. окисла,. %. по масі | Застосовувані розчинники | Хімічне властивість | Температура плавлення або розкладання, ®С |
ЄТС марок 32, 40, 50 | 32-.50 | Органічні | Кислий | 1713 |
Фосфати — кислі солн ор | (наприклад, спирт нли ацетон). Вода | » | 1600 | |
тофосфор ний кислоти Комбінації сполучних ЄТС | Сума | » | 1700 | |
з фосфатними Біхромат амонію | 10—12 | » | Амфотерний | 1500. 2135 |
Оксихлорид хрому | 10—12 | Спнрт, вода | » | 2135 |
Кальцій азотнокислий | Метиловий спнрт | Основний | 2800 |
Примітки. 1. Усі вихідні матеріали — рідини, кальцій азотнокислий кристалічна сіль
2. Метиловий спирт отрутний
Кислі сполучні широко предсталени розчинами. єтилсиликата, з яких утворюється в оболонці аморфний двоокис кремнію. Форми з ним досить міцні й не утворюють пригару на виливках з углеродистих сталей, мідних і алюмінієвих сплавів. До кислих також ставляться фосфати металів і комбінації єтилси-ликатного сполучного сфосфатним.
Єтилснликати (ЄТС) — прозора або слабоокрашенная рідина із заходом ефіру. Це продукт реакції етилового спирту із четиреххлористим кремнієм при безперервному їхнім змішуванні й охолодженні в реакторі. Реакція етерифікації, або єфиризации, може бути схематично представлена наступним рівнянням (якщо застосовують збезводнений спирт) [413:
де (C
H
0)
Si — етиловий ефір ортокремниевой кислоти з температурою кипіння 165,5 °С, називаний також тетраєтоксисиланом, або моноєфиром.
При використанні в реакції спирту, що містить деяка кількість води, остання частково гидролизует продукти єтерн-фикации, а молекули, що утворювалися, конденсуються (поєднуються) з виділенням води, яка знову вступає в реакцію гідролізу. У результаті утворюється суміш сполук (табл. 6.8), яку називають технічним ЄТС. Він не містить двоокиси кремнію (Sio
), але, тому що Si0
- властиво сполучне оболонки, умовна кількість його в ЄТС прийняте в позначенні марки продукту
Для ливарного виробництва вітчизняна хімічна промисловість випускає ЄТС двох марок: 32 і 40. Технічні вимоги зазначені в табл. 6.9. Істотні переваги ЄТС 40 перед ЄТС 32 полягають у тому, що сполучні розчини першого при меншому змісті в них двоокиси кремнію повідомляють оболонки більшу міцність внаслідок більш високого ступеня конденсації. Отже, для ливарного виробництва доцільно випускати тільки ЄТС 40 і ЄТС 50.
Будова молекул ЄТС 32 і ЄТС 40 лінійне, наприклад,
ЄТС 40 і ЄТС 32 не можуть бути сполучними, тому що не повідомляють міцність оболонкам. Для одержання сполучних розчинів їх необхідно гидролизовать для того, щоб лінійна будова молекул перетворити в розгалужене й частково зшите або в колоїдний розчин (с. 211, — 212).
З порівняння сполук вітчизняних ЄТС із закордонними випливає, що останні містять приблизно вдвічі менше мономера. Відомо, що в реакцію гідролізу вступають насамперед і легше.
Сполуки, які можуть входити в ЄТС
Формула | Mac. однієї молекули | _ -. ca, г ; єтоксиль-. НИХ. груп | Содер. жание. єтоксиль-. иих. груп,. % ПО. масі | Sio a , % по масі |
(C. 2 H s O) 4 Si * | 208 | 180 | 86,6 | 28,8 |
(QhsoSio | 342 | 270 | 79,0 | 35,1 |
(C 2 H 5 0) 8 Si 2 0 | 452 | 336 | 74,3 | 37,1 |
(C,H,0)usia | 610 | 450 | 73,9 | 39,3 |
(C 2 H 5 0) 12 Si 5 0 4 | 744 | 540 | 72,5 | 40,32 |
(Qheojusigog | 836 | 588 | 70,3 | 41,0 |
(C 2 H 5 0) le Si 7 O e | 964 | 672 | 69,99 | 41,5 |
(QH e 0) 18 Si 8 0 7 | 1092 | 756 | 69,0 | 41,88 |
(CHsoaesigog | 1220 | 840 | 68,8 | 42,12 |
(Oih.ojesija | 1348 | 924 | 68,5 | 42,43 |
(Qhgojaisiuoio | 1476 | 1008 | 67,5 | 42,64 |
(C 2 H 5 0) 28 Sii 2 0n | 1604 | 1092 | 68,0 | 42,83 |
(C2H 5 0) 28 Si ls Oi 2 | 1732 | 1176 | - 67,8 | 42,95 |
(QheojSiuoia | I860 | 1260 | 67,7 | 43,076 |
Таблиця 6.9.
Технічні вимоги на ЄТС
ЄТС 32 | ЄТС 40 | ЄТС 50 | |
Показник | ТУ 6-02805-74 | ДЕРЖСТАНДАРТ 5.1174-71 | |
Зовнішній вигляд | Рідина, допу | Рідина від безбарвного до | |
скается опалі | ясно-жовтого кольору | ||
сценция | |||
Щільність при 20 °С, кг/м 8 | 1000 | 1040—1070 | 1180—1250 |
В`язкість кінематична при | Не більш 1,6 | 3,5—6,0 | 50—200 |
20 °С, мкм 2 /з | |||
Зміст, % по масі: | |||
НС1 | 0,1 | 0,1 | ==£0,1 |
Si0 2 | 30—34 | 40±2 | 51—54. |
Зміст, % по масі: | «=2,0 | Не аналізується | 2 |
фракції з температурою | |||
кипіння до 110 °С | |||
єтоксильиих груп | - | 60-72 | 57-61 |
(З 2 Н 6 0) | 50-70 | ||
тетраєтоксисилана (ефіру | Немає | ||
ортокремниевой кислоти) | ssl,5 | 2 | |
етилового спирту | - | ||
Тривалість гелеоб- | - | 150-210 | - |
разования, хв |
усього мономери, вони ж виділяють при гідролізі найбільша кількість спирту. Цим можна пояснити утруднення при використанні імпортного ЄТС 40, що містить невелику кількість мономера, для одержання суспензії без уведення органічного розчинника, тому що гідроліз іде дуже в`януло. Для інтенсифікації
.
Кремнезоли, стабілізовані Naoh
Місце виготовлення | Концен. трация. Naoh,. % по масі | Концентрація Si0 2 , % по масі | р, кг/м 3 | ph | Розмір колоїд-- иих Часток, нм |
МХТИ нм. Д. І. Менделєєва Фірма Monsanto | 0,28-0,65. 0,42 | 9,03-39,8. 27,3 | 1052-1287. 1197 | 9,2-9,6 9,35 | 10-15. 10 |
гідролізу слід додати ~10 % взаємного розчинника -спирту або ацетону
Кремнезоли [27] (табл. 6.10) одержують методом видалення іонів натрію, пропускаючи розведений силікат натрію (рідке скло) через катионитовую смолу з наступним нагріванням отриманих продуктів у лужному середовищі й подальшим концентруванням
Кремнезоли — колоїдні дисперсії двоокису кремнію у воді, стабілізовані гідроокисами лужних металів. Вони містять силанольние групи s Si — ВІН, які поліконденсуються з утвором міцних силоксанових зв`язків, наприклад, = Si- Про-Si =; перезаряджаються у воді, подкисленной соляною кислотою. Кремнезоли, розведені водою до 3,5—6 % Si0
, у комбінації з водноспиртовими єтилсиликатними сполучними при сполученому способі готування суспензій суттєво збільшують міцність оболонок, що дозволяє знизити витрата ЄТС 40 і виключити органічні взриво- і пожароопасние рідини (розчинники). Кремнезоли знаходять застосування й для формування лицювального шару оболонок. Недолік кремнезолей — втрата сполучних властивостей після замерзання
Фосфати. Однозаміщені солі ортофосфорної кислоти железофосфат [Fe(H
P0
)
], алюмохромфосфат [А1
Сг(Н
Р0
)
], же-лезоалюмофосфат Lfeal
(H
P0.i)
3 мають сполучні властивості [27, 45, 53]; добре розчинні у воді й нерозчинні в спиртах і ацетоні; при сушінні здобувають полімерні структури типу Ме„0
Р
0
Н
0, а після прожарювання Me
0
P
0
, тому що віддаляється кристаллизационная вода; міцність оболонок підвищується. Двузамещенние.солі ортофосфорної кислоти не мають сполучні властивості
Відоме до 50-х років алюмофосфатное сполучне (АФС), використовуване у виробництві вогнетривів, не одержало застосування в лиття по виплавлюваних моделях, тому що поліморфні форми, що утворюються при прожарюванні, перетерплюють перетворення зі зміною об`єму аналогічно кристалічному кварцу. АФС старіє зі збільшенням в`язкості й зниженням сполучних властивостей і твердіє тільки при 300—400 °С. Із уведенням у нього одного з металів Fe, Cr, Ni, Mn, Са, Mg одержують сполуки типу Ме
0
-А1
0
лР
0
. Вони твердіють при 20—30 °С у процесі сушіння на повітрі й при прожарюванні
Однозаміщені фосфати стабілізують суспензії з ЄТС сполучним без уведення в останні органічних розріджувачів Алюмометаллофосфати використовують як самостійне сполучне для оболонок, так і в комбінації з ЄТС. При цьому розчини з ЄТС містять >10 % двоокиси кремнію [62].
Амфотерні сполучні — це розчини основних солей (оксисолей) алюмінію, хрому, цирконію (оксицитрати, окси-хлориди) і розчини цирконийорганического сполуки ( тетра-хлорєтилцирконати). У процесі сушіння й прожарювання оболонок цементація зерен відбувається внаслідок утвору окислів хрому, алюмінію, цирконію на поверхні зерен. Сутність одержання оксисолей заснована на відновленні хромового ангідриду етиловим спиртом (або ацетоном) у присутності соляної кислоти згідно з рівнянням
Основні сполучні. Представники цієї групи сполучних — азотнокислий кальцій і рідке скло. Азотнокислий кальцій розчинний у метиловому спирті (див. табл. 6.7), після прожарювання оболонки він утворює окис кальцію — властиво сполучне, яке в комбінації з основою із плавленой або спеченной окису магнію або з очисью кальцію дає можливість изгото-ш1ять високовогнетривкі оболонки, хімічно стійкі до сплавів з основними властивостями
Рідке скло (ЖС) також відносять до основних сполучним, тому що його водна витяжка після прожарювання оболонки — лужна; одержують розчиненням у гарячій воді при підвищеному тиску роздробленої силікату-брили. Останню виготовляють найбільше часто сплавкою кремнезему із содою
ЖС може бути натрієвим, калієвим або літієвим
Застосування ЖС для «упрочняющего» шару оболонки не відповідає вимогам одержання якісних виливків. При прожарюванні ЖС плавиться при 793 °С, а розм`якшується при більш низькій температурі, тобто зовнішній шар із цим сполучним при прожарюванні Оболонки й заливанню в неї стали повністю втрачає міцність. При охолодженні ж до температури нижче 600 °С міцність таких оболонок у багато разів вище міцності їх зі сполучним з ЄТС, а усадка внаслідок рідинного спікання зовнішнього шару більше, ніж шарів зі сполучними, одержуваними з ЄТС (мал. 6.8). Втрата міцності при нагріванні оболонок і висока міцність при одночасній високій усадці зовнішнього шару, що остигає, оболонки завжди приводить до викривлення контуру виливків і часто до тріщин у них (мал. 6.9). Такі виливки неприпустимо називати точними
Органічні розчинники-розріджувачі (РР) наведені в табл. 6.11. Вони, як правило, містять воду, яку необхідно враховувати при розрахунках сполуки сполучних
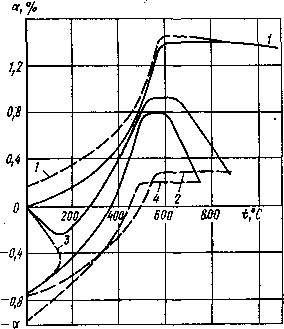
Рис. 6.8. Дилатометричні криві ободочек:.
1 — єтилсиликатная; 2 — жидкостекольная; 3,.
4 — єтилсиликатние з «упрочияющим> жидкосте-кольиим шаром відповідно при виплавлении.
моделей і при нагріванні й ихлажденин;--.
нагрівання; — — — — охолодження
.
Особливо швидко обсихають суспензії з ацетоновим РР, хоча міцність оболонок вище, чим при використанні тільки етилового спирту. Це пояснюється тим, що деяка частина ацетону утворює ацета-чи з ЄТС. Швидке ж обсихання суспензій з ацетоном обумовлене його інтенсивним випаром, тому що температура кипіння ацегона 56,5 °С, а спирту 78,5 °З.
Запропоновано вважати нормою т
г,з — 30 з, тобто час, протягом якого до суспензії на блоках ще добре прилипають обсипочние зерна 14, 49]. Для зашиті суспензій з ацетоном від його швидкого випару, використовують антивипарники — вищі жирні спирти (ВЖС) зі змістом у молекулі 17—19 атомів вуглецю. Кількість антивипарника збільшують зі зменшенням змісту двоокиси кремнію в сполучному (табл. 6.12, мал. 6.10).
Добавки. Добавки вводять у пилоподібний матеріал при підготовці шликера; у сполучний розчин при його готуванні; у суспензію при змішанні сполучного розчину з пилоподібної складової; в обсипочний матеріал; у ванни з гарячою водою длй виплавления моделей (табл. 6.13).
.
Таблиця 6.11
Рис. 6.9. Схеми утвору дефектів на виливках в «зміцнених» жидкостекольним сполучним оболонках:.
а — витріщання шару з ЄТС при виплавлении моделей гарячим повітрям; б — прогин (зминання) оболонки при прожарюванні внаслідок повної втрати міцності «упрочняющего» шару: 1 — шар з ЄТС сполучним; 2 — «упрочняющий» шар; 3 — сипучий наповнювач
.
Таблиця 6.12.
Тривалість обсихання суспензії т
б
(с) на блоках моделей н міцність зразків оболонок ст
(МПа)
Зміст Si0 2 | % по масі, в | сполучному типу орг-2 | |||||||
те а CL про а> m | РР, % по масі | 5 | 7 | 10 | 14 | ||||
о§. ЯО. | ‘‘обидві | °И | т обс | °И | т обс | °і | т обс | ||
1 | Ацетон — 100 * | 3 | 2,0-2,3 | 4 | 4,1-4,2 | 6 | 5,2-5,3 | 8 | 6,0-6,5 |
2 | Ацетон — 60, етиловий спнрт- 40 | 8 | 1,8-1,9 | 11 | 2,8-3,0 | 14 | 3,4-3,7 | 17. | 5,0-5,2 |
3 | Ацетон — 20, етиловий спнрт — 80 | 29 | 33 | 38 | 42 | ||||
4 | Етиловий спирт- 100 | 48 | 1,6-1,8 | 55 | 2,1-2,3 | 60 | 2,5-2,8 | 60 | ПРО. 1. оо. З |
* Спирт, що виділився при гідролізі, у розрахунки ие прийнятий
.
Особливе місце займають поверхнево-активні речовини (УПАВШИ) у технології виготовлення оболонок з водно-спиртових суспензій
(називаних водними), УПАВШИ поліпшують змочування- моделей і зменшують в`язкість суспензій 157, 103].
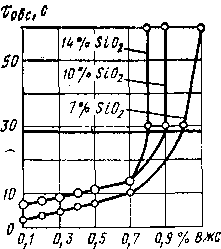
Рис. 6.10. Межа обсипаемости t
g
блоків моделей залежно від змісту умовного S10
у розчині типу орг-2.
.
Добавка в суспензії 0,08-0,2 % поли-винилбутираля до спиртового сполучного типів орг-1 і орг-2 підвищує седимента-ционную стійкість суспензій, газопроникність і міцність оболонок [106].
Введення добавки | Добавка | Зразкове кількість добавки,. % по масі | Призначення |
Прн підготовці шлнкера нз пилоподібного матеріалу | Соляна кислота НС1 | Див. розрахунки | Нейтралізація домішок |
Для гідролізу ЄТС | Вода Н 2 0 | Те ж | Одержання сполучного з -ЄТС 40 або ЄТС 32 |
У воду прн гідролізі ЄТС | Соляна кислота НС1. Сірчанокислий алюмнннй A1 2 (S0 4 ) 8 18Н 2 0 | ». 0,1 до сполучного розчину | Каталізатор гідролізу й поликонден-сацнн. Підвищення стабільності сполучних розчинів н суспензій типів орг-1, 2, 3 v |
На початку готування водно-спиртової суспензії зі сполучним нз ЄТС | Поверхово-Ак-тнвние речовини: метаупон, суль-фанол, ДНС | До 0,22 до пилоподібної составлн-ющей суспензії | Змочування моделей суспензією, розрідження суспензії |
За 10—12 хв До закінчення прнго-товлення суспен‘ Єни | Поливннилбутн-Раль —■ розчин у Спирті | 0,08—0,5 до сполучного | Підвищення седнмёи* тацнонной стійкості суспензій і газопроникності оболонок |
Після готування суспензії | ВЖС | 0,5-1,2 | ■Уменьшение випару ацетону й спирту на блоках моделей і у ванні із суспензією |
При готуванні суспензії | Закис-Окис до- . бальта З03 ПРО4 | 2,6 до корундової суспензії | Підвищення механік ческих властивостей исва* риваёмости жаро* міцного - сплаву при заливанні у вакуум! |
В обсипання | Карбонат кальцію | 40—50 до обсипання | Розчинення у воді оболонок на алюмінієвих виливках |
В обсипочний матеріал | Поварена сіль Nacl | До 5 про до обсипання | Розчинення у воді залишків оболонок на алюмінієвих виливках |
У гарячу воду ( ~-Ю0°С) для виплавления моделей | Контакт Петрова V. | 0,1—0,2 об`єму води | Попередження омилення модельних сполук, захист ванн від корозії |
Введення в обсипання 30—40 % повареної солі або 40—50 % карбонату кальцію дозволяє разупрочнять оболонки у воді після них з&чивки, що важливо при одержанні виливків 139, 52] зі сплавів на алюмінієвій основі